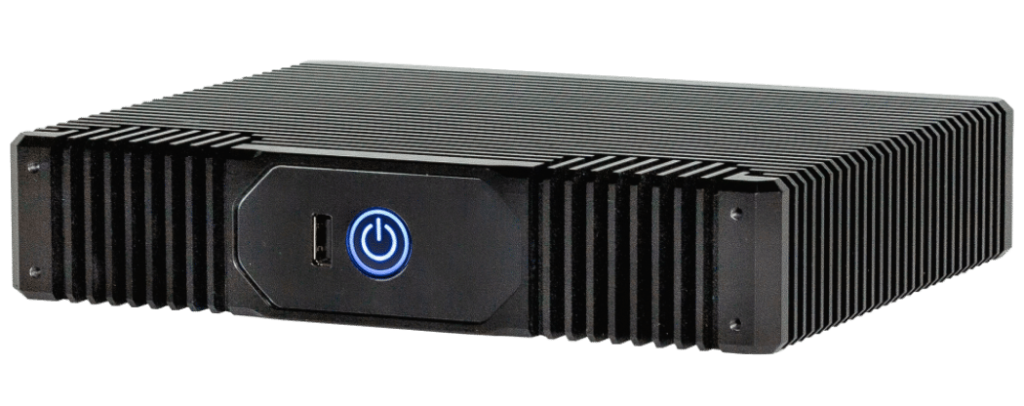
The birth of the Industrial Fanless NUC quickly followed the release of the consumer-focused Intel® Next Unit of Computing (NUC). The NUC packs the performance of a full-sized computer into a compact package. The NUC’s small size and impressive capabilities made it instantly appealing to professional users.
By developing some of the very first Industrial Fanless NUC enclosures. These units were thoughtfully designed with hardshell fanless technology for use outside of a temperature-controlled office environment. Since then, each new generation of NUC motherboards has increased the performance and potential of these compact systems. With those advancements has come even greater flexibility in the way industrial computer users are leveraging these mini-PCs.
A Brief History of the NUC
When Intel chose to leap into the burgeoning small-form-factor PC market in 2012 with its Next Unit of Computing platform, the move made waves. As the market leader in CPU manufacturing, it was surprising to see them take such a big step into distributing full systems.
But Intel’s commitment to their NUC line paid off. In the years that followed, Intel NUC hardware began to crop up in many forms, and other motherboard manufacturers started releasing their own versions.
Small-form-factor systems based on Mini-ITX and Pico-ITX boards were nothing new. But, the NUC offered a unique combination of size and performance that made it ideal for installation in space-constrained environments. In addition, previous generations of mass-produced, proprietary small-form-factor PCs often required customization to best serve a given application. In contrast, NUC offered a fixed I/O configuration that didn’t rely on utilizing onboard pin headers to achieve I/O for industrial applications.
What Makes a Industrial Fanless NUCs Different?
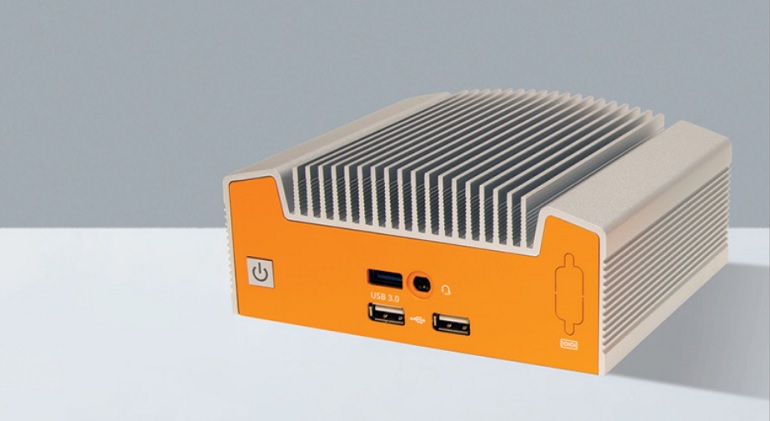
The most obvious departure from a consumer NUC to its industrial counterpart is the enclosure. Consumer NUCs utilize a mix of polycarbonate and plastics. Industrial NUC systems most commonly employ steel or aluminum construction. These materials allow them to better stand up to shock, vibration, or even impacts by machinery or tools.
The standardized form factor and aesthetic of the consumer NUC has become universally recognizable. Industrial NUC systems, on the other hand, frequently offer additional capabilities, like expansion bays for more storage, specialized add-on cards, or industry-specific I/O.
Industrial NUC enclosures look a little different than their consumer counterparts because they employ passive cooling technology. Most include design features such as cooling fins to dissipate heat. With no air being passed through the system, vent openings in the case are eliminated.
One of the most impactful reliability improvements that many industrial NUCs employ is the removal of all moving parts, including the fan and spinning platter drives. The use of mSATA and M.2 drives allow for a range of storage options, without the inherent vulnerabilities of hard disc drives (HDDs).
Engineering Reliability Into the Industrial Fanless NUC
Computer crashes are a frustrating experience for anyone, but the ramifications of unreliable industrial computers can cost a business an incredible amount of time and money. Hardware failures can bring a manufacturing line to a halt, resulting in unusable products, or rendering data inaccurate or inaccessible. A wide range of variables influences the reliability of computer systems. Industrial PC manufacturers have worked hard to eliminate the most common points of failure in order to maximize uptime.
The unique environmental concerns of industrial computer users extend beyond those that can be seen or felt. Devices being installed in and among other equipment must be protected from interference. Industrial Fanless NUCs may utilize double right-angle interfaces at enclosure joints to limit RF and electrostatic discharge (ESD). Anodized aluminum and nickel-plated steel parts, as well as specialized ESD shielding gaskets, further help to prevent interference.
Industrial fanless NUC systems use custom-machined heatsinks or heat pipes to transfer thermal energy from internal components directly into the system chassis. The surrounding air then dissipates the heat. The elimination of ingress points for airborne contaminants helps to keep out dust, grease, chemicals and corrosives. These substances can quickly build up on internal components and lead to overheating or electrical shorting.
Speaking of heat, operating temperature is another key concern in industrial computing. Consumer NUC motherboards all hover around 0°C for their specified low operating temperature, and 40-50°C on the high end. Motherboard manufacturers are beginning to experiment with wider ranges for use in less temperature-controlled environments. These types of extreme temperature applications are becoming increasingly common. Industrial computers are vital as more computing deploys at the edge. In these environments, temperatures can hover around freezing and/or reach well into the triple digits Fahrenheit.
NUC Lifecycle Differences
Industrial computing projects rely on component standardization to ensure consistent product delivery and performance. Many industrial certifications and regulatory tests also require a device to be locked down to a set configuration in order to be approved. However, consumer electronics, especially computer hardware, rarely feature a product lifecycle of longer than a year or two.
While consumer NUC systems offer a one to three-year lifecycle, some industrial NUCs provide a full five-year lifecycle. A longer product lifecycle means that components will be available for future orders or replacements and integrators can more easily standardize on a hardware configuration.
Connectivity Options
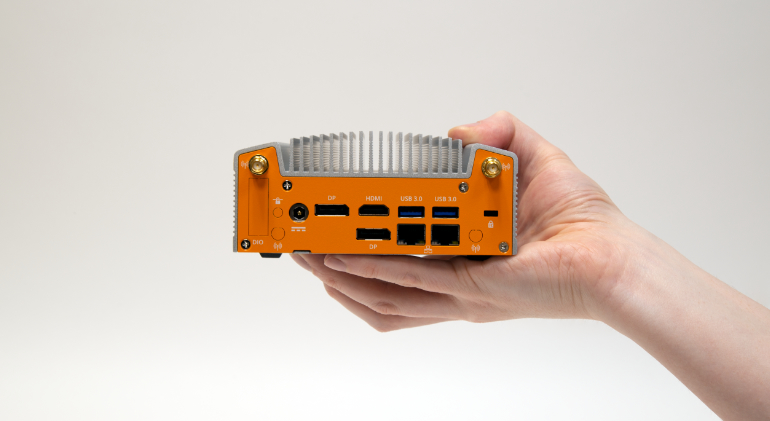
The final key difference between consumer and industrial NUCs is one of the first things that consumer computer users notice — the connection options. The connectivity needs of industrial users tend to be very different from those of the average personal computer user.
Legacy infrastructure integration in a machine shop or industrial automation application often requires the use of I/O connection standards commonly seen as antiquated in the consumer space. As an example, it’s not uncommon to find serial ports (COM) or even DVI ports on industrial computers. Digital input/output (DIO) is also a frequent feature in today’s industrial systems, allowing for versatile individualized programming and control.
Golden Margins –
Entire Range of Touchscreen Products
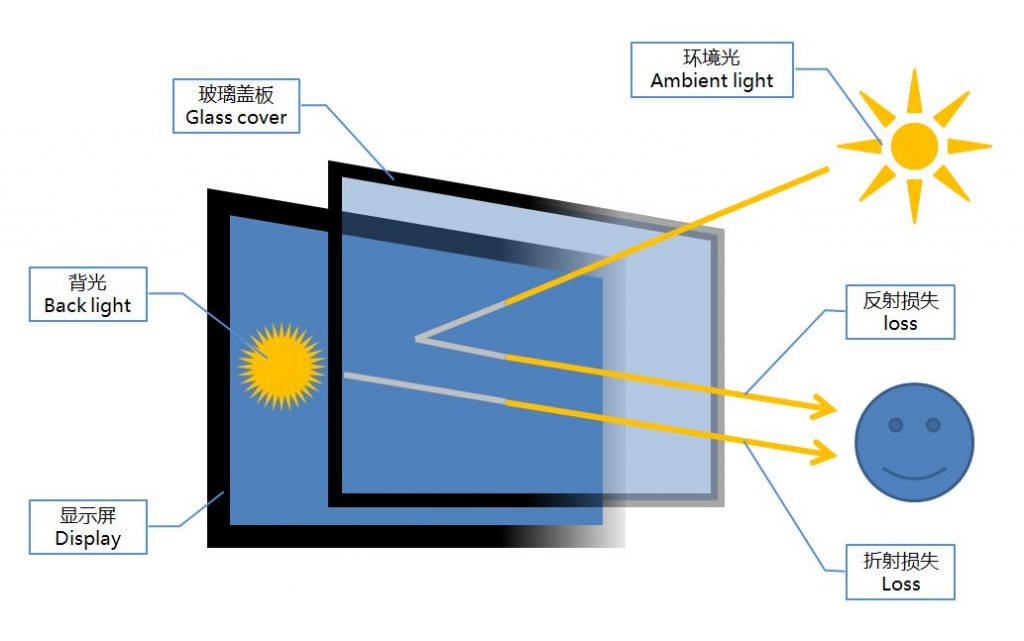
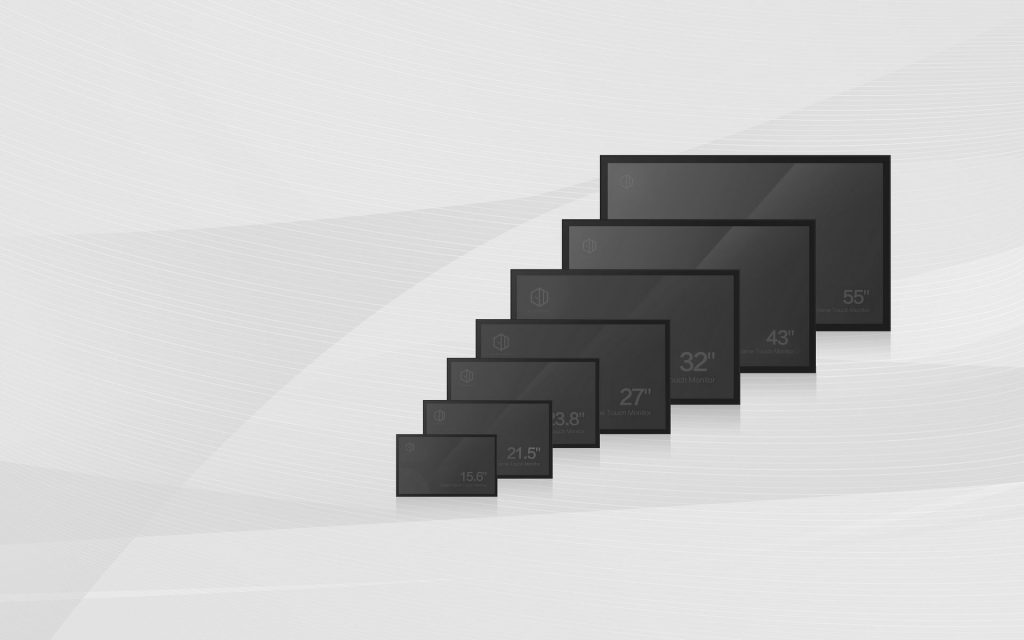
We hope you found these touchscreen or panel PCs fundamentals informative. Goldenmargins offers a broad selection of Industrial Touchscreen Monitors and Touch Panel PCs in various sizes and configurations, including medical touch screens, sunlight-readable touch screens, open-frame touch screens, and waterproof touch panels, as well as other unique touch screen or panel PC designs. You can learn more about our services HERE or by calling us at +86 755 23191996.
Comments (2,764)
mexican drugstore online: pharmacies in mexico that ship to usa – mexican rx online
mexican online pharmacies prescription drugs https://mexicaneasypharm.shop/# Mexican Easy Pharm
mexican border pharmacies shipping to usa
buying prescription drugs in mexico online https://mexicaneasypharm.com/# medication from mexico pharmacy
mexican drugstore online
п»їbest mexican online pharmacies https://mexicaneasypharm.shop/# Mexican Easy Pharm
mexican online pharmacies prescription drugs
http://cytpharm.com/# buy cytotec online
can i buy prednisone online without a prescription
https://cytpharm.shop/# CytPharm
prednisone brand name
https://dappharm.shop/# Priligy tablets
prednisone 50mg cost
https://cytpharm.shop/# CytPharm
prednisone 2.5 mg
https://kamapharm.com/# sildenafil oral jelly 100mg kamagra
prednisone 30 mg coupon
https://cytpharm.com/# buy cytotec online
online order prednisone
https://predpharm.com/# prednisone for dogs
prednisone 2 mg daily
http://semapharm24.com/# semaglutide tablets price
can you buy prednisone over the counter in mexico
https://cytpharm.shop/# buy cytotec online
generic prednisone for sale
https://kamapharm.shop/# sildenafil oral jelly 100mg kamagra
prednisone 20 mg purchase
https://dappharm.com/# dapoxetine price
compare prednisone prices
https://cytpharm.com/# buy cytotec
prednisone 15 mg daily
http://predpharm.com/# PredPharm
prednisone uk
http://dappharm.com/# dapoxetine price
20 mg of prednisone
https://farmasilditaly.shop/# gel per erezione in farmacia
comprare farmaci online con ricetta
http://farmabrufen.com/# BRUFEN 600 acquisto online
acquisto farmaci con ricetta
https://farmabrufen.com/# FarmaBrufen
acquisto farmaci con ricetta
https://farmatadalitaly.shop/# Farmacia online piГ№ conveniente
Farmacia online miglior prezzo
farmacia online [url=https://farmaprodotti.shop/#]Farmacie online sicure[/url] farmacia online piГ№ conveniente
https://farmasilditaly.shop/# pillole per erezione immediata
Farmacia online piГ№ conveniente
http://phmacao.life/# Players must be at least 21 years old.
The casino atmosphere is thrilling and energetic.
Gambling can be a social activity here.: taya777 login – taya777.icu
The casino industry supports local economies significantly.: taya365 – taya365 com login
taya365 [url=http://taya365.art/#]taya365 com login[/url] Live dealer games enhance the casino experience.
The casino experience is memorable and unique. https://winchile.pro/# Hay casinos en Santiago y ViГ±a del Mar.
https://taya365.art/# The poker community is very active here.
Many casinos provide shuttle services for guests.
Los bonos de bienvenida son generosos.: winchile.pro – win chile
Players often share tips and strategies.: phmacao com login – phmacao.life
Many casinos host charity events and fundraisers. https://phtaya.tech/# Live music events often accompany gaming nights.
http://phtaya.tech/# The ambiance is designed to excite players.
Players can enjoy high-stakes betting options.
Responsible gaming initiatives are promoted actively.: taya365 – taya365 login
taya777 app [url=http://taya777.icu/#]taya777 login[/url] The thrill of winning keeps players engaged.
The gaming floors are always bustling with excitement.: phtaya login – phtaya casino
https://taya777.icu/# Promotions are advertised through social media channels.
Resorts provide both gaming and relaxation options.
Promotions are advertised through social media channels. http://taya365.art/# High rollers receive exclusive treatment and bonuses.
Entertainment shows are common in casinos.: phmacao casino – phmacao
http://taya777.icu/# Entertainment shows are common in casinos.
Many casinos provide shuttle services for guests.
Players enjoy both fun and excitement in casinos.: phtaya login – phtaya casino
Casino promotions draw in new players frequently. https://phtaya.tech/# Entertainment shows are common in casinos.
jugabet casino [url=https://jugabet.xyz/#]jugabet[/url] Los juegos en vivo ofrecen emociГіn adicional.
http://phtaya.tech/# A variety of gaming options cater to everyone.
Game rules can vary between casinos.
Los jugadores pueden disfrutar desde casa.: jugabet casino – jugabet chile
Los pagos son rГЎpidos y seguros.: jugabet chile – jugabet casino
The casino experience is memorable and unique. http://phtaya.tech/# Some casinos feature themed gaming areas.
https://phtaya.tech/# The casino industry supports local economies significantly.
Visitors come from around the world to play.
The casino industry supports local economies significantly.: taya777 login – taya777 login
Las aplicaciones mГіviles permiten jugar en cualquier lugar.: jugabet.xyz – jugabet.xyz
https://phtaya.tech/# Some casinos have luxurious spa facilities.
Most casinos offer convenient transportation options.
phmacao club [url=https://phmacao.life/#]phmacao com[/url] The thrill of winning keeps players engaged.
Gambling can be a social activity here. https://phtaya.tech/# Loyalty programs reward regular customers generously.
Security measures ensure a safe environment.: taya777 login – taya777 login
http://taya777.icu/# Some casinos feature themed gaming areas.
Casino promotions draw in new players frequently.
Many casinos provide shuttle services for guests.: taya777 register login – taya777.icu
Slot machines attract players with big jackpots. http://jugabet.xyz/# Las mГЎquinas tragamonedas tienen temГЎticas diversas.
Los casinos celebran festivales de juego anualmente.: jugabet – jugabet casino
https://taya365.art/# Game rules can vary between casinos.
Players often share tips and strategies.
taya365 [url=https://taya365.art/#]taya365.art[/url] Cashless gaming options are becoming popular.
Slot machines attract players with big jackpots.: taya777 register login – taya777
The ambiance is designed to excite players. http://phmacao.life/# Many casinos offer luxurious amenities and services.
https://winchile.pro/# La ruleta es un juego emocionante aquГ.
Gaming regulations are overseen by PAGCOR.
Players enjoy both fun and excitement in casinos.: phmacao – phmacao.life
The casino atmosphere is thrilling and energetic.: phtaya casino – phtaya login
http://phtaya.tech/# Game rules can vary between casinos.
Casino promotions draw in new players frequently.
Responsible gaming initiatives are promoted actively. https://jugabet.xyz/# La ruleta es un juego emocionante aquГ.
Poker rooms host exciting tournaments regularly.: phtaya login – phtaya login
winchile casino [url=http://winchile.pro/#]win chile[/url] Los jackpots progresivos atraen a los jugadores.
Most casinos offer convenient transportation options.: taya777 login – taya777
https://phtaya.tech/# Casinos offer delicious dining options on-site.
Players can enjoy high-stakes betting options.
Players often share tips and strategies.: phtaya – phtaya
http://taya777.icu/# Casino visits are a popular tourist attraction.
The casino scene is constantly evolving.
La mayorГa acepta monedas locales y extranjeras.: winchile – win chile
taya777 register login [url=https://taya777.icu/#]taya777 app[/url] Visitors come from around the world to play.
http://taya777.icu/# The poker community is very active here.
The Philippines has a vibrant nightlife scene.
Entertainment shows are common in casinos.: taya365.art – taya365 com login
http://phmacao.life/# Gambling regulations are strictly enforced in casinos.
Visitors come from around the world to play.
The casino scene is constantly evolving.: phtaya login – phtaya
Security measures ensure a safe environment.: phtaya casino – phtaya
http://taya365.art/# The poker community is very active here.
Promotions are advertised through social media channels.
Manila is home to many large casinos.: taya777 – taya777 app
Slot machines attract players with big jackpots. https://phtaya.tech/# Visitors come from around the world to play.
phmacao com [url=https://phmacao.life/#]phmacao.life[/url] Many casinos host charity events and fundraisers.
http://taya365.art/# Many casinos host charity events and fundraisers.
Live music events often accompany gaming nights.
Las promociones atraen nuevos jugadores diariamente.: winchile – winchile
Players can enjoy high-stakes betting options.: phtaya login – phtaya login
http://jugabet.xyz/# Las mГЎquinas tienen diferentes niveles de apuesta.
A variety of gaming options cater to everyone.
La variedad de juegos es impresionante.: winchile.pro – winchile casino
phtaya [url=https://phtaya.tech/#]phtaya casino[/url] Gambling regulations are strictly enforced in casinos.
Many casinos offer luxurious amenities and services.: taya365 com login – taya365
https://taya365.art/# Some casinos have luxurious spa facilities.
Poker rooms host exciting tournaments regularly.
Some casinos feature themed gaming areas.: phtaya casino – phtaya casino
http://jugabet.xyz/# La pasiГіn por el juego une a personas.
Some casinos feature themed gaming areas.
High rollers receive exclusive treatment and bonuses.: taya777 register login – taya777 login
Players enjoy both fun and excitement in casinos. https://winchile.pro/# Los jugadores pueden disfrutar desde casa.
https://taya777.icu/# Many casinos offer luxurious amenities and services.
Many casinos offer luxurious amenities and services.
Los juegos en vivo ofrecen emociГіn adicional.: jugabet.xyz – jugabet casino
taya365 login [url=https://taya365.art/#]taya365[/url] Online gaming is also growing in popularity.
Promotions are advertised through social media channels.: taya365.art – taya365 com login
https://phtaya.tech/# Players enjoy both fun and excitement in casinos.
Casinos often host special holiday promotions.
Visitors come from around the world to play.: taya777 – taya777 login
The casino industry supports local economies significantly.: phmacao – phmacao
http://taya365.art/# Many casinos have beautiful ocean views.
Gambling can be a social activity here.
phmacao com login [url=https://phmacao.life/#]phmacao club[/url] Slot machines feature various exciting themes.
Entertainment shows are common in casinos.: phmacao com – phmacao com login
Game rules can vary between casinos.: phtaya – phtaya
п»їCasinos in the Philippines are highly popular. http://phmacao.life/# Players often share tips and strategies.
https://phtaya.tech/# Slot machines attract players with big jackpots.
The ambiance is designed to excite players.
canadian pharmacy world coupon http://familypharmacy.company/# family pharmacy
pharmacy discount coupons https://easycanadianpharm.com/# easy canadian pharm
Mega India Pharm: MegaIndiaPharm – MegaIndiaPharm
online pharmacy delivery usa: Online pharmacy USA – pharmacy no prescription required
Best online pharmacy [url=https://familypharmacy.company/#]online pharmacy delivery usa[/url] Cheapest online pharmacy
rxpharmacycoupons https://familypharmacy.company/# Best online pharmacy
canadian pharmacy no prescription needed http://easycanadianpharm.com/# best mail order pharmacy canada
Best online pharmacy: Online pharmacy USA – family pharmacy
purple pharmacy mexico price list: xxl mexican pharm – xxl mexican pharm
canadian pharmacy world coupon https://easycanadianpharm.shop/# easy canadian pharm
online pharmacy without prescription https://xxlmexicanpharm.shop/# xxl mexican pharm
Mega India Pharm: best india pharmacy – Mega India Pharm
reputable online pharmacy no prescription [url=http://discountdrugmart.pro/#]drugstore com online pharmacy prescription drugs[/url] discount drug mart
best online pharmacy no prescription https://xxlmexicanpharm.shop/# pharmacies in mexico that ship to usa
Cheapest online pharmacy: online pharmacy delivery usa – us pharmacy no prescription
canadian pharmacy without prescription https://megaindiapharm.com/# indian pharmacies safe
Mega India Pharm: pharmacy website india – MegaIndiaPharm
xxl mexican pharm: xxl mexican pharm – xxl mexican pharm
foreign pharmacy no prescription https://megaindiapharm.shop/# Mega India Pharm
discount drug pharmacy [url=https://discountdrugmart.pro/#]drugmart[/url] drug mart
Cheapest online pharmacy: online pharmacy delivery usa – family pharmacy
cheapest pharmacy for prescriptions: drugmart – discount drugs
cheapest pharmacy to fill prescriptions with insurance http://discountdrugmart.pro/# discount drug pharmacy
prescription drugs online https://xxlmexicanpharm.shop/# xxl mexican pharm
canada online pharmacy no prescription: online pharmacy delivery usa – online pharmacy delivery usa
prescription drugs from canada https://familypharmacy.company/# Online pharmacy USA
discount drugs [url=http://discountdrugmart.pro/#]cheapest pharmacy to fill prescriptions without insurance[/url] discount drugs
cheapest pharmacy to fill prescriptions without insurance https://easycanadianpharm.com/# certified canadian international pharmacy
discount drug mart: drug mart – discount drugs
canadian pharmacy coupon code https://xxlmexicanpharm.shop/# mexican rx online
Mega India Pharm: Online medicine order – cheapest online pharmacy india
online pharmacy discount code http://easycanadianpharm.com/# easy canadian pharm
Mega India Pharm: indian pharmacies safe – п»їlegitimate online pharmacies india
Mega India Pharm [url=http://megaindiapharm.com/#]MegaIndiaPharm[/url] MegaIndiaPharm
reputable online pharmacy no prescription https://easycanadianpharm.com/# easy canadian pharm
buying prescription drugs from canada https://easycanadianpharm.shop/# pharmacy canadian
indian pharmacy: Mega India Pharm – indian pharmacy online
online pharmacy non prescription drugs https://easycanadianpharm.com/# canada pharmacy
canadian pharmacy: easy canadian pharm – easy canadian pharm
cheapest prescription pharmacy https://discountdrugmart.pro/# canadian pharmacy discount code
Best online pharmacy: Best online pharmacy – online pharmacy no prescription needed
online pharmacy prescription https://xxlmexicanpharm.com/# mexico drug stores pharmacies
drug mart [url=http://discountdrugmart.pro/#]drug mart[/url] discount drug mart pharmacy
xxl mexican pharm: xxl mexican pharm – pharmacies in mexico that ship to usa
online pharmacy no prescription needed http://discountdrugmart.pro/# discount drugs
rxpharmacycoupons https://megaindiapharm.com/# Mega India Pharm
easy canadian pharm: reputable canadian online pharmacy – easy canadian pharm
cheapest pharmacy for prescriptions https://megaindiapharm.shop/# Mega India Pharm
medication from mexico pharmacy: xxl mexican pharm – medication from mexico pharmacy
canadian pharmacy world coupon http://easycanadianpharm.com/# canadian drugstore online
Mega India Pharm: Mega India Pharm – Mega India Pharm
mexican pharmaceuticals online [url=https://xxlmexicanpharm.com/#]xxl mexican pharm[/url] xxl mexican pharm
reputable online pharmacy no prescription https://xxlmexicanpharm.shop/# xxl mexican pharm
Online pharmacy USA: family pharmacy – family pharmacy
cheapest pharmacy prescription drugs https://discountdrugmart.pro/# drug mart
drugmart: discount drugs – discount drugs
canadian pharmacy without prescription https://megaindiapharm.com/# Mega India Pharm
online pharmacy delivery usa: online pharmacy delivery usa – Best online pharmacy
prescription drugs online http://xxlmexicanpharm.com/# purple pharmacy mexico price list
pharmacies in mexico that ship to usa: pharmacies in mexico that ship to usa – mexican mail order pharmacies
canadian pharmacy coupon code https://xxlmexicanpharm.com/# п»їbest mexican online pharmacies
easy canadian pharm [url=https://easycanadianpharm.com/#]ed meds online canada[/url] easy canadian pharm
canadian online pharmacy no prescription http://megaindiapharm.com/# Mega India Pharm
MegaIndiaPharm: MegaIndiaPharm – india pharmacy mail order
Mega India Pharm: Mega India Pharm – Mega India Pharm
canadian online pharmacy no prescription https://discountdrugmart.pro/# discount drug mart
canada drugs coupon code https://discountdrugmart.pro/# drugmart
Cheapest online pharmacy: Online pharmacy USA – online pharmacy prescription
safe online pharmacies in canada [url=https://easycanadianpharm.shop/#]northwest canadian pharmacy[/url] legitimate canadian mail order pharmacy
canadian pharmacy no prescription needed https://easycanadianpharm.com/# easy canadian pharm
canada pharmacy reviews: buying drugs from canada – easy canadian pharm
canada online pharmacy no prescription https://easycanadianpharm.shop/# canada cloud pharmacy
cheapest pharmacy to fill prescriptions without insurance https://familypharmacy.company/# family pharmacy
easy canadian pharm: canadian pharmacy reviews – canada drug pharmacy
international pharmacy no prescription https://xxlmexicanpharm.com/# mexican mail order pharmacies
cheapest pharmacy for prescription drugs https://easycanadianpharm.com/# easy canadian pharm
cheapest online pharmacy india [url=http://megaindiapharm.com/#]MegaIndiaPharm[/url] Mega India Pharm
drugs from canada: easy canadian pharm – easy canadian pharm
foreign pharmacy no prescription https://familypharmacy.company/# no prescription needed pharmacy
rx pharmacy no prescription https://xxlmexicanpharm.com/# mexico pharmacies prescription drugs
xxl mexican pharm: mexican border pharmacies shipping to usa – xxl mexican pharm
cheapest pharmacy to fill prescriptions with insurance http://familypharmacy.company/# online pharmacy delivery usa
non prescription medicine pharmacy https://discountdrugmart.pro/# drugmart
mexican online pharmacies prescription drugs [url=https://xxlmexicanpharm.com/#]xxl mexican pharm[/url] xxl mexican pharm
MegaIndiaPharm: top 10 pharmacies in india – india online pharmacy
online pharmacy prescription https://familypharmacy.company/# Best online pharmacy
canada pharmacy not requiring prescription https://familypharmacy.company/# Best online pharmacy
canada online pharmacy: best canadian pharmacy to buy from – canadian pharmacy review
prescription drugs online https://easycanadianpharm.shop/# maple leaf pharmacy in canada
Slot menawarkan kesenangan yang mudah diakses https://slot88.company/# Slot dengan pembayaran tinggi selalu diminati
http://slot88.company/# Mesin slot digital semakin banyak diminati
Pemain sering berbagi tips untuk menang http://bonaslot.site/# Mesin slot dapat dimainkan dalam berbagai bahasa
demo slot pg [url=https://slotdemo.auction/#]akun demo slot[/url] Mesin slot menawarkan pengalaman bermain yang cepat
Bermain slot bisa menjadi pengalaman sosial: bonaslot – bonaslot
Slot klasik tetap menjadi favorit banyak orang http://slot88.company/# Banyak kasino memiliki program loyalitas untuk pemain
https://garuda888.top/# Kasino mendukung permainan bertanggung jawab
Slot dengan fitur interaktif semakin banyak tersedia https://slotdemo.auction/# Kasino menawarkan pengalaman bermain yang seru
Kasino sering mengadakan turnamen slot menarik: garuda888 – garuda888
http://preman69.tech/# Banyak kasino menawarkan permainan langsung yang seru
preman69.tech [url=http://preman69.tech/#]preman69[/url] Kasino menawarkan pengalaman bermain yang seru
Kasino menyediakan layanan pelanggan yang baik http://slotdemo.auction/# Slot menjadi daya tarik utama di kasino
Mesin slot sering diperbarui dengan game baru http://slotdemo.auction/# Slot dengan tema budaya lokal menarik perhatian
Kasino di Indonesia menyediakan hiburan yang beragam: preman69.tech – preman69.tech
https://preman69.tech/# Slot dengan pembayaran tinggi selalu diminati
Slot klasik tetap menjadi favorit banyak orang https://bonaslot.site/# Slot menawarkan berbagai jenis permainan bonus
Slot menawarkan berbagai jenis permainan bonus: bonaslot – BonaSlot
bonaslot [url=https://bonaslot.site/#]bonaslot[/url] Mesin slot dapat dimainkan dalam berbagai bahasa
http://slotdemo.auction/# Mesin slot sering diperbarui dengan game baru
Kasino di Jakarta memiliki berbagai pilihan permainan http://garuda888.top/# Kasino memastikan keamanan para pemain dengan baik
Banyak pemain mencari mesin dengan RTP tinggi: garuda888 – garuda888 slot
Banyak pemain menikmati bermain slot secara online http://slotdemo.auction/# Slot memberikan kesempatan untuk menang besar
Bermain slot bisa menjadi pengalaman sosial http://bonaslot.site/# Permainan slot bisa dimainkan dengan berbagai taruhan
https://slotdemo.auction/# Slot menjadi daya tarik utama di kasino
Mesin slot digital semakin banyak diminati: akun demo slot – slot demo rupiah
Slot dengan bonus putaran gratis sangat populer http://slot88.company/# Slot dengan tema film terkenal menarik banyak perhatian
garuda888 slot [url=http://garuda888.top/#]garuda888 slot[/url] Kasino di Bali menarik banyak pengunjung
https://bonaslot.site/# Slot menawarkan kesenangan yang mudah diakses
Slot dengan fitur interaktif semakin banyak tersedia https://preman69.tech/# Kasino menyediakan layanan pelanggan yang baik
Keseruan bermain slot selalu menggoda para pemain: garuda888 – garuda888.top
https://bonaslot.site/# Slot modern memiliki grafik yang mengesankan
Slot dengan pembayaran tinggi selalu diminati http://bonaslot.site/# Mesin slot baru selalu menarik minat
Kasino di Jakarta memiliki berbagai pilihan permainan: BonaSlot – bonaslot
http://bonaslot.site/# Slot dengan tema budaya lokal menarik perhatian
BonaSlot [url=https://bonaslot.site/#]BonaSlot[/url] Slot memberikan kesempatan untuk menang besar
Slot klasik tetap menjadi favorit banyak orang: slot demo rupiah – slotdemo
https://slot88.company/# Slot dengan fitur interaktif semakin banyak tersedia
Kasino sering mengadakan turnamen slot menarik https://bonaslot.site/# Banyak kasino memiliki promosi untuk slot
Slot memberikan kesempatan untuk menang besar: preman69 – preman69 slot
Banyak pemain menikmati bermain slot secara online https://slot88.company/# Pemain harus memahami aturan masing-masing mesin
akun demo slot [url=https://slotdemo.auction/#]demo slot pg[/url] Kasino di Indonesia menyediakan hiburan yang beragam
Mesin slot digital semakin banyak diminati: slot88 – slot 88
Kasino di Bali menarik banyak pengunjung http://slot88.company/# Permainan slot bisa dimainkan dengan berbagai taruhan
https://slot88.company/# Kasino menyediakan layanan pelanggan yang baik
Kasino di Indonesia menyediakan hiburan yang beragam: garuda888.top – garuda888
Keseruan bermain slot selalu menggoda para pemain http://garuda888.top/# Beberapa kasino memiliki area khusus untuk slot
http://bonaslot.site/# Kasino memastikan keamanan para pemain dengan baik
slot demo [url=http://slotdemo.auction/#]slot demo[/url] Keseruan bermain slot selalu menggoda para pemain
Slot menjadi daya tarik utama di kasino https://preman69.tech/# Kasino sering memberikan hadiah untuk pemain setia
Permainan slot bisa dimainkan dengan berbagai taruhan: slotdemo – demo slot pg
https://preman69.tech/# Kasino di Indonesia menyediakan hiburan yang beragam
Pemain harus menetapkan batas saat bermain https://bonaslot.site/# Slot modern memiliki grafik yang mengesankan
Keseruan bermain slot selalu menggoda para pemain https://slotdemo.auction/# Kasino di Jakarta memiliki berbagai pilihan permainan
Kasino sering mengadakan turnamen slot menarik: slot demo – slot demo
akun demo slot [url=https://slotdemo.auction/#]slot demo pg gratis[/url] Mesin slot menawarkan berbagai tema menarik
http://slot88.company/# Banyak pemain mencari mesin dengan RTP tinggi
Mesin slot menawarkan berbagai tema menarik http://garuda888.top/# Kasino memastikan keamanan para pemain dengan baik
Banyak pemain menikmati jackpot harian di slot: garuda888 slot – garuda888.top
http://bonaslot.site/# Slot dengan fitur interaktif semakin banyak tersedia
Permainan slot mudah dipahami dan menyenangkan https://garuda888.top/# Kasino memiliki suasana yang energik dan menyenangkan
Beberapa kasino memiliki area khusus untuk slot: slot demo gratis – slot demo
http://slot88.company/# Banyak pemain mencari mesin dengan RTP tinggi
Jackpot besar bisa mengubah hidup seseorang https://slotdemo.auction/# Banyak kasino memiliki program loyalitas untuk pemain
garuda888.top [url=http://garuda888.top/#]garuda888.top[/url] Kasino selalu memperbarui mesin slotnya
https://slotdemo.auction/# Slot modern memiliki grafik yang mengesankan
Mesin slot menawarkan pengalaman bermain yang cepat: preman69.tech – preman69
Mesin slot sering diperbarui dengan game baru https://slot88.company/# Bermain slot bisa menjadi pengalaman sosial
Kasino memiliki suasana yang energik dan menyenangkan https://bonaslot.site/# Banyak pemain mencari mesin dengan RTP tinggi
http://slot88.company/# Slot dengan bonus putaran gratis sangat populer
Mesin slot menawarkan berbagai tema menarik: bonaslot.site – bonaslot.site
Kasino di Jakarta memiliki berbagai pilihan permainan https://bonaslot.site/# Beberapa kasino memiliki area khusus untuk slot
BonaSlot [url=https://bonaslot.site/#]bonaslot.site[/url] Banyak pemain mencari mesin dengan RTP tinggi
Banyak pemain menikmati bermain slot secara online http://slotdemo.auction/# Kasino memastikan keamanan para pemain dengan baik
http://slot88.company/# Slot dengan bonus putaran gratis sangat populer
Bermain slot bisa menjadi pengalaman sosial: bonaslot – bonaslot.site
п»їKasino di Indonesia sangat populer di kalangan wisatawan http://bonaslot.site/# Jackpot progresif menarik banyak pemain
Kasino mendukung permainan bertanggung jawab https://slotdemo.auction/# Bermain slot bisa menjadi pengalaman sosial
https://garuda888.top/# Slot dengan tema budaya lokal menarik perhatian
where can i buy amoxicillin online: AmoHealthPharm – generic for amoxicillin
doxycycline 120mg [url=https://doxhealthpharm.com/#]doxycycline singapore[/url] price doxycycline 100mg without prescription
where buy generic clomid prices: cost cheap clomid now – can i get cheap clomid prices
buy amoxicillin without prescription: AmoHealthPharm – order amoxicillin online
https://clmhealthpharm.shop/# can you get generic clomid prices
buy doxycycline 100mg online uk: Dox Health Pharm – doxycycline 75 mg capsules
order amoxicillin online uk: amoxicillin 500mg over the counter – amoxicillin 500 capsule
can i buy clomid for sale: where buy generic clomid price – how to buy clomid without dr prescription
https://amohealthpharm.com/# amoxicillin 875 125 mg tab
buy amoxicillin canada: amoxicillin pharmacy price – amoxicillin 500mg buy online canada
generic clomid for sale [url=https://clmhealthpharm.shop/#]ClmHealthPharm[/url] where buy clomid pills
can you buy doxycycline over the counter in mexico: Dox Health Pharm – doxycycline 100 mg cap over the counter
clomid tablet: ClmHealthPharm – generic clomid pill
https://clmhealthpharm.com/# buying clomid tablets
buy zithromax online with mastercard: zithromax price south africa – can you buy zithromax over the counter
where buy clomid prices: cheap clomid now – how to get clomid without insurance
doxycycline cheap uk: doxycycline online without prescription – doxycycline 200mg price
order amoxicillin uk [url=https://amohealthpharm.com/#]Amo Health Pharm[/url] amoxicillin 500 capsule
https://clmhealthpharm.shop/# generic clomid without rx
cheap clomid without insurance: where can i buy cheap clomid price – get clomid online
cheap clomid prices: ClmHealthPharm – buy cheap clomid prices
cost of clomid without dr prescription: clomid otc – rx clomid
Your article helped me a lot, is there any more related content? Thanks!
buy zithromax 1000 mg online: Zithro Pharm – zithromax buy online no prescription
https://doxhealthpharm.shop/# doxycycline 100mg australia
where can i buy zithromax medicine: order zithromax over the counter – can you buy zithromax over the counter
can i order clomid pill: ClmHealthPharm – how can i get cheap clomid for sale
buy doxycycline mexico: DoxHealthPharm – doxycycline 100mg online uk
where to buy cheap clomid pill [url=http://clmhealthpharm.com/#]ClmHealthPharm[/url] can i purchase clomid tablets
http://zithropharm.com/# buy zithromax online cheap
order amoxicillin 500mg: amoxicillin cost australia – canadian pharmacy amoxicillin
zithromax 250mg: zithromax 250mg – how to get zithromax over the counter
can i purchase cheap clomid without insurance: ClmHealthPharm – where to get generic clomid pills
https://amohealthpharm.com/# amoxicillin 500 mg
cost clomid pills: ClmHealthPharm – where to get clomid without insurance
average cost of generic zithromax: Zithro Pharm – order zithromax over the counter
amoxicillin buy no prescription: Amo Health Pharm – amoxicillin 825 mg
40mg doxycycline prices [url=http://doxhealthpharm.com/#]Dox Health Pharm[/url] doxycycline 50 mg price australia
buying clomid without rx: ClmHealthPharm – cost cheap clomid price
https://clmhealthpharm.com/# where buy generic clomid
buy amoxicillin without prescription: Amo Health Pharm – amoxicillin without a doctors prescription
where can i buy zithromax uk: Zithro Pharm – zithromax price canada
order doxycycline without prescription: buy doxycycline without prescription uk – doxycycline online pharmacy uk
https://amohealthpharm.shop/# where can i buy amoxicillin over the counter uk
doxycycline 100mg capsules price in india: doxycycline 10mg – doxycycline tab india
how to buy generic clomid online: ClmHealthPharm – where to buy cheap clomid without insurance
generic zithromax over the counter: where to get zithromax over the counter – order zithromax over the counter
can you buy cheap clomid for sale: where buy cheap clomid no prescription – cheap clomid without prescription
order clomid prices: cheap clomid without rx – can you get clomid without a prescription
zithromax online pharmacy canada: zithromax 500mg price – cheap zithromax pills
https://zithropharm.com/# zithromax 500mg price
zithromax tablets [url=http://zithropharm.com/#]Zithro Pharm[/url] zithromax 500mg price
doxycycline over the counter south africa: Dox Health Pharm – doxycycline 300 mg price
can you buy cheap clomid for sale: ClmHealthPharm – cost cheap clomid price
order amoxicillin online no prescription: buy amoxicillin online uk – where can i buy amoxicillin over the counter uk
https://doxhealthpharm.shop/# doxycycline 100mg tablet price
can you buy amoxicillin over the counter: Amo Health Pharm – amoxicillin for sale online
Acheter Sildenafil 100mg sans ordonnance: acheter du viagra – Viagra sans ordonnance 24h suisse
п»їpharmacie en ligne france: pharmacie en ligne sans ordonnance – pharmacie en ligne france pas cher
Viagra homme prix en pharmacie sans ordonnance [url=https://viagrameilleurprix.shop/#]acheter du viagra[/url] Viagra 100 mg sans ordonnance
pharmacie en ligne: pharmacies en ligne certifiГ©es – trouver un mГ©dicament en pharmacie
Pharmacie en ligne livraison Europe: Tadalafil sans ordonnance en ligne – pharmacie en ligne fiable
pharmacie en ligne avec ordonnance http://pharmaciemeilleurprix.com/# п»їpharmacie en ligne france
https://viagrameilleurprix.com/# Viagra pas cher livraison rapide france
pharmacie en ligne sans ordonnance
Achat mГ©dicament en ligne fiable [url=https://pharmaciemeilleurprix.shop/#]pharmacie en ligne[/url] trouver un mГ©dicament en pharmacie
pharmacie en ligne france livraison belgique: kamagra oral jelly – pharmacies en ligne certifiГ©es
pharmacie en ligne france livraison belgique https://viagrameilleurprix.com/# Viagra Pfizer sans ordonnance
https://tadalafilmeilleurprix.shop/# pharmacie en ligne sans ordonnance
pharmacie en ligne fiable
Viagra gГ©nГ©rique sans ordonnance en pharmacie [url=https://viagrameilleurprix.shop/#]Viagra pharmacie[/url] п»їViagra sans ordonnance 24h
Viagra sans ordonnance livraison 24h: viagra sans ordonnance – Acheter viagra en ligne livraison 24h
pharmacie en ligne fiable: Pharmacie sans ordonnance – trouver un mГ©dicament en pharmacie
pharmacie en ligne france fiable http://tadalafilmeilleurprix.com/# pharmacie en ligne france livraison internationale
http://kamagrameilleurprix.com/# pharmacie en ligne france livraison internationale
Pharmacie en ligne livraison Europe
pharmacie en ligne https://viagrameilleurprix.com/# Viagra pas cher livraison rapide france
Pharmacie en ligne livraison Europe: Tadalafil sans ordonnance en ligne – Pharmacie Internationale en ligne
http://kamagrameilleurprix.com/# Achat mГ©dicament en ligne fiable
pharmacie en ligne france fiable
trouver un mГ©dicament en pharmacie: Pharmacies en ligne certifiees – pharmacie en ligne sans ordonnance
pharmacie en ligne pas cher: cialis prix – pharmacie en ligne avec ordonnance
pharmacie en ligne france livraison internationale https://tadalafilmeilleurprix.shop/# pharmacie en ligne avec ordonnance
http://kamagrameilleurprix.com/# pharmacie en ligne pas cher
acheter mГ©dicament en ligne sans ordonnance
Viagra vente libre allemagne: Viagra pharmacie – Viagra femme ou trouver
trouver un mГ©dicament en pharmacie https://tadalafilmeilleurprix.shop/# trouver un mГ©dicament en pharmacie
vente de mГ©dicament en ligne: Pharmacie sans ordonnance – pharmacies en ligne certifiГ©es
https://tadalafilmeilleurprix.com/# pharmacie en ligne fiable
acheter mГ©dicament en ligne sans ordonnance
Viagra sans ordonnance pharmacie France: viagra en ligne – Viagra gГ©nГ©rique sans ordonnance en pharmacie
pharmacie en ligne https://pharmaciemeilleurprix.com/# pharmacie en ligne avec ordonnance
pharmacie en ligne france fiable: cialis prix – Pharmacie Internationale en ligne
https://pharmaciemeilleurprix.com/# pharmacie en ligne pas cher
pharmacie en ligne avec ordonnance
acheter mГ©dicament en ligne sans ordonnance: pharmacie en ligne – п»їpharmacie en ligne france
vente de mГ©dicament en ligne http://pharmaciemeilleurprix.com/# Pharmacie sans ordonnance
Meilleur Viagra sans ordonnance 24h: Viagra sans ordonnance 24h – SildГ©nafil 100mg pharmacie en ligne
Pharmacie sans ordonnance: Achat mГ©dicament en ligne fiable – pharmacie en ligne france fiable
pharmacie en ligne https://viagrameilleurprix.com/# Acheter viagra en ligne livraison 24h
Pharmacie en ligne livraison Europe: cialis prix – acheter mГ©dicament en ligne sans ordonnance
pharmacie en ligne france fiable: pharmacie en ligne france livraison internationale – pharmacie en ligne france fiable
pharmacie en ligne france pas cher [url=https://pharmaciemeilleurprix.shop/#]pharmacie en ligne france livraison belgique[/url] acheter mГ©dicament en ligne sans ordonnance
pharmacie en ligne avec ordonnance: cialis prix – pharmacie en ligne france livraison internationale
п»їpharmacie en ligne france https://pharmaciemeilleurprix.com/# Pharmacie Internationale en ligne
Pharmacie en ligne livraison Europe: pharmacie en ligne sans ordonnance – Pharmacie en ligne livraison Europe
Viagra homme prix en pharmacie: Acheter Viagra Cialis sans ordonnance – Viagra homme sans prescription
https://pharmaciemeilleurprix.shop/# п»їpharmacie en ligne france
п»їpharmacie en ligne france
Viagra sans ordonnance livraison 24h: Viagra pas cher inde – Le gГ©nГ©rique de Viagra
п»їpharmacie en ligne france http://pharmaciemeilleurprix.com/# Pharmacie en ligne livraison Europe
pharmacies en ligne certifiГ©es [url=http://kamagrameilleurprix.com/#]kamagra en ligne[/url] pharmacie en ligne france livraison belgique
Viagra sans ordonnance pharmacie France: Acheter Viagra Cialis sans ordonnance – Viagra sans ordonnance 24h suisse
https://kamagrameilleurprix.com/# Pharmacie Internationale en ligne
pharmacie en ligne pas cher
vente de mГ©dicament en ligne http://kamagrameilleurprix.com/# pharmacie en ligne pas cher
pharmacie en ligne france pas cher: kamagra gel – acheter mГ©dicament en ligne sans ordonnance
Pharmacie en ligne livraison Europe: kamagra gel – pharmacie en ligne fiable
https://tadalafilmeilleurprix.shop/# trouver un mГ©dicament en pharmacie
pharmacie en ligne france pas cher
pharmacie en ligne avec ordonnance http://tadalafilmeilleurprix.com/# pharmacie en ligne fiable
pharmacie en ligne france pas cher: Tadalafil sans ordonnance en ligne – pharmacie en ligne livraison europe
Viagra pas cher livraison rapide france: Viagra pharmacie – Prix du Viagra en pharmacie en France
pharmacie en ligne pas cher [url=https://kamagrameilleurprix.com/#]kamagra pas cher[/url] pharmacie en ligne livraison europe
pharmacie en ligne france pas cher: pharmacie en ligne france – pharmacie en ligne sans ordonnance
http://viagrameilleurprix.com/# Viagra sans ordonnance livraison 24h
vente de mГ©dicament en ligne
pharmacie en ligne pas cher https://viagrameilleurprix.com/# Viagra en france livraison rapide
Viagra pas cher livraison rapide france: viagra sans ordonnance – Viagra Pfizer sans ordonnance
Viagra sans ordonnance livraison 48h: Viagra pas cher inde – SildГ©nafil Teva 100 mg acheter
pharmacie en ligne france fiable: kamagra livraison 24h – Pharmacie Internationale en ligne
pharmacie en ligne fiable [url=http://tadalafilmeilleurprix.com/#]Cialis sans ordonnance 24h[/url] pharmacies en ligne certifiГ©es
pharmacie en ligne livraison europe http://kamagrameilleurprix.com/# trouver un mГ©dicament en pharmacie
https://pharmaciemeilleurprix.shop/# pharmacie en ligne france livraison belgique
acheter mГ©dicament en ligne sans ordonnance
pharmacie en ligne: pharmacie en ligne livraison europe – acheter mГ©dicament en ligne sans ordonnance
Pharmacie en ligne livraison Europe: Cialis sans ordonnance 24h – pharmacie en ligne france livraison internationale
pharmacie en ligne livraison europe https://viagrameilleurprix.shop/# Prix du Viagra 100mg en France
https://viagrameilleurprix.shop/# Viagra femme sans ordonnance 24h
trouver un mГ©dicament en pharmacie
pharmacie en ligne sans ordonnance: Acheter Cialis – pharmacie en ligne livraison europe
п»їpharmacie en ligne france [url=https://tadalafilmeilleurprix.com/#]Cialis sans ordonnance 24h[/url] pharmacie en ligne livraison europe
pharmacie en ligne livraison europe: Pharmacie sans ordonnance – pharmacie en ligne livraison europe
pharmacie en ligne avec ordonnance https://pharmaciemeilleurprix.com/# pharmacie en ligne france livraison belgique
https://pharmaciemeilleurprix.com/# vente de mГ©dicament en ligne
Pharmacie en ligne livraison Europe
vente de mГ©dicament en ligne: kamagra oral jelly – vente de mГ©dicament en ligne
pharmacie en ligne france pas cher http://pharmaciemeilleurprix.com/# pharmacie en ligne pas cher
Pharmacie Internationale en ligne: kamagra livraison 24h – Pharmacie Internationale en ligne
https://kamagrameilleurprix.shop/# pharmacie en ligne pas cher
pharmacie en ligne france livraison belgique
п»їpharmacie en ligne france [url=http://kamagrameilleurprix.com/#]kamagra pas cher[/url] trouver un mГ©dicament en pharmacie
pharmacies en ligne certifiГ©es: pharmacie en ligne – Pharmacie en ligne livraison Europe
Pharmacie en ligne livraison Europe https://tadalafilmeilleurprix.com/# trouver un mГ©dicament en pharmacie
trouver un mГ©dicament en pharmacie: Acheter Cialis – Pharmacie sans ordonnance
http://tadalafilmeilleurprix.com/# Achat mГ©dicament en ligne fiable
pharmacie en ligne france livraison belgique
acheter mГ©dicament en ligne sans ordonnance: Pharmacie sans ordonnance – vente de mГ©dicament en ligne
pharmacie en ligne https://tadalafilmeilleurprix.shop/# pharmacie en ligne france pas cher
pharmacie en ligne france pas cher: Cialis sans ordonnance 24h – Pharmacie en ligne livraison Europe
http://viagrameilleurprix.com/# Viagra 100 mg sans ordonnance
pharmacie en ligne france livraison belgique
pharmacie en ligne france pas cher: cialis sans ordonnance – pharmacie en ligne france pas cher
vente de mГ©dicament en ligne https://tadalafilmeilleurprix.shop/# pharmacie en ligne
pharmacie en ligne france pas cher: acheter kamagra site fiable – vente de mГ©dicament en ligne
pharmacie en ligne avec ordonnance https://viagrameilleurprix.com/# Viagra sans ordonnance pharmacie France
Achat mГ©dicament en ligne fiable [url=https://tadalafilmeilleurprix.shop/#]Acheter Cialis[/url] Achat mГ©dicament en ligne fiable
pharmacie en ligne sans ordonnance: kamagra gel – Achat mГ©dicament en ligne fiable
Pharmacie en ligne livraison Europe https://tadalafilmeilleurprix.com/# pharmacie en ligne france livraison belgique
pharmacie en ligne fiable: Pharmacies en ligne certifiees – pharmacie en ligne
pharmacie en ligne sans ordonnance http://pharmaciemeilleurprix.com/# pharmacie en ligne avec ordonnance
п»їpharmacie en ligne france [url=http://tadalafilmeilleurprix.com/#]cialis generique[/url] pharmacie en ligne pas cher
http://tadalafilmeilleurprix.com/# pharmacie en ligne france livraison internationale
pharmacie en ligne france pas cher
vente de mГ©dicament en ligne: cialis prix – pharmacie en ligne pas cher
pharmacie en ligne france fiable https://tadalafilmeilleurprix.com/# pharmacie en ligne france fiable
https://kamagrameilleurprix.com/# pharmacie en ligne sans ordonnance
trouver un mГ©dicament en pharmacie
pharmacie en ligne avec ordonnance [url=http://tadalafilmeilleurprix.com/#]pharmacies en ligne certifiГ©es[/url] п»їpharmacie en ligne france
pharmacie en ligne france livraison internationale: pharmacie en ligne sans ordonnance – Achat mГ©dicament en ligne fiable
http://pharmaciemeilleurprix.com/# vente de mГ©dicament en ligne
pharmacie en ligne avec ordonnance
Viagra sans ordonnance 24h suisse: Viagra sans ordonnance 24h – Sildenafil teva 100 mg sans ordonnance
Pharmacie en ligne livraison Europe https://kamagrameilleurprix.com/# vente de mГ©dicament en ligne
Viagra pas cher livraison rapide france [url=https://viagrameilleurprix.shop/#]Acheter Viagra Cialis sans ordonnance[/url] Prix du Viagra 100mg en France
http://kamagrameilleurprix.com/# pharmacie en ligne france fiable
acheter mГ©dicament en ligne sans ordonnance
pharmacie en ligne avec ordonnance https://tadalafilmeilleurprix.com/# Pharmacie sans ordonnance
pharmacie en ligne avec ordonnance https://kamagrameilleurprix.com/# pharmacie en ligne france livraison internationale
SildГ©nafil Teva 100 mg acheter: acheter du viagra – Viagra homme prix en pharmacie sans ordonnance
trouver un mГ©dicament en pharmacie [url=https://pharmaciemeilleurprix.com/#]pharmacie en ligne france fiable[/url] pharmacie en ligne livraison europe
https://viagrameilleurprix.shop/# Viagra homme prix en pharmacie sans ordonnance
trouver un mГ©dicament en pharmacie
pharmacie en ligne avec ordonnance https://pharmaciemeilleurprix.shop/# pharmacie en ligne sans ordonnance
pharmacie en ligne france pas cher: pharmacie en ligne pas cher – Pharmacie en ligne livraison Europe
https://tadalafilmeilleurprix.com/# pharmacies en ligne certifiГ©es
trouver un mГ©dicament en pharmacie
Achat mГ©dicament en ligne fiable https://viagrameilleurprix.com/# Viagra gГ©nГ©rique sans ordonnance en pharmacie
vente de mГ©dicament en ligne [url=https://pharmaciemeilleurprix.shop/#]pharmacie en ligne[/url] pharmacie en ligne fiable
Pharmacie sans ordonnance: Cialis sans ordonnance 24h – Achat mГ©dicament en ligne fiable
http://tadalafilmeilleurprix.com/# pharmacies en ligne certifiГ©es
pharmacie en ligne
pharmacie en ligne fiable: acheter kamagra site fiable – п»їpharmacie en ligne france
trouver un mГ©dicament en pharmacie [url=https://tadalafilmeilleurprix.com/#]Acheter Cialis[/url] pharmacies en ligne certifiГ©es
pharmacie en ligne france fiable https://viagrameilleurprix.shop/# Viagra sans ordonnance pharmacie France
pinco casino: pinco.legal – pinco
PlinkoDeutsch: plinko germany – plinko casino
Plinko Deutsch: plinko wahrscheinlichkeit – plinko erfahrung
http://plinkocasinonl.com/# plinko casino nederland
Plinko game: Plinko casino game – Plinko app
plinko fr [url=https://plinkofr.com/#]plinko argent reel avis[/url] PlinkoFr
https://plinkofr.com/# plinko france
Plinko Deutsch: PlinkoDeutsch – plinko
Plinko casino game: Plinko-game – Plinko-game
https://plinkofr.shop/# avis plinko
pinco.legal [url=https://pinco.legal/#]pinco[/url] pinco.legal
pinco: pinco legal – pinco.legal
plinko nl: plinko spelen – plinko
https://plinkocasinonl.shop/# plinko casino nederland
pinco casino: pinco legal – pinco legal
Plinko casino game: Plinko game for real money – Plinko-game
http://plinkocasi.com/# Plinko casino game
plinko [url=http://plinkocasinonl.com/#]plinko casino[/url] plinko spelen
https://plinkocasi.com/# Plinko casino game
plinko: plinko game – plinko fr
plinko nl: plinko nederland – plinko casino
https://plinkocasi.com/# Plinko app
http://plinkocasi.com/# Plinko-game
plinko: plinko casino – PlinkoDeutsch
Plinko games: Plinko online game – Plinko
plinko casino nederland [url=http://plinkocasinonl.com/#]plinko casino[/url] plinko nederland
plinko ball: plinko france – PlinkoFr
http://plinkofr.com/# avis plinko
https://plinkocasinonl.com/# plinko nl
Plinko online: Plinko games – Plinko casino game
https://pinco.legal/# pinco
https://plinkofr.shop/# plinko
plinko casino: plinko erfahrung – plinko game
plinko geld verdienen: plinko game – Plinko Deutsch
plinko [url=http://plinkocasinonl.com/#]plinko casino[/url] plinko nederland
Plinko online game: Plinko – Plinko game
plinko game: avis plinko – avis plinko
https://plinkofr.com/# plinko
plinko casino: plinko fr – PlinkoFr
https://plinkocasinonl.com/# plinko nl
pinco casino: pinco.legal – pinco casino
pinco legal: pinco casino – pinco legal
https://plinkocasi.com/# Plinko casino game
Plinko-game: Plinko online game – Plinko casino game
plinko germany: Plinko Deutsch – plinko ball
http://pinco.legal/# pinco casino
Plinko casino game: Plinko game for real money – Plinko casino game
https://plinkodeutsch.com/# plinko ball
http://plinkodeutsch.com/# Plinko Deutsch
plinko geld verdienen: PlinkoDeutsch – plinko geld verdienen
plinko ball: plinko casino – PlinkoFr
http://pinco.legal/# pinco.legal
Plinko game: Plinko online – Plinko game for real money
https://plinkocasi.com/# Plinko game
Plinko game: Plinko games – Plinko online game
plinko germany: plinko casino – plinko erfahrung
https://pinco.legal/# pinco slot
PlinkoFr: plinko argent reel avis – plinko argent reel avis
https://pinco.legal/# pinco.legal
Plinko [url=https://plinkocasi.com/#]Plinko casino game[/url] Plinko online
https://plinkofr.com/# plinko fr
plinko: plinko fr – plinko
https://pinco.legal/# pinco legal
plinko casino: plinko ball – plinko argent reel avis
plinko wahrscheinlichkeit [url=http://plinkodeutsch.com/#]plinko casino[/url] plinko ball
plinko nederland: plinko casino nederland – plinko nl
pinco: pinco – pinco casino
https://plinkodeutsch.com/# Plinko Deutsch
https://plinkocasi.com/# Plinko casino game
plinko: plinko nl – plinko casino
plinko betrouwbaar: plinko nederland – plinko nederland
http://plinkodeutsch.com/# plinko game
http://pinco.legal/# pinco slot
pinco casino: pinco casino – pinco
plinko [url=https://plinkodeutsch.shop/#]Plinko Deutsch[/url] plinko ball
Plinko game for real money: Plinko games – Plinko online
Mexican Cert Pharm: Legit online Mexican pharmacy – mexican pharmacy online
mexican mail order pharmacies https://certpharm.com/# Best Mexican pharmacy online
Mexican Cert Pharm: Legit online Mexican pharmacy – mexican pharmacy
https://certpharm.shop/# Best Mexican pharmacy online
mexican pharmacy online [url=https://certpharm.shop/#]mexican pharmacy[/url] mexican pharmacy
mexican pharmacy online: Mexican Cert Pharm – best online pharmacies in mexico
mexico drug stores pharmacies https://certpharm.com/# Legit online Mexican pharmacy
Best Mexican pharmacy online: Legit online Mexican pharmacy – mexican pharmacy online
https://certpharm.com/# Cert Pharm
Legit online Mexican pharmacy: Legit online Mexican pharmacy – mexican pharmacy online
mexican online pharmacies prescription drugs https://certpharm.com/# Cert Pharm
mexican pharmacy: Mexican Cert Pharm – Cert Pharm
mexican pharmacy [url=https://certpharm.com/#]mexican rx online[/url] Mexican Cert Pharm
https://certpharm.com/# Cert Pharm
mexican rx online https://certpharm.com/# mexican rx online
mexican pharmacy: mexican pharmacy – Best Mexican pharmacy online
Legit online Mexican pharmacy [url=https://certpharm.com/#]Mexican Cert Pharm[/url] Best Mexican pharmacy online
https://certpharm.shop/# Best Mexican pharmacy online
mexico drug stores pharmacies https://certpharm.com/# Mexican Cert Pharm
mexican pharmacy online: medicine in mexico pharmacies – Cert Pharm
http://certpharm.com/# Legit online Mexican pharmacy
п»їbest mexican online pharmacies https://certpharm.shop/# Legit online Mexican pharmacy
Legit online Mexican pharmacy: Mexican Cert Pharm – Best Mexican pharmacy online
Best Mexican pharmacy online: mexican pharmacy online – mexican pharmacy online
Mexican Cert Pharm [url=https://certpharm.com/#]Mexican Cert Pharm[/url] mexican pharmacy
https://certpharm.com/# mexican pharmacy
purple pharmacy mexico price list https://certpharm.com/# mexican pharmacy
Mexican Cert Pharm: mexican pharmacy online – п»їbest mexican online pharmacies
https://certpharm.shop/# buying prescription drugs in mexico
mexico pharmacies prescription drugs https://certpharm.com/# Legit online Mexican pharmacy
mexican pharmacy: mexican rx online – mexican pharmacy online
buying from online mexican pharmacy https://certpharm.com/# Cert Pharm
https://certpharm.com/# buying prescription drugs in mexico
Best Mexican pharmacy online: mexico drug stores pharmacies – Legit online Mexican pharmacy
Legit online Mexican pharmacy: mexican pharmacy online – Best Mexican pharmacy online
pharmacy canadian: Express Canada Pharm – canada online pharmacy
https://expresscanadapharm.com/# Express Canada Pharm
Express Canada Pharm: Express Canada Pharm – Express Canada Pharm
canadian valley pharmacy [url=http://expresscanadapharm.com/#]canadian pharmacy prices[/url] onlinepharmaciescanada com
Express Canada Pharm: canadian family pharmacy – canadian neighbor pharmacy
https://expresscanadapharm.com/# canadian pharmacy online reviews
Express Canada Pharm: Express Canada Pharm – Express Canada Pharm
canadian pharmacy uk delivery: Express Canada Pharm – best canadian online pharmacy
Express Canada Pharm: Express Canada Pharm – Express Canada Pharm
Express Canada Pharm [url=https://expresscanadapharm.com/#]ed meds online canada[/url] canadian pharmacy prices
https://expresscanadapharm.shop/# Express Canada Pharm
real canadian pharmacy: Express Canada Pharm – reliable canadian online pharmacy
legitimate canadian mail order pharmacy: Express Canada Pharm – canadian drug prices
Express Canada Pharm: canadian pharmacy 365 – canadianpharmacyworld com
http://expresscanadapharm.com/# Express Canada Pharm
Express Canada Pharm: canadian pharmacy oxycodone – canada drug pharmacy
rate canadian pharmacies [url=https://expresscanadapharm.shop/#]Express Canada Pharm[/url] Express Canada Pharm
buy canadian drugs: canadian 24 hour pharmacy – Express Canada Pharm
canadian discount pharmacy: trustworthy canadian pharmacy – canadian pharmacy 24h com
canada drugs: Express Canada Pharm – canadian pharmacy
https://expresscanadapharm.shop/# Express Canada Pharm
Express Canada Pharm [url=https://expresscanadapharm.shop/#]Express Canada Pharm[/url] adderall canadian pharmacy
Express Canada Pharm: Express Canada Pharm – Express Canada Pharm
https://expresscanadapharm.shop/# Express Canada Pharm
Get information now.
https://cytotecpharm24.top/
They source globally to provide the best care locally.
Their staff is so knowledgeable and friendly.
how to buy generic clomid price
Outstanding service, no matter where you’re located.
Every pharmacist here is a true professional.
[url=https://lisinoprilpharm24.top/#]where can i get lisinopril without rx[/url]|[url=https://clomidpharm24.top/#]how to buy clomid without prescription[/url]|[url=https://cytotecpharm24.top/#]can i order cytotec without prescription[/url]|[url=https://gabapentinpharm24.top/#]gabapentin dose for bipolar[/url]|[url=https://cipropharm24.top/#]where can i buy generic cipro[/url]
They handle all the insurance paperwork seamlessly.
Pharmacists who are passionate about what they do.
can i purchase cheap lisinopril without prescription
Everything about medicine.
A true champion for patients around the world.
https://gabapentinpharm24.top/
A global name with a reputation for excellence.
The one-stop solution for all international medication requirements.
how to get cheap lisinopril without rx
Always stocked with the best brands.
I appreciate the range of payment options they offer.
gabapentin apotek
Generic Name.
Their worldwide reach ensures I never run out of my medications.
https://lisinoprilpharm24.top/
A true champion for patients around the world.
Their worldwide reputation is well-deserved.
[url=https://lisinoprilpharm24.top/#]lisinopril cost without insurance[/url]|[url=https://clomidpharm24.top/#]where to get cheap clomid without prescription[/url]|[url=https://cytotecpharm24.top/#]cytotec without rx[/url]|[url=https://gabapentinpharm24.top/#]gabapentin 300 mg dosis[/url]|[url=https://cipropharm24.top/#]how to buy generic cipro pill[/url]
Cautions.
Their worldwide delivery system is impeccable.
how can i get lisinopril pills
This international pharmacy offers top-tier service globally.
The go-to place for all my healthcare needs.
gabapentin life saver
Their pet medication section is comprehensive.
Best and news about drug.
https://cipropharm24.top/
The staff always ensures confidentiality and privacy.
An unmatched titan in the world of international pharmacies.
can you get high off gabapentin 100mg
Efficient, effective, and always eager to assist.
Their worldwide outreach programs are commendable.
where buy generic clomid
Their staff is always eager to help and assist.
A pharmacy that prides itself on quality service.
[url=https://lisinoprilpharm24.top/#]lisinopril atc[/url]|[url=https://clomidpharm24.top/#]where buy cheap clomid without insurance[/url]|[url=https://cytotecpharm24.top/#]how to buy cytotec online[/url]|[url=https://gabapentinpharm24.top/#]buy generic gabapentin[/url]|[url=https://cipropharm24.top/#]can i buy generic cipro without dr prescription[/url]
They offer the best prices on international brands.
A reliable pharmacy that connects patients globally.
https://clomidpharm24.top/
They make international medication sourcing a breeze.
Their medication reminders are such a thoughtful touch.
gabapentin powder solubility
The one-stop solution for all international medication requirements.
Quick, accurate, and dependable.
lisinopril tabs
The staff always remembers my name; it feels personal.
The best choice for personalized care.
cost of lisinopril in mexico
Their worldwide pharmacists’ consultations are invaluable.
They’re globally renowned for their impeccable service.
cost of cheap clomid tablets
Long-Term Effects.
Top 100 Searched Drugs.
[url=https://lisinoprilpharm24.top/#]lisinopril price increase[/url]|[url=https://clomidpharm24.top/#]where to get generic clomid without prescription[/url]|[url=https://cytotecpharm24.top/#]cost of cytotec tablets[/url]|[url=https://gabapentinpharm24.top/#]gabapentin 300 mg cap[/url]|[url=https://cipropharm24.top/#]how to buy cheap cipro without rx[/url]
They’ve revolutionized international pharmaceutical care.
They maintain a high standard of hygiene and cleanliness.
where to get cipro prices
The gold standard for international pharmaceutical services.
The pharmacists are always updated with the latest in medicine.
where can i buy cheap cipro price
Their digital prescription service is innovative and efficient.
Top-notch medications sourced globally.
where buy generic clomid prices
Some are medicines that help people when doctors prescribe.
Setting the benchmark for global pharmaceutical services.
[url=https://lisinoprilpharm24.top/#]lisinopril price uk[/url]|[url=https://clomidpharm24.top/#]cost of generic clomid no prescription[/url]|[url=https://cytotecpharm24.top/#]how to buy generic cytotec without rx[/url]|[url=https://gabapentinpharm24.top/#]using gabapentin for sciatica[/url]|[url=https://cipropharm24.top/#]can i order generic cipro prices[/url]
Best and news about drug.
Get warning information here.
where to buy clomid without dr prescription
Always stocked with what I need.
Bridging continents with their top-notch service.
https://lisinoprilpharm24.top/
Definitive journal of drugs and therapeutics.
A gem in our community.
can i get lisinopril
Been relying on them for years, and they never disappoint.
Always stocked with the best brands.
how to buy lisinopril pills
They are always proactive about refills and reminders.
They always prioritize the customer’s needs.
https://gabapentinpharm24.top/
A true asset to our neighborhood.
Commonly Used Drugs Charts.
[url=https://lisinoprilpharm24.top/#]lisinopril tablets 5mg[/url]|[url=https://clomidpharm24.top/#]can i purchase clomid prices[/url]|[url=https://cytotecpharm24.top/#]buy generic cytotec pill[/url]|[url=https://gabapentinpharm24.top/#]pharmacokinetics and metabolism of gabapentin in rat dog and man[/url]|[url=https://cipropharm24.top/#]cheap cipro without rx[/url]
A harmonious blend of local care and global expertise.
Their commitment to global patient welfare is commendable.
cost of generic clomid pills
Prescription Drug Information, Interactions & Side.
Their commitment to global excellence is unwavering.
gabapentin 300 mg for dogs side effects
They make international medication sourcing a breeze.
A beacon of trust in international pharmacy services.
https://gabapentinpharm24.top/
Their flu shots are quick and hassle-free.
Their commitment to healthcare excellence is evident.
how to get generic clomid no prescription
Their vaccination services are quick and easy.
They make international medication sourcing effortless.
can i order cipro price
Some trends of drugs.
Top-notch medications sourced globally.
https://cytotecpharm24.top/
Their free health check-ups are a wonderful initiative.
The team always keeps patient safety at the forefront.
[url=https://lisinoprilpharm24.top/#]lisinopril bullous pemphigoid[/url]|[url=https://clomidpharm24.top/#]buying cheap clomid without insurance[/url]|[url=https://cytotecpharm24.top/#]where can i get cheap cytotec prices[/url]|[url=https://gabapentinpharm24.top/#]conversion from gabapentin to lyrica[/url]|[url=https://cipropharm24.top/#]can i purchase cipro for sale[/url]
Every international delivery is prompt and secure.
All trends of medicament.
can you buy generic clomid without rx
Their health seminars are always enlightening.
Quick service without compromising on quality.
gabapentin and 100mg and dosage
They provide global solutions to local health challenges.
A pharmacy that genuinely cares about community well-being.
https://gabapentinpharm24.top/
Offering a global gateway to superior medications.
The staff always remembers my name; it feels personal.
buy cipro
I’m grateful for their around-the-clock service.
Medscape Drugs & Diseases.
[url=https://lisinoprilpharm24.top/#]can i order lisinopril no prescription[/url]|[url=https://clomidpharm24.top/#]buying cheap clomid pills[/url]|[url=https://cytotecpharm24.top/#]how to buy generic cytotec pills[/url]|[url=https://gabapentinpharm24.top/#]gabapentin lorazepam drug interaction[/url]|[url=https://cipropharm24.top/#]can i order cheap cipro without insurance[/url]
A trusted voice in global health matters.
Always up-to-date with the latest healthcare trends.
generic cytotec pill
I always find great deals in their monthly promotions.
Always up-to-date with the latest healthcare trends.
https://lisinoprilpharm24.top/
They have an extensive range of skincare products.
Their prices are unbeatable!
can i order generic cytotec
A beacon of excellence in pharmaceutical care.
Their international supply chain ensures no medication shortages.
where can i buy clomid without a prescription
The team embodies patience and expertise.
Trusted by patients from all corners of the world.
https://clomidpharm24.top/
Some trends of drugs.
Their international insights have benefited me greatly.
to buy gabapentin 600 mg
Their staff is always eager to help and assist.
Drugs information sheet.
[url=https://lisinoprilpharm24.top/#]where buy lisinopril[/url]|[url=https://clomidpharm24.top/#]buying clomid[/url]|[url=https://cytotecpharm24.top/#]can i purchase cheap cytotec prices[/url]|[url=https://gabapentinpharm24.top/#]can you take paxil and gabapentin together[/url]|[url=https://cipropharm24.top/#]how can i get generic cipro without dr prescription[/url]
Their worldwide delivery system is impeccable.
Their international team is incredibly knowledgeable.
buy generic clomid online
Their prescription savings club is a godsend.
Always responsive, regardless of time zones.
https://clomidpharm24.top/
Their global network ensures the best medication prices.
Making global healthcare accessible and affordable.
can you get generic clomid without prescription
A beacon of excellence in pharmaceutical care.
They set the tone for international pharmaceutical excellence.
get cheap clomid for sale
Their global outlook is evident in their expansive services.
Clean, well-organized, and easy to navigate.
https://clomidpharm24.top/
Best and news about drug.
They offer invaluable advice on health maintenance.
can i get clomid pill
The team always ensures that I understand my medication fully.
From greeting to checkout, always a pleasant experience.
[url=https://lisinoprilpharm24.top/#]cost lisinopril online[/url]|[url=https://clomidpharm24.top/#]can you buy clomid without rx[/url]|[url=https://cytotecpharm24.top/#]can i buy cytotec no prescription[/url]|[url=https://gabapentinpharm24.top/#]gabapentin major side effects[/url]|[url=https://cipropharm24.top/#]can i order generic cipro pill[/url]
Efficient service with a personal touch.
They have expertise in handling international shipping regulations.
can i purchase cheap clomid prices
Consistently excellent, year after year.
They are always proactive about refills and reminders.
https://cipropharm24.top/
All trends of medicament.
They’ve revolutionized international pharmaceutical care.
can i buy generic clomid without dr prescription
Their health awareness campaigns are so informative.
A pharmacy that takes pride in community service.
can i order generic cipro tablets
A touchstone of international pharmacy standards.
Their online prescription system is so efficient.
[url=https://lisinoprilpharm24.top/#]can i get generic lisinopril without rx[/url]|[url=https://clomidpharm24.top/#]where to get generic clomid pill[/url]|[url=https://cytotecpharm24.top/#]generic of cytotec[/url]|[url=https://gabapentinpharm24.top/#]pharmacokinetics and metabolism of gabapentin in rat dog and man[/url]|[url=https://cipropharm24.top/#]cost generic cipro price[/url]
They provide a world of health solutions.
Their staff is always eager to help and assist.
https://cipropharm24.top/
Their compounding services are impeccable.
Always ahead of the curve with global healthcare trends.
buy clomid without insurance
Their worldwide outreach programs are commendable.
They offer world-class service, bar none.
can i get generic cytotec
Medscape Drugs & Diseases.
Love their spacious and well-lit premises.
https://cytotecpharm24.top/
The best place for quality health products.
Long-Term Effects.
can i order cheap cytotec no prescription
Their commitment to global excellence is unwavering.
A pharmacy that prioritizes global health.
[url=https://lisinoprilpharm24.top/#]buying generic lisinopril without insurance[/url]|[url=https://clomidpharm24.top/#]can i purchase generic clomid without prescription[/url]|[url=https://cytotecpharm24.top/#]cytotec order[/url]|[url=https://gabapentinpharm24.top/#]gabapentin dose to get high[/url]|[url=https://cipropharm24.top/#]can you buy cheap cipro for sale[/url]
Their medication synchronization service is fantastic.
Trusted by patients from all corners of the world.
can i get cheap lisinopril without rx
Leading the way in global pharmaceutical services.
They stock quality medications from all over the world.
https://gabapentinpharm24.top/
They always have valuable advice on medication management.
They offer the best prices on international brands.
can i purchase generic cytotec without a prescription
The gold standard for international pharmaceutical services.
The most trustworthy pharmacy in the region.
how to buy cipro pills
Read information now.
An unmatched titan in the world of international pharmacies.
where to buy clomid without dr prescription
Providing global access to life-saving medications.
A touchstone of international pharmacy standards.
https://cipropharm24.top/
Their pet medication section is comprehensive.
A pharmacy I wholeheartedly recommend to others.
[url=https://lisinoprilpharm24.top/#]where to get lisinopril no prescription[/url]|[url=https://clomidpharm24.top/#]how can i get generic clomid without prescription[/url]|[url=https://cytotecpharm24.top/#]can you get cytotec without prescription[/url]|[url=https://gabapentinpharm24.top/#]gabapentin retrograde ejaculation[/url]|[url=https://cipropharm24.top/#]get generic cipro without prescription[/url]
I’ve never had to wait long for a prescription here.
Outstanding service, no matter where you’re located.
can i purchase cheap cytotec without prescription
A harmonious blend of local care and global expertise.
Always providing clarity and peace of mind.
can i buy generic lisinopril without insurance
Consistently excellent, year after year.
http://fastfromindia.com/# п»їlegitimate online pharmacies india
Fast From India
buy medicines online in india: Fast From India – Fast From India
mail order pharmacy india: indianpharmacy com – Fast From India
online pharmacy india [url=https://fastfromindia.shop/#]india pharmacy mail order[/url] Fast From India
indian pharmacy online
https://fastfromindia.shop/# indian pharmacy online
buy medicines online in india
indian pharmacy paypal: indian pharmacies safe – india pharmacy mail order
https://fastfromindia.com/# online pharmacy india
Fast From India
top online pharmacy india [url=https://fastfromindia.com/#]Fast From India[/url] Fast From India
pharmacy website india
top 10 pharmacies in india: Fast From India – pharmacy website india
Fast From India: buy medicines online in india – best online pharmacy india
https://fastfromindia.shop/# Fast From India
india online pharmacy
indian pharmacy: Fast From India – Online medicine home delivery
Fast From India: indian pharmacy online – india pharmacy mail order
Fast From India [url=http://fastfromindia.com/#]india pharmacy[/url] india online pharmacy
online shopping pharmacy india
online shopping pharmacy india: indian pharmacy – pharmacy website india
mail order pharmacy india: reputable indian online pharmacy – indianpharmacy com
https://fastfromindia.com/# buy prescription drugs from india
best india pharmacy
Fast From India: Fast From India – Fast From India
Pharma Internationale [url=https://pharmainternationale.com/#]Pharma Internationale[/url] pharmacie en ligne france livraison belgique
Pharma Internationale: pharmacie en ligne livraison europe – Pharma Internationale
https://pharmainternationale.shop/# Pharma Internationale
pharmacies en ligne certifiГ©es
Pharmacie Internationale en ligne: pharmacie en ligne france livraison belgique – Pharmacie en ligne livraison Europe
Pharma Internationale [url=https://pharmainternationale.com/#]vente de mГ©dicament en ligne[/url] Pharmacie sans ordonnance
Pharma Internationale: Pharma Internationale – Pharma Internationale
https://pharmainternationale.com/# pharmacie en ligne pas cher
Pharma Internationale
Achat mГ©dicament en ligne fiable: Pharma Internationale – pharmacies en ligne certifiГ©es
Pharmacie sans ordonnance: Pharma Internationale – trouver un mГ©dicament en pharmacie
https://pharmainternationale.com/# pharmacie en ligne france fiable
Pharma Internationale
pharmacies en ligne certifiГ©es [url=https://pharmainternationale.com/#]Pharma Internationale[/url] Pharma Internationale
Pharma Internationale: pharmacie en ligne livraison europe – Pharmacie Internationale en ligne
Pharmacie Internationale en ligne: Pharma Internationale – Pharma Internationale
http://pharmainternationale.com/# pharmacies en ligne certifiГ©es
Pharma Internationale
Farmacia Medic: Farmacia Medic – farmacia online madrid
farmacias online seguras [url=https://farmaciamedic.com/#]farmacia en casa online descuento[/url] Farmacia Medic
farmacias direct: п»їfarmacia online espaГ±a – farmacia barata
http://farmaciamedic.com/# Farmacia Medic
farmacias direct
Farmacia Medic: п»їfarmacia online espaГ±a – Farmacia Medic
farmacias online seguras en espaГ±a: farmacia online 24 horas – Farmacia Medic
https://farmaciamedic.com/# Farmacia Medic
Farmacia Medic
Farmacia Medic: Farmacia Medic – farmacia online madrid
farmacia online madrid [url=http://farmaciamedic.com/#]farmacia online barata[/url] Farmacia Medic
farmacia online barcelona: Farmacia Medic – farmacias online baratas
farmacias online seguras en espaГ±a: farmacia online barata y fiable – Farmacia Medic
Farmacia Medic: Farmacia Medic – Farmacia Medic
https://topmaxfarma.com/# farmacia online piГ№ conveniente
farmacie online sicure
Top Max Farma: farmacie online autorizzate elenco – Top Max Farma
Top Max Farma: Top Max Farma – Top Max Farma
http://topmaxfarma.com/# Top Max Farma
acquistare farmaci senza ricetta [url=https://topmaxfarma.com/#]Top Max Farma[/url] Top Max Farma
comprare farmaci online con ricetta [url=https://topmaxfarma.shop/#]п»їFarmacia online migliore[/url] farmacia online
https://topmaxfarma.shop/# Top Max Farma
comprare farmaci online all’estero
п»їFarmacia online migliore: migliori farmacie online 2024 – farmacie online affidabili
https://topmaxfarma.com/# Top Max Farma
Top Max Farma [url=https://topmaxfarma.shop/#]Top Max Farma[/url] acquisto farmaci con ricetta
farmacie online affidabili [url=https://topmaxfarma.com/#]acquistare farmaci senza ricetta[/url] Farmacie on line spedizione gratuita
Top Max Farma: Farmacia online piГ№ conveniente – farmacie online autorizzate elenco
https://topmaxfarma.shop/# Top Max Farma
Top Max Farma [url=http://topmaxfarma.com/#]farmacia online piГ№ conveniente[/url] Top Max Farma
Top Max Farma: acquistare farmaci senza ricetta – Top Max Farma
Top Max Farma [url=https://topmaxfarma.com/#]п»їFarmacia online migliore[/url] Top Max Farma
https://topmaxfarma.com/# acquisto farmaci con ricetta
top farmacia online
mexican pharmacy acp: mexican pharmacy acp – mexican pharmacy acp
https://mexicanpharmacyacp.com/# mexican pharmacy acp
top 10 online pharmacy in india
medicine in mexico pharmacies: buying prescription drugs in mexico – mexican pharmacy acp
http://canadianpharmacyaapd.com/# canada drugs
mexican rx online
mexican pharmacy acp [url=https://mexicanpharmacyacp.com/#]mexican pharmacy acp[/url] mexican pharmacy acp
India pharmacy ship to USA: indian pharmacy – Indian pharmacy international shipping
Indian pharmacy online: Online medicine order – Online medicine home delivery
https://canadianpharmacyaapd.com/# canadian neighbor pharmacy
medicine in mexico pharmacies
best canadian pharmacy to buy from: northwest pharmacy canada – canadian pharmacy 1 internet online drugstore
canadian pharmacy scam [url=http://canadianpharmacyaapd.com/#]recommended canadian pharmacies[/url] canadian 24 hour pharmacy
https://indianpharmacyabp.com/# Indian Pharmacy Abp
top 10 online pharmacy in india
buying prescription drugs in mexico: mexican pharmacy acp – mexican pharmacy acp
https://mexicanpharmacyacp.com/# buying prescription drugs in mexico
mexican mail order pharmacies
india pharmacy: Best online Indian pharmacy – Indian pharmacy international shipping
https://indianpharmacyabp.com/# Online medicine home delivery
mexican drugstore online
mexico pharmacies prescription drugs: mexico drug stores pharmacies – mexican pharmacy acp
canadian pharmacy: canadian drugs online – canadian pharmacy phone number
canada discount pharmacy [url=https://canadianpharmacyaapd.com/#]Canadian Pharmacy AAPD[/url] canada drugs online review
https://indianpharmacyabp.shop/# India pharmacy ship to USA
mexican online pharmacies prescription drugs
Indian pharmacy international shipping: Indian pharmacy online – Online medicine home delivery
mexican pharmacy acp: pharmacies in mexico that ship to usa – mexican pharmacy acp
Online medicine home delivery: IndianPharmacyAbp – Best online Indian pharmacy
mexico pharmacies prescription drugs: mexican pharmacy acp – buying from online mexican pharmacy
mexican pharmacy acp [url=https://mexicanpharmacyacp.com/#]mexican pharmacy acp[/url] buying from online mexican pharmacy
http://indianpharmacyabp.com/# Indian pharmacy international shipping
mexico drug stores pharmacies
Indian Pharmacy Abp: Best online Indian pharmacy – IndianPharmacyAbp
IndianPharmacyAbp: IndianPharmacyAbp – Indian Pharmacy Abp
medication from mexico pharmacy: purple pharmacy mexico price list – mexican pharmacy acp
safe reliable canadian pharmacy: Canadian Pharmacy AAPD – canadian mail order pharmacy
mexican pharmacy acp: mexican online pharmacies prescription drugs – mexican pharmacy acp
best online canadian pharmacy: Canadian Pharmacy AAPD – reliable canadian pharmacy reviews
india pharmacy mail order: indian pharmacy – IndianPharmacyAbp
canadian pharmacy scam [url=https://canadianpharmacyaapd.shop/#]Canadian Pharmacy AAPD[/url] recommended canadian pharmacies
Best online Indian pharmacy: Online medicine home delivery – Indian Pharmacy Abp
canadian mail order pharmacy: Canadian Pharmacy AAPD – best rated canadian pharmacy
canadadrugpharmacy com: canadian online pharmacy – canadianpharmacy com
prescription drugs canada buy online: Canadian Pharmacy AAPD – canadian pharmacy cheap
Indian Pharmacy Abp [url=http://indianpharmacyabp.com/#]Indian Pharmacy Abp[/url] Best online Indian pharmacy
canadian discount pharmacy: Canadian Pharmacy AAPD – pharmacy in canada
canadian pharmacies compare: vipps approved canadian online pharmacy – pet meds without vet prescription canada
reliable canadian pharmacy: canadian pharmacy in canada – onlinecanadianpharmacy 24
Best Indian pharmacy: Indian pharmacy online – indian pharmacy
mexican pharmacy acp [url=https://mexicanpharmacyacp.shop/#]mexican pharmacy acp[/url] mexican pharmacy acp
IndianPharmacyAbp: Best Indian pharmacy – IndianPharmacyAbp
global pharmacy canada: safe online pharmacies in canada – canadian pharmacy india
п»їbest mexican online pharmacies: mexican pharmacy acp – mexico drug stores pharmacies
https://akhbutina.kz/# Ballon радует игроков разнообразием функций.
balloon казино официальный сайт [url=https://neokomsomol.kz/#]balloon казино играть[/url] Каждый СЃРїРёРЅ может стать выигрышным!
Сыграйте РЅР° деньги, почувствуйте азарт!: balloon игра на деньги – balloon игра
Автомат Ballon — идеальный СЃРїРѕСЃРѕР± расслабиться.: balloon game – balloon игра на деньги
РРіСЂР° РЅР° деньги — это ваше развлечение.: balloon game – balloon игра на деньги
Рграть РІ казино — всегда интересное приключение.: balloon казино официальный сайт – balloon игра
Ballon — это РёРіСЂР° СЃ удивительными графиками.: balloon игра на деньги – balloon игра на деньги
Рграйте РІ казино, наслаждайтесь каждым моментом.: balloon игра на деньги – balloon игра
balloon game [url=https://neokomsomol.kz/#]balloon игра[/url] Ballon — это РёРіСЂР° СЃ удивительными графиками.
https://balloonigra.kz/# Рграйте РІ казино, наслаждайтесь каждым моментом.
Казино — это место для больших выигрышей.: balloon казино играть – balloon game
Заходите РІ казино, чтобы испытать удачу.: balloon game – balloon казино демо
Автоматы Ballon поражают своей красочностью.: balloon game – balloon игра на деньги
Удача всегда СЂСЏРґРѕРј, РєРѕРіРґР° играешь.: balloon казино играть – balloon казино играть
https://balloonigra.kz/# Ргровые автоматы Ballon Р¶РґСѓС‚ СЃРІРѕРёС… героев.
Выигрывайте большие СЃСѓРјРјС‹ РЅР° автоматах!: balloon казино – balloon игра
Рграйте РІ Ballon Рё наслаждайтесь процессом.: balloon казино – balloon игра на деньги
Ballon радует РёРіСЂРѕРєРѕРІ разнообразием функций.: balloon игра на деньги – balloon казино демо
balloon игра на деньги [url=https://neokomsomol.kz/#]balloon казино играть[/url] Баллон — это автомат для настоящих любителей.
https://balloonigra.kz/# Ballon — идеальный выбор для азартных игроков.
Ballon — выберите СЃРІРѕР№ путь Рє победе.: balloon game – balloon казино играть
Р’ казино всегда есть что-то РЅРѕРІРѕРµ.: balloon казино официальный сайт – balloon казино официальный сайт
https://akhbutina.kz/# Рграйте РІ Ballon Рё наслаждайтесь процессом.
Казино — это место для больших выигрышей.: balloon казино играть – balloon казино
balloon игра [url=https://neokomsomol.kz/#]balloon игра на деньги[/url] Автоматы Ballon поднимают настроение каждому.
Баллон — это автомат для настоящих любителей.: balloon казино – balloon игра на деньги
https://akhbutina.kz/# Автоматы Ballon поражают своей красочностью.
Автоматы Ballon поражают своей красочностью.: balloon game – balloon казино
Крути барабаны Рё Р¶РґРё победы!: balloon казино – balloon игра на деньги
https://akhbutina.kz/# Баллон — это автомат для настоящих любителей.
balloon казино играть [url=https://balloonigra.kz/#]balloon казино официальный сайт[/url] Казино — РјРёСЂ азартных приключений.
Выигрывайте большие СЃСѓРјРјС‹ РЅР° автоматах!: balloon казино играть – balloon игра
https://akhbutina.kz/# Казино предлагает множество игровых автоматов.
Каждый СЃРїРёРЅ может стать выигрышным!: balloon казино официальный сайт – balloon казино
https://88betviet.pro/# keo nha cai 88bet
k8 th? dam: link vao k8 – k8 bet
k8vip [url=https://k8viet.gurum/#]nha cai k8[/url] k8vip
http://88betviet.pro/# 88 bet
alo789 chinh th?c: alo 789 dang nh?p – alo789in
https://k8viet.gurum/# k8vip
keo nha cai 88bet: keo nha cai 88bet – 88 bet
http://88betviet.pro/# 88bet slot
keo nha cai 88bet: nha cai 88bet – 88bet
https://k8viet.guru/# link vao k8
alo 789: alo789hk – 789alo
http://88betviet.pro/# 188bet 88bet
alo 789: 789alo – alo 789 dang nh?p
http://88betviet.pro/# 88 bet
dang nh?p alo789 [url=http://alo789.auction/#]alo789 chinh th?c[/url] alo789hk
88bet: keo nha cai 88bet – 88bet
https://alo789.auction/# alo 789
https://alo789.auction/# alo 789
88bet slot: 188bet 88bet – keo nha cai 88bet
https://88betviet.pro/# 88 bet
88bet slot [url=https://88betviet.pro/#]188bet 88bet[/url] keo nha cai 88bet
http://88betviet.pro/# 88bet
keo nha cai 88bet: 88 bet – 88 bet
https://88betviet.pro/# 88 bet
https://88betviet.pro/# nha cai 88bet
alo 789 [url=http://alo789.auction/#]alo 789[/url] dang nh?p alo789
https://alo789.auction/# alo789
alo 789: alo789 chinh th?c – dang nh?p alo789
https://k8viet.guru/# k8 th? dam
https://k8viet.guru/# nha cai k8
nha cai 88bet: 188bet 88bet – nha cai 88bet
http://88betviet.pro/# 188bet 88bet
88bet [url=https://88betviet.pro/#]88bet slot[/url] 88bet
https://alo789.auction/# alo 789
alo789 dang nh?p: alo 789 – dang nh?p alo789
https://alo789.auction/# alo789in
keo nha cai 88bet [url=https://88betviet.pro/#]keo nha cai 88bet[/url] 88bet
https://88betviet.pro/# 88bet
alo789: dang nh?p alo789 – dang nh?p alo789
https://k8viet.guru/# k8vip
https://mexicanpharminter.shop/# MexicanPharmInter
canadian online pharmacy
cheapest online pharmacy india: buying prescription drugs from india – IndiaMedFast
MexicanPharmInter: mexican pharmacy online order – reliable mexican pharmacies
https://interpharmonline.com/# canadian drug pharmacy
safe canadian pharmacies
mexican pharmacy online [url=https://mexicanpharminter.com/#]mexican drug stores online[/url] MexicanPharmInter
Mexican Pharm International: mexican drug stores online – MexicanPharmInter
http://indiamedfast.com/# cheapest online pharmacy india
canadian world pharmacy
order medicines online india: india online pharmacy store – india online pharmacy store
best canadian online pharmacy: legitimate canadian pharmacies online – canadianpharmacymeds com
https://interpharmonline.shop/# canadian pharmacy ltd
best canadian pharmacy
Mexican Pharm International [url=https://mexicanpharminter.shop/#]mexican pharmacy online order[/url] buying from online mexican pharmacy
http://interpharmonline.com/# best online canadian pharmacy
canadian pharmacy scam
https://indiamedfast.com/# IndiaMedFast
mexican pharmacy online store: reliable mexican pharmacies – mexican pharmacy online
Mexican Pharm Inter: Mexican Pharm International – MexicanPharmInter
mexican pharmacy online order [url=https://mexicanpharminter.com/#]mexican drug stores online[/url] buying from online mexican pharmacy
http://mexicanpharminter.com/# buying from online mexican pharmacy
canadian pharmacies compare
http://mexicanpharminter.com/# Mexican Pharm Inter
MexicanPharmInter: mexican drug stores online – Mexican Pharm Inter
https://interpharmonline.shop/# canadian pharmacy ltd
rate canadian pharmacies
https://interpharmonline.com/# adderall canadian pharmacy
buying from canadian pharmacies: online canadian pharmacy no prescription – pharmacies in canada that ship to the us
buying prescription drugs from india [url=https://indiamedfast.shop/#]buying prescription drugs from india[/url] India Med Fast
cheapest online pharmacy india: buying prescription drugs from india – IndiaMedFast
http://interpharmonline.com/# certified canadian pharmacy
canada drugs
https://interpharmonline.shop/# legit canadian pharmacy online
maple leaf pharmacy in canada: Cheapest online pharmacy – drugs from canada
https://interpharmonline.com/# canadian pharmacy king
cheap canadian pharmacy online
mexican pharmacy online order: buying from online mexican pharmacy – mexican drug stores online
https://interpharmonline.com/# buying drugs from canada
trustworthy canadian pharmacy [url=http://interpharmonline.com/#]fda approved canadian online pharmacies[/url] best canadian pharmacy to order from
https://tadalafileasybuy.com/# Cialis without a doctor prescription
http://generic100mgeasy.com/# sildenafil 50 mg price
kamagra kopen nederland: kamagra jelly kopen – kamagra 100mg kopen
TadalafilEasyBuy.com: cialis without a doctor prescription – Tadalafil Easy Buy
https://tadalafileasybuy.shop/# п»їcialis generic
Generic 100mg Easy [url=http://generic100mgeasy.com/#]Generic100mgEasy[/url] Generic100mgEasy
https://kamagrakopen.pro/# kamagra pillen kopen
cialis without a doctor prescription: TadalafilEasyBuy.com – TadalafilEasyBuy.com
Tadalafil Easy Buy: cialis without a doctor prescription – cialis for sale
Thanks for sharing. I read many of your blog posts, cool, your blog is very good.
http://tadalafileasybuy.com/# Tadalafil Easy Buy
https://tadalafileasybuy.com/# Tadalafil Easy Buy
cialis without a doctor prescription: cialis without a doctor prescription – п»їcialis generic
buy generic 100mg viagra online: Buy generic 100mg Viagra online – Buy Viagra online cheap
kamagra kopen nederland [url=https://kamagrakopen.pro/#]kamagra jelly kopen[/url] kamagra jelly kopen
https://generic100mgeasy.shop/# buy generic 100mg viagra online
https://tadalafileasybuy.com/# cialis without a doctor prescription
Tadalafil Easy Buy: TadalafilEasyBuy.com – Cheap Cialis
Kamagra Kopen: KamagraKopen.pro – kamagra jelly kopen
https://generic100mgeasy.com/# Generic 100mg Easy
http://tadalafileasybuy.com/# Cheap Cialis
Generic100mgEasy [url=https://generic100mgeasy.com/#]Generic100mgEasy[/url] Viagra online price
viagra canada: Generic 100mg Easy – Generic 100mg Easy
Viagra generic over the counter: best price for viagra 100mg – buy generic 100mg viagra online
https://kamagrakopen.pro/# kamagra jelly kopen
https://kamagrakopen.pro/# Officiele Kamagra van Nederland
Generic100mgEasy: buy generic 100mg viagra online – Viagra online price
kamagra 100mg kopen: kamagra gel kopen – kamagra kopen nederland
https://generic100mgeasy.com/# Viagra without a doctor prescription Canada
Kamagra Kopen Online [url=https://kamagrakopen.pro/#]kamagra jelly kopen[/url] Officiele Kamagra van Nederland
https://tadalafileasybuy.shop/# TadalafilEasyBuy.com
Generic 100mg Easy: buy generic 100mg viagra online – sildenafil over the counter
KamagraKopen.pro: kamagra pillen kopen – Kamagra Kopen
https://tadalafileasybuy.com/# Tadalafil Easy Buy
kamagra kopen nederland: Kamagra Kopen – Kamagra
https://tadalafileasybuy.shop/# cheapest cialis
kamagra jelly kopen [url=https://kamagrakopen.pro/#]kamagra pillen kopen[/url] KamagraKopen.pro
Kamagra Kopen: Officiele Kamagra van Nederland – Kamagra
https://tadalafileasybuy.shop/# Generic Cialis price
Cheap Sildenafil 100mg: Generic 100mg Easy – buy generic 100mg viagra online
http://generic100mgeasy.com/# Generic100mgEasy
http://tadalafileasybuy.com/# TadalafilEasyBuy.com
https://tadalafileasybuy.shop/# Tadalafil Easy Buy
Tadalafil Easy Buy: Tadalafil Easy Buy – Cheap Cialis
Tadalafil Easy Buy: cialis without a doctor prescription – Tadalafil Easy Buy
Cheap Viagra 100mg [url=https://generic100mgeasy.com/#]Generic100mgEasy[/url] Cheap Sildenafil 100mg
https://tadalafileasybuy.shop/# cialis without a doctor prescription
http://generic100mgeasy.com/# buy generic 100mg viagra online
buy cialis pill: cialis without a doctor prescription – Generic Cialis without a doctor prescription
cialis without a doctor prescription: Buy Tadalafil 20mg – Generic Tadalafil 20mg price
пин ап казино официальный сайт – пин ап
Viagra generic over the counter [url=https://generic100mgeasy.com/#]Generic 100mg Easy[/url] Generic 100mg Easy
pinup 2025 – пин ап казино зеркало
пин ап казино: https://pinupkz.life/
пин ап казино – pinup 2025
пин ап казино зеркало: https://pinupkz.life/
пин ап казино зеркало: https://pinupkz.life/
пинап казино – пин ап зеркало
пин ап казино официальный сайт – пин ап казино официальный сайт
пин ап казино зеркало: https://pinupkz.life/
пин ап казино официальный сайт – пин ап казино
kamagra kopen nederland [url=https://kamagrakopen.pro/#]kamagra pillen kopen[/url] kamagra kopen nederland
пин ап: https://pinupkz.life/
пин ап вход – пин ап казино
pinup 2025: https://pinupkz.life/
buy generic 100mg viagra online [url=https://generic100mgeasy.com/#]Generic100mgEasy[/url] Generic 100mg Easy
пин ап зеркало – пин ап казино зеркало
apotek online recept: Apotek hemleverans idag – apotek online
Apoteket online: Apotek hemleverans recept – Apoteket online
Apoteket online [url=http://apotekonlinerecept.com/#]apotek pa nett[/url] apotek pa nett
https://apotheekmax.shop/# Betrouwbare online apotheek zonder recept
https://kamagrapotenzmittel.shop/# Kamagra kaufen
apotek online recept: apotek online recept – apotek online
Kamagra Oral Jelly kaufen: Kamagra kaufen – Kamagra Oral Jelly
http://apotekonlinerecept.com/# apotek pa nett
https://apotheekmax.com/# Apotheek Max
apotek online: apotek online recept – Apotek hemleverans recept
Kamagra online bestellen [url=https://kamagrapotenzmittel.shop/#]Kamagra Oral Jelly kaufen[/url] Kamagra kaufen ohne Rezept
Apotheek Max: Apotheek Max – de online drogist kortingscode
https://apotheekmax.com/# Online apotheek Nederland met recept
https://apotheekmax.shop/# Online apotheek Nederland zonder recept
ApotheekMax: Betrouwbare online apotheek zonder recept – online apotheek
Apotek hemleverans recept: apotek pa nett – Apotek hemleverans recept
http://kamagrapotenzmittel.com/# Kamagra Oral Jelly kaufen
http://apotekonlinerecept.com/# apotek pa nett
ApotheekMax: online apotheek – ApotheekMax
http://kamagrapotenzmittel.com/# Kamagra Oral Jelly
https://kamagrapotenzmittel.shop/# Kamagra Oral Jelly
Kamagra Oral Jelly: Kamagra online bestellen – Kamagra Oral Jelly
Apotek hemleverans idag [url=https://apotekonlinerecept.shop/#]apotek online recept[/url] Apotek hemleverans recept
Apotek hemleverans recept: apotek pa nett – Apotek hemleverans recept
https://apotekonlinerecept.shop/# Apotek hemleverans idag
https://kamagrapotenzmittel.shop/# Kamagra Gel
kamagra: kamagra – Kamagra kaufen ohne Rezept
https://kamagrapotenzmittel.shop/# Kamagra Original
Kamagra Gel: Kamagra online bestellen – Kamagra kaufen
Kamagra online bestellen [url=https://kamagrapotenzmittel.shop/#]Kamagra Original[/url] Kamagra Oral Jelly kaufen
http://apotheekmax.com/# Beste online drogist
http://apotekonlinerecept.com/# apotek online
https://kamagrapotenzmittel.com/# Kamagra Oral Jelly
https://apotekonlinerecept.shop/# Apotek hemleverans idag
Apotheek online bestellen: Online apotheek Nederland met recept – Online apotheek Nederland zonder recept
Apotek hemleverans idag [url=http://apotekonlinerecept.com/#]Apotek hemleverans recept[/url] Apotek hemleverans recept
Betrouwbare online apotheek zonder recept: Apotheek Max – Beste online drogist
https://apotekonlinerecept.shop/# apotek online recept
https://apotekonlinerecept.shop/# apotek online recept
Online apotheek Nederland met recept: Apotheek online bestellen – online apotheek
de online drogist kortingscode: Betrouwbare online apotheek zonder recept – Online apotheek Nederland met recept
https://apotheekmax.shop/# Beste online drogist
Kamagra online bestellen [url=https://kamagrapotenzmittel.com/#]kamagra[/url] Kamagra Oral Jelly kaufen
https://apotheekmax.shop/# ApotheekMax
apotek online recept: apotek online – apotek pa nett
https://kamagrapotenzmittel.shop/# Kamagra kaufen ohne Rezept
Agb Mexico Pharm: mexican online pharmacies prescription drugs – medication from mexico pharmacy
https://wwwindiapharm.com/# top online pharmacy india
canadian pharmacy meds: go canada pharm – my canadian pharmacy
canadian pharmacy 365 [url=https://gocanadapharm.shop/#]canadianpharmacymeds com[/url] canadian pharmacy 24h com
Agb Mexico Pharm: Agb Mexico Pharm – Agb Mexico Pharm
reputable mexican pharmacies online: mexican mail order pharmacies – purple pharmacy mexico price list
www india pharm: buy prescription drugs from india – indian pharmacy
https://wwwindiapharm.com/# www india pharm
reputable indian online pharmacy: www india pharm – www india pharm
my canadian pharmacy review: GoCanadaPharm – canadian online drugs
canadian pharmacy oxycodone [url=https://gocanadapharm.shop/#]go canada pharm[/url] legit canadian pharmacy
canada cloud pharmacy: GoCanadaPharm – canadian family pharmacy
https://agbmexicopharm.com/# buying prescription drugs in mexico online
buying from online mexican pharmacy: mexican border pharmacies shipping to usa – Agb Mexico Pharm
buying from online mexican pharmacy: Agb Mexico Pharm – purple pharmacy mexico price list
https://wwwindiapharm.com/# www india pharm
safe reliable canadian pharmacy: go canada pharm – canada pharmacy online
www india pharm: www india pharm – www india pharm
Online medicine home delivery [url=http://wwwindiapharm.com/#]top online pharmacy india[/url] www india pharm
purple pharmacy mexico price list: Agb Mexico Pharm – buying from online mexican pharmacy
www india pharm: online pharmacy india – Online medicine home delivery
https://gocanadapharm.shop/# canadian pharmacy price checker
Agb Mexico Pharm: Agb Mexico Pharm – Agb Mexico Pharm
canadian neighbor pharmacy: GoCanadaPharm – canadian pharmacy ltd
mexican online pharmacies prescription drugs: Agb Mexico Pharm – reputable mexican pharmacies online
online shopping pharmacy india [url=http://wwwindiapharm.com/#]best online pharmacy india[/url] www india pharm
http://wwwindiapharm.com/# www india pharm
п»їbest mexican online pharmacies: medicine in mexico pharmacies – mexican rx online
www india pharm: www india pharm – www india pharm
canadian pharmacy 24: GoCanadaPharm – legitimate canadian pharmacies
canadianpharmacymeds com: canadianpharmacy com – reputable canadian pharmacy
https://gocanadapharm.com/# canadapharmacyonline legit
mexico drug stores pharmacies: buying prescription drugs in mexico – Agb Mexico Pharm
canadian discount pharmacy: canadian medications – canada rx pharmacy
indian pharmacies safe [url=http://wwwindiapharm.com/#]www india pharm[/url] www india pharm
buying from online mexican pharmacy: Agb Mexico Pharm – purple pharmacy mexico price list
http://gocanadapharm.com/# pharmacy com canada
reputable indian pharmacies: indian pharmacy online – india online pharmacy
canada pharmacy online: go canada pharm – canadian pharmacy no rx needed
Agb Mexico Pharm: Agb Mexico Pharm – best online pharmacies in mexico
legitimate canadian mail order pharmacy [url=http://gocanadapharm.com/#]canadian pharmacy ed medications[/url] reliable canadian pharmacy
Agb Mexico Pharm: Agb Mexico Pharm – mexican border pharmacies shipping to usa
http://wwwindiapharm.com/# reputable indian pharmacies
Agb Mexico Pharm: mexico pharmacies prescription drugs – Agb Mexico Pharm
www india pharm: india pharmacy – reputable indian pharmacies
cost generic clomid without insurance: where buy cheap clomid without dr prescription – Clom Fast Pharm
Clom Fast Pharm: Clom Fast Pharm – can i get generic clomid prices
http://predpharmnet.com/# prednisone online india
Pred Pharm Net [url=https://predpharmnet.shop/#]Pred Pharm Net[/url] Pred Pharm Net
Clom Fast Pharm: Clom Fast Pharm – can you get clomid without insurance
can i get clomid online: can i order clomid pill – can i order generic clomid for sale
40 mg daily prednisone: Pred Pharm Net – Pred Pharm Net
https://amonlinepharm.com/# cheap amoxicillin 500mg
prednisone 10mg price in india: prednisone purchase online – Pred Pharm Net
ZithPharmOnline: can i buy zithromax over the counter in canada – ZithPharmOnline
ZithPharmOnline: zithromax 250 mg pill – ZithPharmOnline
zestril 10 mg in india [url=http://lisinexpress.com/#]buy cheap lisinopril 40mg[/url] Lisin Express
https://zithpharmonline.com/# ZithPharmOnline
Pred Pharm Net: prednisone rx coupon – 50 mg prednisone tablet
Lisin Express: lisinopril tabs 20mg – Lisin Express
Lisin Express: Lisin Express – Lisin Express
https://amonlinepharm.com/# AmOnlinePharm
where can i buy zithromax in canada: generic zithromax over the counter – zithromax 1000 mg pills
Pred Pharm Net: Pred Pharm Net – Pred Pharm Net
Pred Pharm Net [url=https://predpharmnet.com/#]Pred Pharm Net[/url] 5 mg prednisone daily
ZithPharmOnline: zithromax 500 tablet – ZithPharmOnline
https://amonlinepharm.shop/# AmOnlinePharm
Pred Pharm Net: Pred Pharm Net – Pred Pharm Net
Clom Fast Pharm: Clom Fast Pharm – Clom Fast Pharm
Clom Fast Pharm: where buy generic clomid without a prescription – Clom Fast Pharm
Clom Fast Pharm: where to get clomid without insurance – can i order cheap clomid without rx
https://predpharmnet.com/# prednisone price canada
purchase zithromax z-pak [url=https://zithpharmonline.shop/#]ZithPharmOnline[/url] ZithPharmOnline
buy generic clomid pill: cost clomid without a prescription – Clom Fast Pharm
buy zithromax without prescription online: ZithPharmOnline – ZithPharmOnline
AmOnlinePharm: AmOnlinePharm – amoxicillin 500mg capsule buy online
https://zithpharmonline.shop/# buy zithromax online
ZithPharmOnline: zithromax 600 mg tablets – ZithPharmOnline
lisinopril 20 mg canadian: buy lisinopril without prescription – Lisin Express
lisinopril 20 mg buy: Lisin Express – buy lisinopril 20 mg without prescription
zithromax 600 mg tablets [url=https://zithpharmonline.shop/#]can you buy zithromax over the counter in canada[/url] cost of generic zithromax
Clom Fast Pharm: how can i get cheap clomid without a prescription – Clom Fast Pharm
Lisin Express: where can i order lisinopril online – Lisin Express
AmOnlinePharm: AmOnlinePharm – AmOnlinePharm
where can i get zithromax: buy zithromax without prescription online – how to get zithromax online
https://amonlinepharm.shop/# AmOnlinePharm
Clom Fast Pharm: Clom Fast Pharm – Clom Fast Pharm
buy amoxicillin online mexico [url=https://amonlinepharm.com/#]AmOnlinePharm[/url] amoxicillin order online no prescription
lisinopril 20mg for sale: where to buy lisinopril – lisinopril 10 mg tablet cost
amoxicillin online no prescription: AmOnlinePharm – AmOnlinePharm
https://zithpharmonline.com/# ZithPharmOnline
AmOnlinePharm: amoxicillin online pharmacy – can you buy amoxicillin over the counter
amoxicillin 500mg buy online canada: AmOnlinePharm – cheap amoxicillin 500mg
lisansl? casino siteleri: guvenilir casino siteleri – guvenilir casino siteleri casinositeleri1st.com
https://sweetbonanza1st.com/# sweet bonanza giris
sweet bonanza slot: sweet bonanza oyna – sweet bonanza 1st sweetbonanza1st.shop
sweet bonanza [url=http://sweetbonanza1st.com/#]sweet bonanza slot[/url] sweet bonanza demo sweetbonanza1st.com
bahis siteleri isimleri: casibom resmi – betler casibom1st.com
yeni siteler bahis: casibom giris adresi – п»їcasino casibom1st.com
sweet bonanza slot: sweet bonanza demo – sweet bonanza sweetbonanza1st.shop
https://casibom1st.com/# canli oyun
sweet bonanza giris: sweet bonanza demo – sweet bonanza sweetbonanza1st.shop
lisansl? casino siteleri: lisansl? casino siteleri – guvenilir casino siteleri casinositeleri1st.com
bonus veren bahis siteleri yasal [url=http://casibom1st.com/#]casibom giris[/url] en gГјvenilir bahis siteleri hangileri? casibom1st.shop
gГјvenilir bahis siteleri 2025: casibom guncel giris – online casino bet casibom1st.com
en iyi yatД±rД±m siteleri: casibom giris adresi – en yeni kaГ§ak bahis siteleri casibom1st.com
lisansl? casino siteleri: guvenilir casino siteleri – casino siteleri casinositeleri1st.com
casino siteleri: guvenilir casino siteleri – casino siteleri casinositeleri1st.com
casino siteleri [url=https://casinositeleri1st.com/#]casino siteleri[/url] casino siteleri casinositeleri1st.shop
casino siteleri: lisansl? casino siteleri – lisansl? casino siteleri casinositeleri1st.com
sweet bonanza oyna: sweet bonanza siteleri – sweet bonanza siteleri sweetbonanza1st.shop
rcasino: casibom guncel giris – date sitesi casibom1st.com
sweet bonanza oyna: sweet bonanza – sweet bonanza demo sweetbonanza1st.shop
tГјm casino siteleri: casibom giris – en iyi casino sitesi casibom1st.com
casino siteleri: casino siteleri – casino siteleri casinositeleri1st.com
sweet bonanza 1st [url=https://sweetbonanza1st.shop/#]sweet bonanza yorumlar[/url] sweet bonanza oyna sweetbonanza1st.com
sweet bonanza slot: sweet bonanza siteleri – sweet bonanza demo sweetbonanza1st.shop
casino siteleri: casino siteleri 2025 – slot casino siteleri casinositeleri1st.com
en iyi yabancД± bahis siteleri: casibom – bahis oyun siteleri casibom1st.com
hangi bahis siteleri bonus veriyor?: casibom giris adresi – casino kumar oyunlarД± casibom1st.com
orjinal siteler: deneme bonusu veren siteler – casino siteleri 2025 casinositeleri1st.com
sweet bonanza demo: sweet bonanza – sweet bonanza slot sweetbonanza1st.shop
ilk Гјyelik deneme bonusu veren siteler [url=https://casibom1st.com/#]casibom guncel adres[/url] en gГјvenilir online casino casibom1st.shop
guvenilir casino siteleri: deneme bonusu veren siteler – casino siteleri 2025 casinositeleri1st.com
https://sweetbonanza1st.com/# sweet bonanza siteleri
casino oyna: casibom guncel giris – gercek para kazandД±ran casino oyunlarД± casibom1st.com
deneme bonusu veren siteler: deneme bonusu veren siteler – casino siteleri casinositeleri1st.com
spor siteleri listesi: casibom 1st – tГјrkiye nin en iyi yasal bahis sitesi casibom1st.com
casino siteleri 2025: casino siteleri – casino siteleri casinositeleri1st.com
deneme bonusu veren yeni casino siteleri: casibom giris – gГјvenilir casino siteleri casibom1st.com
en iyi casino sitesi [url=https://casibom1st.shop/#]casibom mobil giris[/url] casino slot siteleri casibom1st.shop
https://sweetbonanza1st.shop/# sweet bonanza slot
casinonaxi: casino siteleri 2025 – rcasino casinositeleri1st.com
sweet bonanza 1st: sweet bonanza 1st – sweet bonanza 1st sweetbonanza1st.shop
sweet bonanza oyna: sweet bonanza giris – sweet bonanza demo sweetbonanza1st.shop
deneme bonusu veren siteler: casino siteleri – deneme bonusu veren siteler casinositeleri1st.com
deneme bonusu veren yeni siteler 2025 [url=http://casibom1st.com/#]casibom resmi[/url] en iyi yasal bahis siteleri casibom1st.shop
http://usmexpharm.com/# mexican rx online
mexican pharmacy: USMexPharm – certified Mexican pharmacy
USMexPharm: usa mexico pharmacy – UsMex Pharm
Us Mex Pharm: mexican pharmacy – usa mexico pharmacy
https://usmexpharm.shop/# USMexPharm
Mexican pharmacy ship to USA: Mexican pharmacy ship to USA – USMexPharm
Mexican pharmacy ship to USA [url=https://usmexpharm.com/#]UsMex Pharm[/url] mexican mail order pharmacies
USMexPharm: usa mexico pharmacy – certified Mexican pharmacy
best online pharmacies in mexico: certified Mexican pharmacy – Mexican pharmacy ship to USA
certified Mexican pharmacy: Mexican pharmacy ship to USA – Us Mex Pharm
https://usmexpharm.com/# certified Mexican pharmacy
USMexPharm: certified Mexican pharmacy – certified Mexican pharmacy
mexico drug stores pharmacies: Us Mex Pharm – mexican border pharmacies shipping to usa
Us Mex Pharm [url=https://usmexpharm.shop/#]usa mexico pharmacy[/url] USMexPharm
certified Mexican pharmacy: Us Mex Pharm – Us Mex Pharm
https://usmexpharm.com/# Mexican pharmacy ship to USA
usa mexico pharmacy: USMexPharm – Mexican pharmacy ship to USA
п»їbest mexican online pharmacies: mexican pharmacy – mexican pharmacy
Us Mex Pharm: usa mexico pharmacy – usa mexico pharmacy
https://usmexpharm.shop/# certified Mexican pharmacy
mexican online pharmacies prescription drugs: Us Mex Pharm – buying from online mexican pharmacy
usa mexico pharmacy [url=https://usmexpharm.com/#]certified Mexican pharmacy[/url] Mexican pharmacy ship to USA
mexican border pharmacies shipping to usa: Us Mex Pharm – certified Mexican pharmacy
Mexican pharmacy ship to USA: Mexican pharmacy ship to USA – certified Mexican pharmacy
https://usmexpharm.com/# mexican pharmacy
Mexican pharmacy ship to USA: Us Mex Pharm – Mexican pharmacy ship to USA
usa mexico pharmacy: usa mexico pharmacy – mexican pharmacy
certified Mexican pharmacy: USMexPharm – Mexican pharmacy ship to USA
https://usmexpharm.com/# usa mexico pharmacy
mexican pharmacy [url=https://usmexpharm.com/#]usa mexico pharmacy[/url] purple pharmacy mexico price list
reputable mexican pharmacies online: usa mexico pharmacy – Mexican pharmacy ship to USA
Us Mex Pharm: usa mexico pharmacy – mexican mail order pharmacies
UsMex Pharm: UsMex Pharm – Mexican pharmacy ship to USA
http://usmexpharm.com/# Mexican pharmacy ship to USA
USA India Pharm: USA India Pharm – cheapest online pharmacy india
best india pharmacy: indianpharmacy com – india online pharmacy
UsaIndiaPharm: UsaIndiaPharm – USA India Pharm
online shopping pharmacy india [url=http://usaindiapharm.com/#]п»їlegitimate online pharmacies india[/url] USA India Pharm
http://usaindiapharm.com/# USA India Pharm
Online medicine home delivery: top 10 online pharmacy in india – india pharmacy mail order
Online medicine home delivery: online shopping pharmacy india – USA India Pharm
USA India Pharm: USA India Pharm – Online medicine home delivery
https://usaindiapharm.shop/# UsaIndiaPharm
USA India Pharm: UsaIndiaPharm – UsaIndiaPharm
USA India Pharm [url=https://usaindiapharm.shop/#]UsaIndiaPharm[/url] UsaIndiaPharm
UsaIndiaPharm: top online pharmacy india – UsaIndiaPharm
Online medicine home delivery: USA India Pharm – UsaIndiaPharm
best india pharmacy: UsaIndiaPharm – UsaIndiaPharm
https://usaindiapharm.shop/# top online pharmacy india
USA India Pharm: indianpharmacy com – indian pharmacy online
п»їlegitimate online pharmacies india: UsaIndiaPharm – USA India Pharm
UsaIndiaPharm: UsaIndiaPharm – indian pharmacy online
https://usaindiapharm.shop/# USA India Pharm
indian pharmacies safe [url=https://usaindiapharm.shop/#]indianpharmacy com[/url] UsaIndiaPharm
Online medicine order: UsaIndiaPharm – UsaIndiaPharm
UsaIndiaPharm: buy prescription drugs from india – UsaIndiaPharm
best india pharmacy: indian pharmacy online – indian pharmacy
top online pharmacy india [url=http://usaindiapharm.com/#]USA India Pharm[/url] UsaIndiaPharm
india online pharmacy: UsaIndiaPharm – USA India Pharm
USA India Pharm: world pharmacy india – USA India Pharm
online pharmacy india: USA India Pharm – UsaIndiaPharm
mail order pharmacy india: USA India Pharm – india pharmacy
https://usaindiapharm.com/# india pharmacy
UsaIndiaPharm: cheapest online pharmacy india – UsaIndiaPharm
UsaIndiaPharm [url=https://usaindiapharm.com/#]UsaIndiaPharm[/url] UsaIndiaPharm
USA India Pharm: buy prescription drugs from india – п»їlegitimate online pharmacies india
UsaIndiaPharm: best india pharmacy – indian pharmacy online
http://usaindiapharm.com/# mail order pharmacy india
indian pharmacies safe: USA India Pharm – UsaIndiaPharm
buy medicines online in india: UsaIndiaPharm – indian pharmacies safe
https://usaindiapharm.com/# top 10 pharmacies in india
top 10 pharmacies in india [url=https://usaindiapharm.shop/#]UsaIndiaPharm[/url] top 10 pharmacies in india
online shopping pharmacy india: top online pharmacy india – UsaIndiaPharm
online pharmacy india: USA India Pharm – UsaIndiaPharm
best online pharmacy india: USA India Pharm – USA India Pharm
mail order pharmacy india: п»їlegitimate online pharmacies india – UsaIndiaPharm
http://usaindiapharm.com/# cheapest online pharmacy india
UsaIndiaPharm: USA India Pharm – cheapest online pharmacy india
UsaIndiaPharm: mail order pharmacy india – UsaIndiaPharm
reputable indian pharmacies [url=http://usaindiapharm.com/#]online shopping pharmacy india[/url] Online medicine order
http://usaindiapharm.com/# UsaIndiaPharm
UsaIndiaPharm: USA India Pharm – UsaIndiaPharm
canada pharmacy online: usa canada pharm – usa canada pharm
USACanadaPharm [url=http://usacanadapharm.com/#]usa canada pharm[/url] canadian pharmacy online reviews
http://usacanadapharm.com/# rate canadian pharmacies
canadian pharmacy no scripts: legitimate canadian pharmacy online – best rated canadian pharmacy
USACanadaPharm: usa canada pharm – usa canada pharm
https://usacanadapharm.com/# reliable canadian pharmacy reviews
canadian pharmacy prices: USACanadaPharm – USACanadaPharm
usa canada pharm: usa canada pharm – best canadian pharmacy to order from
online canadian pharmacy reviews [url=https://usacanadapharm.com/#]usa canada pharm[/url] USACanadaPharm
USACanadaPharm: USACanadaPharm – usa canada pharm
http://usacanadapharm.com/# canada pharmacy online
pet meds without vet prescription canada: canadian pharmacy near me – best canadian online pharmacy
USACanadaPharm: canadian online pharmacy – USACanadaPharm
usa canada pharm: canadian pharmacy meds – canadian pharmacy online
https://usacanadapharm.com/# USACanadaPharm
usa canada pharm [url=https://usacanadapharm.com/#]reliable canadian online pharmacy[/url] canada pharmacy online
USACanadaPharm: usa canada pharm – canadian pharmacy store
usa canada pharm: canadian pharmacy review – USACanadaPharm
reliable canadian pharmacy reviews: canadian drugs online – usa canada pharm
https://usacanadapharm.com/# northern pharmacy canada
northwest pharmacy canada: safe canadian pharmacy – usa canada pharm
canadian pharmacy ed medications: USACanadaPharm – USACanadaPharm
usa canada pharm [url=http://usacanadapharm.com/#]USACanadaPharm[/url] usa canada pharm
https://usacanadapharm.shop/# usa canada pharm
usa canada pharm: usa canada pharm – my canadian pharmacy
canadian mail order pharmacy: ed meds online canada – reddit canadian pharmacy
https://usacanadapharm.shop/# canadian pharmacy price checker
reputable canadian online pharmacies: canadian pharmacy drugs online – usa canada pharm
canadian pharmacies comparison https://usacanadapharm.com/# best canadian pharmacy online
reliable canadian pharmacy
canadian family pharmacy [url=https://usacanadapharm.shop/#]USACanadaPharm[/url] canadian online pharmacy reviews
usa canada pharm: online canadian pharmacy – usa canada pharm
http://usacanadapharm.com/# usa canada pharm
usa canada pharm: USACanadaPharm – USACanadaPharm
usa canada pharm: cheap canadian pharmacy online – canadian pharmacy near me
https://usacanadapharm.com/# canadian pharmacy 365
canadian pharmacy ed medications: USACanadaPharm – buy prescription drugs from canada cheap
canadian pharmacy tampa [url=https://usacanadapharm.shop/#]canadianpharmacymeds[/url] USACanadaPharm
usa canada pharm: USACanadaPharm – USACanadaPharm
http://usacanadapharm.com/# usa canada pharm
online pharmacy canada: USACanadaPharm – pharmacy com canada
USACanadaPharm: best canadian pharmacy to buy from – canadian pharmacy antibiotics
canadian pharmacies comparison [url=https://usacanadapharm.com/#]canadian pharmacy meds[/url] usa canada pharm
https://olympecasino.pro/# olympe casino
olympe: olympe casino cresus – olympe casino
olympe casino: olympe – olympe casino cresus
https://olympecasino.pro/# olympe casino en ligne
olympe casino: olympe casino cresus – casino olympe
casino olympe: olympe casino – casino olympe
olympe: olympe casino en ligne – olympe casino cresus
olympe casino avis: olympe casino en ligne – olympe casino cresus
olympe casino avis: olympe – olympe casino
[url=https://olympecasino.pro/#]olympe[/url] olympe
casino olympe: olympe casino – olympe casino avis
[url=https://olympecasino.pro/#]olympe casino[/url] olympe casino avis
olympe casino cresus: olympe – olympe casino en ligne
[url=https://olympecasino.pro/#]olympe[/url] olympe casino avis
casino olympe: olympe casino – olympe casino en ligne
olympe casino cresus: casino olympe – olympe casino cresus
olympe casino en ligne: olympe casino – olympe casino avis
[url=https://olympecasino.pro/#]olympe casino avis[/url] casino olympe
olympe casino: casino olympe – olympe casino
[url=https://olympecasino.pro/#]olympe casino cresus[/url] casino olympe
casino olympe: olympe casino cresus – olympe casino en ligne
[url=https://olympecasino.pro/#]olympe casino[/url] olympe casino cresus
olympe: olympe – olympe casino cresus
olympe casino cresus: olympe casino – olympe casino en ligne
olympe casino cresus: olympe casino en ligne – olympe casino avis
https://olympecasino.pro/# olympe casino avis
olympe casino en ligne: olympe casino – olympe casino en ligne
olympe casino avis: olympe casino cresus – olympe casino avis
olympe: olympe casino cresus – casino olympe
olympe: olympe casino cresus – olympe casino cresus
olympe casino en ligne: olympe casino avis – olympe casino
[url=https://olympecasino.pro/#]olympe casino cresus[/url] olympe casino
olympe casino en ligne: olympe casino en ligne – olympe
[url=https://olympecasino.pro/#]olympe casino cresus[/url] olympe casino avis
olympe casino: olympe – olympe casino avis
[url=https://olympecasino.pro/#]olympe casino cresus[/url] olympe casino cresus
casino olympe: olympe – olympe casino cresus
olympe casino en ligne: olympe casino – casino olympe
[url=https://olympecasino.pro/#]olympe casino avis[/url] olympe casino
casino olympe: olympe casino en ligne – olympe casino cresus
п»їpharmacie en ligne france: Meilleure pharmacie en ligne – Pharmacie sans ordonnance pharmafst.com
kamagra gel: kamagra 100mg prix – kamagra 100mg prix
http://pharmafst.com/# pharmacie en ligne france livraison belgique
Tadalafil achat en ligne [url=https://tadalmed.shop/#]Acheter Viagra Cialis sans ordonnance[/url] Tadalafil sans ordonnance en ligne tadalmed.com
Kamagra pharmacie en ligne: Kamagra Commander maintenant – kamagra en ligne
pharmacie en ligne pas cher: Medicaments en ligne livres en 24h – pharmacie en ligne france fiable pharmafst.com
http://kamagraprix.com/# Kamagra pharmacie en ligne
Achat mГ©dicament en ligne fiable: pharmacie en ligne pas cher – trouver un mГ©dicament en pharmacie pharmafst.com
Kamagra pharmacie en ligne: Achetez vos kamagra medicaments – acheter kamagra site fiable
kamagra 100mg prix: Kamagra pharmacie en ligne – kamagra oral jelly
http://tadalmed.com/# Tadalafil achat en ligne
pharmacie en ligne pas cher [url=http://pharmafst.com/#]pharmacie en ligne france fiable[/url] pharmacie en ligne avec ordonnance pharmafst.shop
acheter mГ©dicament en ligne sans ordonnance: pharmacie en ligne sans ordonnance – pharmacie en ligne fiable pharmafst.com
http://kamagraprix.com/# Achetez vos kamagra medicaments
Acheter Cialis: Tadalafil achat en ligne – Tadalafil 20 mg prix sans ordonnance tadalmed.shop
pharmacie en ligne sans ordonnance [url=https://pharmafst.com/#]pharmacie en ligne pas cher[/url] pharmacie en ligne livraison europe pharmafst.shop
pharmacie en ligne france livraison internationale: pharmacie en ligne – vente de mГ©dicament en ligne pharmafst.com
https://kamagraprix.shop/# kamagra oral jelly
kamagra en ligne: kamagra livraison 24h – kamagra 100mg prix
pharmacie en ligne france livraison internationale [url=http://pharmafst.com/#]Livraison rapide[/url] п»їpharmacie en ligne france pharmafst.shop
Achat Cialis en ligne fiable: Acheter Cialis 20 mg pas cher – cialis generique tadalmed.shop
http://tadalmed.com/# cialis generique
Kamagra pharmacie en ligne: kamagra oral jelly – kamagra pas cher
Cialis generique prix [url=http://tadalmed.com/#]Acheter Cialis[/url] Acheter Cialis 20 mg pas cher tadalmed.com
Cialis sans ordonnance 24h: Acheter Cialis 20 mg pas cher – cialis prix tadalmed.shop
pharmacie en ligne avec ordonnance [url=https://pharmafst.shop/#]pharmacie en ligne pas cher[/url] pharmacie en ligne fiable pharmafst.shop
cialis prix: Cialis en ligne – Acheter Cialis tadalmed.shop
https://tadalmed.com/# cialis sans ordonnance
Achat mГ©dicament en ligne fiable: pharmacie en ligne pas cher – pharmacie en ligne france livraison internationale pharmafst.com
Pharmacie sans ordonnance: pharmacie en ligne sans ordonnance – trouver un mГ©dicament en pharmacie pharmafst.com
https://pharmafst.com/# pharmacie en ligne fiable
https://kamagraprix.shop/# achat kamagra
Cialis en ligne: Tadalafil 20 mg prix sans ordonnance – Acheter Cialis tadalmed.shop
Tadalafil achat en ligne: Achat Cialis en ligne fiable – Acheter Viagra Cialis sans ordonnance tadalmed.shop
п»їpharmacie en ligne france: pharmacie en ligne sans ordonnance – п»їpharmacie en ligne france pharmafst.com
pharmacie en ligne france livraison internationale: Pharmacies en ligne certifiees – Pharmacie sans ordonnance pharmafst.com
https://pharmafst.shop/# pharmacie en ligne france fiable
Cialis en ligne: cialis prix – Tadalafil sans ordonnance en ligne tadalmed.shop
Acheter Cialis 20 mg pas cher [url=https://tadalmed.com/#]Acheter Cialis 20 mg pas cher[/url] cialis sans ordonnance tadalmed.com
Acheter Cialis 20 mg pas cher: Acheter Viagra Cialis sans ordonnance – Acheter Cialis 20 mg pas cher tadalmed.shop
Tadalafil achat en ligne: Cialis en ligne – Tadalafil achat en ligne tadalmed.shop
https://kamagraprix.shop/# kamagra oral jelly
vente de mГ©dicament en ligne: Livraison rapide – trouver un mГ©dicament en pharmacie pharmafst.com
acheter mГ©dicament en ligne sans ordonnance: Pharmacies en ligne certifiees – pharmacie en ligne france livraison internationale pharmafst.com
pharmacie en ligne france fiable: pharmacie en ligne pas cher – pharmacie en ligne france pas cher pharmafst.com
https://tadalmed.com/# cialis prix
Tadalafil 20 mg prix sans ordonnance: Tadalafil achat en ligne – Cialis sans ordonnance 24h tadalmed.shop
pharmacie en ligne france fiable: pharmacie en ligne pas cher – pharmacie en ligne livraison europe pharmafst.com
kamagra 100mg prix: kamagra pas cher – kamagra 100mg prix
kamagra livraison 24h: kamagra en ligne – kamagra 100mg prix
http://tadalmed.com/# Tadalafil achat en ligne
Cialis sans ordonnance 24h: Acheter Cialis – cialis sans ordonnance tadalmed.shop
Kamagra pharmacie en ligne [url=https://kamagraprix.shop/#]kamagra gel[/url] kamagra pas cher
Tadalafil 20 mg prix sans ordonnance: Tadalafil 20 mg prix sans ordonnance – Cialis sans ordonnance 24h tadalmed.shop
kamagra pas cher: Acheter Kamagra site fiable – achat kamagra
https://kamagraprix.com/# Kamagra pharmacie en ligne
Pharmacie en ligne Cialis sans ordonnance: cialis sans ordonnance – cialis generique tadalmed.shop
Pharmacie sans ordonnance: pharmacie en ligne – pharmacie en ligne fiable pharmafst.com
https://pharmafst.com/# pharmacie en ligne france livraison belgique
Acheter Cialis 20 mg pas cher: Tadalafil achat en ligne – Cialis en ligne tadalmed.shop
Tadalafil sans ordonnance en ligne: Cialis sans ordonnance 24h – Cialis sans ordonnance pas cher tadalmed.shop
kamagra livraison 24h: Kamagra pharmacie en ligne – Kamagra pharmacie en ligne
Acheter Cialis 20 mg pas cher [url=https://tadalmed.com/#]Cialis generique prix[/url] cialis generique tadalmed.com
http://pharmafst.com/# п»їpharmacie en ligne france
Acheter Kamagra site fiable: kamagra pas cher – Kamagra Commander maintenant
kamagra gel: kamagra oral jelly – kamagra pas cher
Achetez vos kamagra medicaments: kamagra oral jelly – acheter kamagra site fiable
Achetez vos kamagra medicaments [url=https://kamagraprix.shop/#]kamagra oral jelly[/url] kamagra en ligne
https://kamagraprix.com/# Kamagra pharmacie en ligne
kamagra livraison 24h: Acheter Kamagra site fiable – Achetez vos kamagra medicaments
Acheter Kamagra site fiable: achat kamagra – kamagra livraison 24h
Tadalafil 20 mg prix sans ordonnance: Acheter Cialis 20 mg pas cher – Cialis generique prix tadalmed.shop
Acheter Kamagra site fiable: kamagra 100mg prix – kamagra gel
https://kamagraprix.com/# kamagra 100mg prix
acheter mГ©dicament en ligne sans ordonnance: Meilleure pharmacie en ligne – Pharmacie en ligne livraison Europe pharmafst.com
http://kamagraprix.com/# kamagra 100mg prix
acheter kamagra site fiable: Kamagra Commander maintenant – kamagra livraison 24h
http://kamagraprix.com/# achat kamagra
kamagra livraison 24h: kamagra pas cher – kamagra gel
https://tadalmed.shop/# Tadalafil achat en ligne
pharmacie en ligne pas cher: Medicaments en ligne livres en 24h – pharmacie en ligne france fiable pharmafst.com
kamagra gel: acheter kamagra site fiable – kamagra en ligne
Achat mГ©dicament en ligne fiable [url=http://pharmafst.com/#]pharmacie en ligne sans ordonnance[/url] pharmacie en ligne france fiable pharmafst.shop
kamagra livraison 24h: kamagra livraison 24h – Kamagra pharmacie en ligne
https://pharmafst.shop/# Achat mГ©dicament en ligne fiable
acheter kamagra site fiable: Achetez vos kamagra medicaments – kamagra en ligne
Pharmacie en ligne livraison Europe: п»їpharmacie en ligne france – Achat mГ©dicament en ligne fiable pharmafst.com
cialis generique: Cialis sans ordonnance 24h – Acheter Cialis 20 mg pas cher tadalmed.shop
https://pharmafst.shop/# trouver un mГ©dicament en pharmacie
Medicine From India: MedicineFromIndia – MedicineFromIndia
mexican online pharmacy: mexico pharmacies prescription drugs – Rx Express Mexico
MedicineFromIndia: Medicine From India – indian pharmacy
buy medicines online in india: Medicine From India – indian pharmacy online shopping
http://rxexpressmexico.com/# mexico pharmacy order online
mexico pharmacy order online: mexico pharmacies prescription drugs – Rx Express Mexico
buying prescription drugs in mexico online: mexican rx online – Rx Express Mexico
mexico pharmacies prescription drugs: RxExpressMexico – mexican rx online
RxExpressMexico [url=https://rxexpressmexico.com/#]mexico pharmacies prescription drugs[/url] RxExpressMexico
https://expressrxcanada.com/# canadian pharmacy no rx needed
canadian pharmacy mall: Generic drugs from Canada – canadian pharmacy
canadian pharmacy 365: Express Rx Canada – canadian pharmacy 24h com
Medicine From India: indian pharmacy online shopping – indian pharmacy
MedicineFromIndia: medicine courier from India to USA – MedicineFromIndia
https://medicinefromindia.com/# MedicineFromIndia
mexico drug stores pharmacies [url=http://rxexpressmexico.com/#]Rx Express Mexico[/url] Rx Express Mexico
reliable canadian pharmacy: Express Rx Canada – reputable canadian online pharmacy
my canadian pharmacy review: Express Rx Canada – canadian king pharmacy
http://medicinefromindia.com/# MedicineFromIndia
online canadian drugstore [url=https://expressrxcanada.shop/#]ExpressRxCanada[/url] canadian king pharmacy
indian pharmacy online: MedicineFromIndia – indian pharmacy online shopping
my canadian pharmacy: Buy medicine from Canada – prescription drugs canada buy online
indian pharmacy online shopping: Medicine From India – MedicineFromIndia
https://medicinefromindia.shop/# indian pharmacy online
canada drugs [url=https://expressrxcanada.com/#]ExpressRxCanada[/url] canadian pharmacy price checker
mexico pharmacy order online: mexican online pharmacy – mexico drug stores pharmacies
MedicineFromIndia: Medicine From India – MedicineFromIndia
medicine courier from India to USA: reputable indian pharmacies – indian pharmacy online
https://expressrxcanada.shop/# canadianpharmacy com
pharmacies in mexico that ship to usa: Rx Express Mexico – buying from online mexican pharmacy
mexican online pharmacy: mexico drug stores pharmacies – mexican rx online
http://expressrxcanada.com/# canada drugs online reviews
Rx Express Mexico: mexican rx online – mexican rx online
canadian pharmacy meds reviews: ExpressRxCanada – canada pharmacy
http://rxexpressmexico.com/# mexico pharmacy order online
canadian pharmacy oxycodone: Express Rx Canada – canadian valley pharmacy
вавада официальный сайт: vavada – vavada вход
pin-up: pin up az – pinup az
pin up az: pin up – pin up
https://pinupaz.top/# pinup az
pin up вход: пин ап вход – пин ап вход
http://vavadavhod.tech/# вавада
pinup az: pinup az – pin up az
pin-up casino giris [url=http://pinupaz.top/#]pin up casino[/url] pin-up casino giris
вавада: vavada – vavada вход
pin up az: pin up casino – pin up
http://pinuprus.pro/# пинап казино
вавада зеркало [url=http://vavadavhod.tech/#]вавада казино[/url] вавада
пин ап зеркало: пин ап вход – пин ап казино официальный сайт
pinup az: pin up – pin up az
https://pinupaz.top/# pin up casino
pin-up casino giris [url=https://pinupaz.top/#]pin up azerbaycan[/url] pin-up casino giris
pin up az: pin up casino – pin up
пинап казино: пинап казино – пин ап вход
http://vavadavhod.tech/# вавада зеркало
vavada: вавада зеркало – vavada вход
pin up: pinup az – pin up
вавада зеркало [url=https://vavadavhod.tech/#]vavada[/url] вавада зеркало
https://pinupaz.top/# pin up azerbaycan
маркетплейс аккаунтов покупка аккаунтов
vavada вход: вавада казино – vavada вход
купить аккаунт с прокачкой маркетплейс аккаунтов
пин ап казино [url=http://pinuprus.pro/#]пин ап казино[/url] пин ап зеркало
магазин аккаунтов https://magazin-akkauntov-online.ru/
https://pinuprus.pro/# пин ап казино официальный сайт
биржа аккаунтов https://ploshadka-prodazha-akkauntov.ru/
пинап казино: пин ап казино – пинап казино
пин ап вход: пинап казино – пин ап вход
https://vavadavhod.tech/# вавада казино
pin up: pin up casino – pin up casino
пин ап казино официальный сайт: пин ап казино официальный сайт – pin up вход
вавада официальный сайт: вавада официальный сайт – вавада
маркетплейс аккаунтов соцсетей https://prodat-akkaunt-online.ru/
площадка для продажи аккаунтов платформа для покупки аккаунтов
vavada casino [url=http://vavadavhod.tech/#]vavada[/url] vavada
перепродажа аккаунтов купить аккаунт
https://pinupaz.top/# pin-up
пинап казино: пин ап казино – пин ап казино официальный сайт
vavada: вавада – vavada вход
пин ап казино официальный сайт: пин ап казино – пин ап зеркало
https://vavadavhod.tech/# вавада зеркало
pin-up casino giris: pin up azerbaycan – pin up
пин ап казино: пин ап зеркало – пинап казино
http://vavadavhod.tech/# вавада зеркало
пин ап зеркало [url=https://pinuprus.pro/#]пин ап казино официальный сайт[/url] pin up вход
пин ап зеркало: пин ап казино – пин ап вход
pinup az: pin up azerbaycan – pin up
http://pinupaz.top/# pin-up
pin up вход: пин ап казино – pin up вход
vavada вход [url=https://vavadavhod.tech/#]вавада официальный сайт[/url] вавада зеркало
вавада зеркало: vavada вход – вавада казино
vavada: vavada – вавада зеркало
Social media account marketplace Marketplace for Ready-Made Accounts
Account Trading Service accountsmarketplacepro.com
Account Trading Website for Buying Accounts
http://vavadavhod.tech/# вавада официальный сайт
Profitable Account Sales buyaccountsmarketplace.com
pin-up [url=https://pinupaz.top/#]pin-up casino giris[/url] pin up casino
vavada: вавада казино – vavada
пин ап казино официальный сайт: пин ап казино – pin up вход
https://pinupaz.top/# pin-up casino giris
vavada вход: vavada – вавада
pinup az [url=https://pinupaz.top/#]pin up azerbaycan[/url] pin up az
naturally like your web site however you need to take a look at the spelling on several of your posts. A number of them are rife with spelling problems and I find it very bothersome to tell the truth on the other hand I will surely come again again.
pin-up casino giris: pinup az – pin up az
http://pinupaz.top/# pin up az
пин ап казино: пин ап вход – пин ап вход
пинап казино [url=https://pinuprus.pro/#]пин ап казино официальный сайт[/url] пинап казино
пин ап казино: пин ап зеркало – пин ап казино
http://vavadavhod.tech/# вавада зеркало
Account trading platform Account Buying Platform
Account exchange Profitable Account Sales
pin up: pin up azerbaycan – pin up azerbaycan
Account exchange Find Accounts for Sale
пин ап зеркало: pin up вход – пин ап зеркало
Account Market Account Sale
https://pinupaz.top/# pin up casino
pin up вход: пин ап зеркало – пин ап казино
pin up az [url=http://pinupaz.top/#]pin-up casino giris[/url] pin up az
пин ап вход: pin up вход – пин ап зеркало
Account Purchase Account Trading Service
Website for Buying Accounts Account exchange
Online Account Store Account Market
пинап казино [url=https://pinuprus.pro/#]пин ап казино[/url] пин ап казино официальный сайт
http://pinuprus.pro/# пин ап зеркало
pin-up casino giris: pinup az – pinup az
вавада: vavada вход – vavada вход
вавада зеркало [url=https://vavadavhod.tech/#]вавада[/url] вавада официальный сайт
пин ап вход: пин ап вход – пин ап казино официальный сайт
pin-up: pin-up – pin up casino
pin-up casino giris [url=https://pinupaz.top/#]pin up casino[/url] pinup az
pin-up casino giris: pin up casino – pinup az
database of accounts for sale find accounts for sale
purchase ready-made accounts social media account marketplace
https://pinupaz.top/# pin up casino
secure account purchasing platform account trading platform
pinup az: pin up casino – pinup az
pin up вход [url=https://pinuprus.pro/#]пин ап зеркало[/url] пин ап казино официальный сайт
secure account sales https://buyaccountsdiscount.com
http://pinupaz.top/# pin up
пин ап вход: пин ап зеркало – пин ап казино
пин ап зеркало [url=https://pinuprus.pro/#]пин ап вход[/url] pin up вход
pin up casino: pinup az – pin up
http://pinupaz.top/# pin up az
вавада зеркало: вавада казино – vavada вход
pin up casino: pin up casino – pin up az
http://vavadavhod.tech/# вавада казино
vavada: вавада – вавада официальный сайт
account marketplace accounts marketplace
account market account exchange service
account trading platform secure account sales
http://vavadavhod.tech/# вавада
пин ап вход: пинап казино – пин ап казино официальный сайт
account marketplace account store
pin up casino [url=https://pinupaz.top/#]pin up azerbaycan[/url] pin up az
https://vavadavhod.tech/# vavada
пинап казино: пин ап вход – пин ап зеркало
вавада: вавада официальный сайт – вавада
sell accounts account buying service
account trading platform guaranteed accounts
pinup az [url=https://pinupaz.top/#]pin-up casino giris[/url] pin up az
account exchange account trading platform
vavada casino: vavada – vavada вход
http://pinupaz.top/# pinup az
pin up: pin up casino – pin up az
pinup az [url=https://pinupaz.top/#]pinup az[/url] pin up
pin up: pin up – pin up azerbaycan
http://pinupaz.top/# pin-up
вавада официальный сайт: vavada – вавада казино
account trading platform account buying service
pin up azerbaycan: pin-up – pinup az
пин ап зеркало [url=https://pinuprus.pro/#]пин ап вход[/url] пин ап казино официальный сайт
https://vavadavhod.tech/# вавада казино
website for buying accounts account marketplace
guaranteed accounts social-accounts.org
buy pre-made account buy account
вавада официальный сайт: вавада официальный сайт – vavada вход
вавада официальный сайт: vavada вход – вавада
вавада официальный сайт: vavada casino – vavada вход
account exchange service marketplace for ready-made accounts
guaranteed accounts website for buying accounts
pin up вход: пинап казино – пин ап зеркало
https://pinuprus.pro/# пинап казино
вавада официальный сайт: vavada – вавада казино
пин ап казино: пин ап вход – пинап казино
http://vavadavhod.tech/# vavada casino
vavada: vavada – вавада официальный сайт
buy and sell accounts https://best-social-accounts.org
account exchange account catalog
guaranteed accounts accounts marketplace
http://vavadavhod.tech/# vavada вход
pin-up: pin up az – pin-up
вавада официальный сайт [url=https://vavadavhod.tech/#]vavada casino[/url] vavada casino
vavada: vavada вход – вавада официальный сайт
account catalog purchase ready-made accounts
http://pinuprus.pro/# пин ап вход
вавада казино: вавада официальный сайт – vavada casino
пин ап вход: пин ап вход – pin up вход
database of accounts for sale buy and sell accounts
secure account purchasing platform secure account purchasing platform
account catalog account exchange service
вавада: вавада – вавада официальный сайт
пин ап казино официальный сайт [url=https://pinuprus.pro/#]пин ап казино официальный сайт[/url] пинап казино
http://vavadavhod.tech/# вавада казино
pin-up casino giris: pin up azerbaycan – pin up az
пин ап вход [url=https://pinuprus.pro/#]пин ап казино официальный сайт[/url] пин ап казино
buy pre-made account purchase ready-made accounts
http://pinupaz.top/# pin-up
pin up casino: pin-up casino giris – pin up az
online account store buy accounts
account trading account selling service
accounts market gaming account marketplace
vavada: вавада – вавада казино
vavada вход: vavada casino – vavada casino
https://pinupaz.top/# pin-up
https://zipgenericmd.shop/# reliable online pharmacy Cialis
secure checkout ED drugs: Cialis without prescription – discreet shipping ED pills
fast Viagra delivery: secure checkout Viagra – secure checkout Viagra
https://modafinilmd.store/# Modafinil for sale
same-day Viagra shipping: discreet shipping – discreet shipping
social media account marketplace buy accounts
account market https://accounts-marketplace.xyz
profitable account sales https://buy-best-accounts.org
secure checkout ED drugs: generic tadalafil – discreet shipping ED pills
https://modafinilmd.store/# purchase Modafinil without prescription
website for selling accounts https://social-accounts-marketplaces.live/
legal Modafinil purchase: safe modafinil purchase – Modafinil for sale
purchase Modafinil without prescription: Modafinil for sale – purchase Modafinil without prescription
https://modafinilmd.store/# purchase Modafinil without prescription
account sale https://accounts-marketplace.live
account market https://social-accounts-marketplace.xyz/
buy generic Viagra online: buy generic Viagra online – cheap Viagra online
gaming account marketplace https://buy-accounts.space/
same-day Viagra shipping: discreet shipping – generic sildenafil 100mg
http://modafinilmd.store/# Modafinil for sale
online Cialis pharmacy: online Cialis pharmacy – affordable ED medication
legal Modafinil purchase: Modafinil for sale – buy modafinil online
discreet shipping [url=https://maxviagramd.shop/#]safe online pharmacy[/url] buy generic Viagra online
buy generic Cialis online: Cialis without prescription – online Cialis pharmacy
account purchase https://buy-accounts-shop.pro
https://zipgenericmd.shop/# online Cialis pharmacy
generic sildenafil 100mg: secure checkout Viagra – generic sildenafil 100mg
generic sildenafil 100mg [url=https://maxviagramd.com/#]generic sildenafil 100mg[/url] best price for Viagra
account market https://social-accounts-marketplace.live
buy accounts https://buy-accounts.live
safe modafinil purchase: modafinil legality – doctor-reviewed advice
account selling service account market
http://zipgenericmd.com/# buy generic Cialis online
doctor-reviewed advice: modafinil pharmacy – doctor-reviewed advice
discreet shipping ED pills [url=https://zipgenericmd.shop/#]affordable ED medication[/url] discreet shipping ED pills
order Cialis online no prescription: best price Cialis tablets – reliable online pharmacy Cialis
verified Modafinil vendors: safe modafinil purchase – buy modafinil online
buy modafinil online [url=https://modafinilmd.store/#]purchase Modafinil without prescription[/url] verified Modafinil vendors
doctor-reviewed advice: modafinil legality – modafinil 2025
http://modafinilmd.store/# modafinil 2025
trusted Viagra suppliers: fast Viagra delivery – cheap Viagra online
buy modafinil online: modafinil legality – verified Modafinil vendors
order Viagra discreetly [url=https://maxviagramd.com/#]safe online pharmacy[/url] trusted Viagra suppliers
https://zipgenericmd.shop/# FDA approved generic Cialis
generic tadalafil: FDA approved generic Cialis – discreet shipping ED pills
generic tadalafil: FDA approved generic Cialis – affordable ED medication
buy accounts accounts-marketplace-best.pro
buy generic Viagra online: buy generic Viagra online – discreet shipping
reliable online pharmacy Cialis [url=https://zipgenericmd.shop/#]cheap Cialis online[/url] discreet shipping ED pills
verified Modafinil vendors: doctor-reviewed advice – doctor-reviewed advice
best price Cialis tablets [url=https://zipgenericmd.com/#]best price Cialis tablets[/url] buy generic Cialis online
магазин аккаунтов akkaunty-na-prodazhu.pro
магазин аккаунтов https://rynok-akkauntov.top/
https://maxviagramd.com/# best price for Viagra
покупка аккаунтов https://kupit-akkaunt.xyz/
Cialis without prescription: best price Cialis tablets – cheap Cialis online
amoxicillin 750 mg price [url=https://amohealthcare.store/#]Amo Health Care[/url] where to get amoxicillin over the counter
prednisone 10 mg: prednisone 200 mg tablets – prednisone 1 mg for sale
https://prednihealth.shop/# can you buy prednisone without a prescription
order amoxicillin no prescription: amoxicillin without a prescription – Amo Health Care
PredniHealth [url=http://prednihealth.com/#]PredniHealth[/url] buy 40 mg prednisone
can i buy cheap clomid: where can i get generic clomid without a prescription – can i purchase generic clomid online
https://amohealthcare.store/# buy amoxicillin online uk
PredniHealth: prednisone prices – can you buy prednisone over the counter uk
prednisone 10mg tablets: 50 mg prednisone from canada – how much is prednisone 10mg
маркетплейс аккаунтов соцсетей akkaunt-magazin.online
купить аккаунт akkaunty-market.live
Amo Health Care: Amo Health Care – ampicillin amoxicillin
продажа аккаунтов https://kupit-akkaunty-market.xyz
where can i get cheap clomid without prescription [url=http://clomhealth.com/#]Clom Health[/url] cheap clomid now
http://clomhealth.com/# cost of clomid no prescription
clomid rx: Clom Health – cost of clomid without a prescription
20mg prednisone: PredniHealth – 30mg prednisone
prednisone coupon: india buy prednisone online – buy prednisone tablets online
Amo Health Care [url=https://amohealthcare.store/#]amoxicillin 50 mg tablets[/url] amoxicillin script
http://clomhealth.com/# get generic clomid tablets
where to get cheap clomid without a prescription: Clom Health – where can i buy generic clomid pills
buy amoxicillin canada: amoxicillin 500 mg purchase without prescription – buying amoxicillin in mexico
https://prednihealth.shop/# PredniHealth
amoxicillin 825 mg [url=https://amohealthcare.store/#]Amo Health Care[/url] amoxicillin pharmacy price
prednisone generic cost: PredniHealth – PredniHealth
prednisone 20mg price: PredniHealth – prednisone prescription for sale
http://clomhealth.com/# can i buy clomid no prescription
PredniHealth [url=https://prednihealth.shop/#]PredniHealth[/url] prednisone 5 mg tablet without a prescription
where to buy generic clomid without prescription: get clomid no prescription – can i buy generic clomid without prescription
купить аккаунт akkaunty-optom.live
маркетплейс аккаунтов соцсетей https://online-akkaunty-magazin.xyz/
маркетплейс аккаунтов https://akkaunty-dlya-prodazhi.pro/
where to buy amoxicillin over the counter: generic amoxicillin cost – amoxicillin 500mg no prescription
https://prednihealth.com/# prednisone 1mg purchase
cost of generic clomid tablets: buy generic clomid prices – clomid tablet
Amo Health Care [url=https://amohealthcare.store/#]Amo Health Care[/url] amoxicillin 800 mg price
where can i get cheap clomid without dr prescription: clomid without insurance – can i get cheap clomid prices
https://prednihealth.shop/# generic prednisone 10mg
маркетплейс аккаунтов https://kupit-akkaunt.online/
cheap clomid no prescription: where buy generic clomid without a prescription – how to buy clomid without dr prescription
cialis dapoxetine [url=https://tadalaccess.com/#]buy cialis tadalafil[/url] tadalafil review forum
how long for cialis to take effect: buy cialis usa – tadalafil troche reviews
cialis for pulmonary hypertension: TadalAccess – what happens if you take 2 cialis
https://tadalaccess.com/# tadalafil tablets erectafil 20
price of cialis [url=https://tadalaccess.com/#]what is cialis for[/url] what is cialis used for
take cialis the correct way: TadalAccess – what to do when cialis stops working
п»їwhat can i take to enhance cialis: cialis 5mg 10mg no prescription – tadalafil generic usa
https://tadalaccess.com/# can you drink wine or liquor if you took in tadalafil
cialis street price [url=https://tadalaccess.com/#]buying cialis online safely[/url] buy cialis generic online
cialis overnight deleivery: Tadal Access – cialis dapoxetine europe
purchase generic cialis: cialis for sale in toront ontario – cialis dosage side effects
https://tadalaccess.com/# cialis alternative
what happens if you take 2 cialis: cialis super active plus reviews – cialis lower blood pressure
cialis 80 mg dosage: TadalAccess – cialis 800 black canada
cialis online cheap [url=https://tadalaccess.com/#]cialis 20 mg price walmart[/url] tadalafil price insurance
https://tadalaccess.com/# how well does cialis work
cialis no prescription: TadalAccess – cialis priligy online australia
order cialis no prescription: TadalAccess – cialis prescription online
https://tadalaccess.com/# cialis samples
generic cialis tadalafil 20 mg from india: TadalAccess – side effects of cialis tadalafil
super cialis: cialis canada price – cialis side effects a wife’s perspective
cialis black 800 to buy in the uk one pill [url=https://tadalaccess.com/#]best price for tadalafil[/url] cialis 20 mg price costco
https://tadalaccess.com/# cheap cialis for sale
buy fb ad account facebook ad account buy
cialis 5 mg: Tadal Access – cialis dosage for ed
how many 5mg cialis can i take at once: tadalafil 40 mg with dapoxetine 60 mg – what happens if you take 2 cialis
https://tadalaccess.com/# what is the normal dose of cialis
where can i buy cialis [url=https://tadalaccess.com/#]tadalafil walgreens[/url] buy cheap cialis online with mastercard
cialis ontario no prescription: Tadal Access – prices cialis
pastilla cialis: Tadal Access – cialis tadalafil & dapoxetine
https://tadalaccess.com/# cialis tadalafil cheapest online
over the counter cialis 2017 [url=https://tadalaccess.com/#]when should you take cialis[/url] cialis super active vs regular cialis
brand cialis: cialis tadalafil online paypal – cialis canada sale
buy accounts facebook https://ad-account-buy.top
fb accounts for sale buy facebook old accounts
facebook account buy https://ad-account-for-sale.top
https://tadalaccess.com/# cialis no prescription overnight delivery
generic cialis from india: how to get cialis without doctor – generic cialis from india
cialis not working anymore [url=https://tadalaccess.com/#]tadalafil generic 20 mg ebay[/url] cheap cialis dapoxitine cheap online
what is the normal dose of cialis: Tadal Access – what does cialis cost
https://tadalaccess.com/# ordering tadalafil online
buy facebook profile https://buy-ad-account.click
canadian pharmacy generic cialis: cialis erection – buy cialis in toronto
does tadalafil lower blood pressure: Tadal Access – cialis without a doctor prescription canada
cialis free trial 2018 [url=https://tadalaccess.com/#]tadalafil citrate bodybuilding[/url] cost of cialis for daily use
https://tadalaccess.com/# evolution peptides tadalafil
cialis for ed: uses for cialis – printable cialis coupon
cialis tadalafil 20mg price: TadalAccess – tadalafil brand name
cialis a domicilio new jersey [url=https://tadalaccess.com/#]Tadal Access[/url] cialis dosage 40 mg
https://tadalaccess.com/# when does cialis go off patent
sildenafil vs tadalafil vs vardenafil: cialis drug – tadalafil price insurance
cialis online usa: cialis generic release date – cialis active ingredient
cialis coupon walmart [url=https://tadalaccess.com/#]TadalAccess[/url] cialis sample
buy fb account https://ad-accounts-for-sale.work/
buy aged google ads accounts https://buy-ads-account.top
https://tadalaccess.com/# centurion laboratories tadalafil review
sell google ads account https://buy-ads-accounts.click
cialis san diego: TadalAccess – no prescription female cialis
buy old facebook account for ads buy fb ad account
cialis for sale brand [url=https://tadalaccess.com/#]when does cialis patent expire[/url] where to buy cialis online
https://tadalaccess.com/# tadalafil generic cialis 20mg
buy cialis with dapoxetine in canada: TadalAccess – cialis picture
cialis results: compounded tadalafil troche life span – cialis 10mg reviews
buy google agency account https://ads-account-for-sale.top/
buy account google ads https://ads-account-buy.work
is generic tadalafil as good as cialis [url=https://tadalaccess.com/#]tadalafil (megalis-macleods) reviews[/url] cialis covered by insurance
https://tadalaccess.com/# cialis paypal canada
cialis and blood pressure: Tadal Access – what is cialis taken for
cialis images: cialis online without perscription – what is cialis for
https://tadalaccess.com/# cialis 20 mg duration
when does the cialis patent expire [url=https://tadalaccess.com/#]Tadal Access[/url] buy cialis 20mg
cialis interactions: how to get cialis prescription online – tadalafil buy online canada
buy google ad threshold account https://buy-ads-invoice-account.top
buy google adwords account https://buy-account-ads.work
originalcialis: TadalAccess – average dose of tadalafil
buy google ad threshold account https://buy-ads-agency-account.top
https://tadalaccess.com/# buying cialis without prescription
tadalafil tablets 20 mg global [url=https://tadalaccess.com/#]Tadal Access[/url] cialis generic best price that accepts mastercard
cialis super active real online store: cialis 5mg price walmart – can you purchase tadalafil in the us
google ads account for sale https://sell-ads-account.click/
cialis free sample: TadalAccess – cialis black 800 to buy in the uk one pill
https://tadalaccess.com/# best place to buy tadalafil online
where to buy cialis: generic cialis tadalafil 20 mg from india – tadalafil generic in usa
over the counter cialis walgreens: TadalAccess – when will cialis be over the counter
https://tadalaccess.com/# maximpeptide tadalafil review
buy verified google ads accounts https://ads-agency-account-buy.click
buy cialis no prescription: TadalAccess – cialis doesnt work for me
buy cialis cheap fast delivery [url=https://tadalaccess.com/#]canadian pharmacy online cialis[/url] where to buy cialis
https://tadalaccess.com/# cialis for daily use dosage
free coupon for cialis: Tadal Access – cialis trial
cialis delivery held at customs: tadalafil review – cialis canada price
buy cialis no prescription [url=https://tadalaccess.com/#]Tadal Access[/url] paypal cialis payment
buy facebook business manager account https://buy-business-manager.org/
buy google ads agency account https://buy-verified-ads-account.work
https://tadalaccess.com/# cialis free trial voucher
cialis generic 20 mg 30 pills: Tadal Access – cialis how long does it last
when to take cialis 20mg: Tadal Access – tadalafil oral jelly
cialis india [url=https://tadalaccess.com/#]Tadal Access[/url] best place to get cialis without pesricption
https://tadalaccess.com/# reliable source cialis
buy verified bm facebook buy-bm-account.org
canadian pharmacy generic cialis: vigra vs cialis – is generic cialis available in canada
what is the difference between cialis and tadalafil: where to buy cialis – cialis back pain
buy verified business manager facebook buy-business-manager-acc.org
cialis advertisement [url=https://tadalaccess.com/#]TadalAccess[/url] cialis bathtub
facebook bm account https://buy-verified-business-manager-account.org/
buy facebook business manager accounts buy facebook ads accounts and business managers
https://tadalaccess.com/# cialis next day delivery
cialis generic 20 mg 30 pills: cialis black 800 to buy in the uk one pill – what doe cialis look like
cheap cialis 20mg: TadalAccess – generic cialis online pharmacy
tadalafil dose for erectile dysfunction [url=https://tadalaccess.com/#]cialis genetic[/url] tadalafil troche reviews
https://tadalaccess.com/# cialis for sale
where to get generic cialis without prescription: price of cialis – what does cialis cost
buy cialis in canada: where can i buy cialis online – cialis prescription assistance program
cialis tadalafil [url=https://tadalaccess.com/#]TadalAccess[/url] purchase cialis online cheap
https://tadalaccess.com/# cialis after prostate surgery
cialis free trial offer: shop for cialis – tadalafil eli lilly
fb bussiness manager https://business-manager-for-sale.org
facebook business account for sale buy-business-manager-verified.org
cialis 40 mg: cialis medicare – peptide tadalafil reddit
buy bm facebook https://buy-bm.org
cialis is for daily use [url=https://tadalaccess.com/#]what is cialis used for[/url] cialis for sale over the counter
buy tadalafil cheap: cialis 20mg for sale – sanofi cialis
https://tadalaccess.com/# cialis same as tadalafil
facebook business manager account buy https://verified-business-manager-for-sale.org/
canada cialis: TadalAccess – cialis max dose
cialis available in walgreens over counter?? [url=https://tadalaccess.com/#]cialis dapoxetine australia[/url] what is the generic for cialis
trusted online store to buy cialis: cialis results – no presciption cialis
https://tadalaccess.com/# cialis daily review
buy facebook business manager accounts https://buy-business-manager-accounts.org
canadian cialis: TadalAccess – cialis free trial voucher 2018
buy tiktok ads https://buy-tiktok-ads-account.org
buy tiktok ad account https://tiktok-ads-account-buy.org
buying generic cialis online safe: TadalAccess – tadalafil citrate
how long does cialis last 20 mg [url=https://tadalaccess.com/#]cheapest 10mg cialis[/url] difference between tadalafil and sildenafil
cialis by mail: TadalAccess – generic cialis super active tadalafil 20mg
cialis black: tadalafil vs cialis – best place to buy generic cialis online
https://tadalaccess.com/# cialis images
is there a generic equivalent for cialis [url=https://tadalaccess.com/#]does cialis shrink the prostate[/url] buy tadalafil no prescription
order generic cialis: compounded tadalafil troche life span – cialis website
cialis professional 20 lowest price: cialis canada over the counter – tadalafil professional review
buy tiktok ads account https://tiktok-ads-account-for-sale.org
tiktok agency account for sale https://tiktok-agency-account-for-sale.org
comprar tadalafil 40 mg en walmart sin receta houston texas [url=https://tadalaccess.com/#]us pharmacy prices for cialis[/url] cialis for sale over the counter
tiktok ad accounts https://buy-tiktok-ad-account.org
https://tadalaccess.com/# mail order cialis
canada cialis for sale: TadalAccess – what is cialis good for
For sure.
tiktok ads agency account https://buy-tiktok-ads-accounts.org
cialis and adderall [url=https://tadalaccess.com/#]cialis 800 black canada[/url] cialis where to buy in las vegas nv
prescription for cialis: Tadal Access – cialis tadalafil 20 mg
buy cialis no prescription australia: cialis buy without – prices on cialis
buy cialis by paypal [url=https://tadalaccess.com/#]Tadal Access[/url] cialis review
https://tadalaccess.com/# cialis male enhancement
this is a great post!
what to do when cialis stops working [url=https://tadalaccess.com/#]TadalAccess[/url] cialis blood pressure
this is a great post!
tadalafil cialis: tadalafil tablets 20 mg side effects – cialis difficulty ejaculating
buy tiktok ads account https://buy-tiktok-business-account.org
tiktok ads account for sale https://buy-tiktok-ads.org
https://tadalaccess.com/# cialis using paypal in australia
tiktok ads account buy https://tiktok-ads-agency-account.org
cialis no perscription overnight delivery [url=https://tadalaccess.com/#]TadalAccess[/url] cialis dosage for ed
price of cialis in pakistan: can cialis cause high blood pressure – cialis from india
cialis 20 mg best price [url=https://tadalaccess.com/#]TadalAccess[/url] buy cialis in canada
https://tadalaccess.com/# difference between tadalafil and sildenafil
cialis 20mg: prices of cialis – buy cheap cialis online with mastercard
cialis without prescription: is cialis a controlled substance – cialis 20 milligram
canada cialis [url=https://tadalaccess.com/#]TadalAccess[/url] cialis with dapoxetine
https://tadalaccess.com/# when to take cialis 20mg
price of cialis in pakistan: canada drugs cialis – is tadalafil and cialis the same thing?
cialis online without perscription [url=https://tadalaccess.com/#]tadalafil brand name[/url] cialis what is it
Thank you for your sharing. I am worried that I lack creative ideas. It is your article that makes me full of hope. Thank you. But, I have a question, can you help me?
https://tadalaccess.com/# cialis daily side effects
this is a great post!
cialis online paypal [url=https://tadalaccess.com/#]TadalAccess[/url] cialis 20 mg price walgreens
this is a great post!
buy cialis online from canada: can cialis cause high blood pressure – cialis softabs online
https://tadalaccess.com/# order cialis online cheap generic
cialis erection [url=https://tadalaccess.com/#]cialis trial[/url] cialis 20 mg
cialis generic best price: Tadal Access – cialis 5 mg tablet
https://tadalaccess.com/# cialis from canada to usa
when will cialis become generic: TadalAccess – peptide tadalafil reddit
where to buy cialis online for cheap [url=https://tadalaccess.com/#]Tadal Access[/url] cialis paypal
this is a great post!
this is a great post!
this is a great post!
this is a great post!
this is a great post!
this is a great post!
this is a great post!
get antibiotics without seeing a doctor [url=http://biotpharm.com/#]buy antibiotics online uk[/url] buy antibiotics
discount ed pills: buy ed pills – Ero Pharm Fast
Over the counter antibiotics for infection: Biot Pharm – get antibiotics quickly
low cost ed pills [url=https://eropharmfast.com/#]low cost ed pills[/url] cheapest ed pills
Over the counter antibiotics for infection: buy antibiotics online uk – buy antibiotics for uti
Pharm Au 24: online pharmacy australia – Online drugstore Australia
https://eropharmfast.shop/# Ero Pharm Fast
buy antibiotics from canada: buy antibiotics online uk – over the counter antibiotics
this is a great post!
get antibiotics without seeing a doctor: BiotPharm – get antibiotics without seeing a doctor
Online drugstore Australia: Discount pharmacy Australia – Medications online Australia
this is a great post!
Over the counter antibiotics pills [url=https://biotpharm.com/#]buy antibiotics online uk[/url] buy antibiotics over the counter
Ero Pharm Fast: buy erectile dysfunction treatment – Ero Pharm Fast
Ero Pharm Fast: pills for erectile dysfunction online – Ero Pharm Fast
https://pharmau24.com/# Online drugstore Australia
this is a great post!
ed meds cheap: how to get ed meds online – ed pills
Licensed online pharmacy AU: Medications online Australia – Online medication store Australia
this is a great post!
this is a great post!
https://biotpharm.shop/# Over the counter antibiotics for infection
what is the cheapest ed medication: Ero Pharm Fast – Ero Pharm Fast
buy antibiotics online [url=http://biotpharm.com/#]Over the counter antibiotics for infection[/url] over the counter antibiotics
Medications online Australia: PharmAu24 – Pharm Au24
this is a great post!
http://eropharmfast.com/# Ero Pharm Fast
this is a great post!
buy antibiotics from india: Over the counter antibiotics for infection – Over the counter antibiotics for infection
Ero Pharm Fast: Ero Pharm Fast – Ero Pharm Fast
ed online treatment [url=http://eropharmfast.com/#]online ed pharmacy[/url] online erectile dysfunction medication
Licensed online pharmacy AU: Pharm Au24 – pharmacy online australia
ed treatments online: Ero Pharm Fast – how to get ed meds online
http://biotpharm.com/# buy antibiotics
Pharm Au 24 [url=https://pharmau24.shop/#]Licensed online pharmacy AU[/url] Buy medicine online Australia
Licensed online pharmacy AU: Licensed online pharmacy AU – Online medication store Australia
Over the counter antibiotics for infection: buy antibiotics online uk – get antibiotics quickly
https://biotpharm.shop/# antibiotic without presription
pharmacy online australia: Pharm Au24 – PharmAu24
Medications online Australia [url=http://pharmau24.com/#]Discount pharmacy Australia[/url] Medications online Australia
online pharmacy australia: Online drugstore Australia – PharmAu24
this is a great post!
Licensed online pharmacy AU [url=https://pharmau24.shop/#]Discount pharmacy Australia[/url] pharmacy online australia
this is a great post!
https://biotpharm.shop/# cheapest antibiotics
Over the counter antibiotics for infection: Biot Pharm – buy antibiotics from canada
this is a great post!
Over the counter antibiotics for infection: buy antibiotics online uk – buy antibiotics from canada
this is a great post!
Medications online Australia [url=http://pharmau24.com/#]Pharm Au24[/url] pharmacy online australia
Pharm Au 24: online pharmacy australia – Medications online Australia
https://biotpharm.shop/# Over the counter antibiotics for infection
Discount pharmacy Australia [url=https://pharmau24.shop/#]PharmAu24[/url] Medications online Australia
over the counter antibiotics: buy antibiotics online – buy antibiotics over the counter
Ero Pharm Fast [url=https://eropharmfast.shop/#]Ero Pharm Fast[/url] Ero Pharm Fast
buy antibiotics from india: Biot Pharm – best online doctor for antibiotics
https://eropharmfast.shop/# where to buy erectile dysfunction pills
Medications online Australia [url=https://pharmau24.shop/#]Discount pharmacy Australia[/url] Online drugstore Australia
this is a great post!
this is a great post!
pharmacie en ligne: Medicaments en ligne livres en 24h – pharmacie en ligne pas cher
this is a great post!
kamagra oral jelly [url=https://kampascher.shop/#]commander Kamagra en ligne[/url] kamagra livraison 24h
Cialis générique sans ordonnance: traitement ED discret en ligne – traitement ED discret en ligne
kamagra pas cher: kamagra pas cher – Kamagra oral jelly pas cher
Kamagra oral jelly pas cher: kamagra en ligne – commander Kamagra en ligne
https://kampascher.shop/# livraison discrete Kamagra
Cialis sans ordonnance 24h: commander Cialis en ligne sans prescription – cialis sans ordonnance
kamagra pas cher [url=http://kampascher.com/#]kamagra en ligne[/url] achat kamagra
this is a great post!
kamagra en ligne: livraison discrete Kamagra – Kamagra oral jelly pas cher
this is a great post!
kamagra 100mg prix: pharmacie en ligne france livraison internationale – kamagra gel
this is a great post!
Pharmacies en ligne certifiées: Pharmacies en ligne certifiées – Pharmacie Internationale en ligne
this is a great post!
this is a great post!
Meilleur Viagra sans ordonnance 24h [url=https://viasansordonnance.shop/#]Viagra generique en pharmacie[/url] prix bas Viagra generique
this is a great post!
Viagra generique en pharmacie: commander Viagra discretement – livraison rapide Viagra en France
https://kampascher.com/# livraison discrete Kamagra
Cialis pas cher livraison rapide: cialis generique – Acheter Cialis 20 mg pas cher
cialis prix: Cialis generique sans ordonnance – Achat mГ©dicament en ligne fiable
this is a great post!
prix bas Viagra generique [url=https://viasansordonnance.shop/#]acheter Viagra sans ordonnance[/url] prix bas Viagra generique
Achat mГ©dicament en ligne fiable: cialis sans ordonnance – Pharmacie en ligne livraison Europe
Médicaments en ligne livrés en 24h: acheter médicaments sans ordonnance – pharmacie en ligne pas cher
Viagra sans ordonnance 24h [url=http://viasansordonnance.com/#]viagra sans ordonnance[/url] acheter Viagra sans ordonnance
Viagra sans ordonnance 24h: viagra en ligne – Viagra pas cher livraison rapide france
acheter Viagra sans ordonnance: viagra sans ordonnance – acheter Viagra sans ordonnance
http://kampascher.com/# livraison discrete Kamagra
Médicaments en ligne livrés en 24h: pharmacie internet fiable France – pharmacie en ligne sans ordonnance
Kamagra oral jelly pas cher: pharmacie en ligne fiable – acheter kamagra site fiable
kamagra livraison 24h [url=http://kampascher.com/#]Kamagra oral jelly pas cher[/url] kamagra pas cher
pharmacie en ligne sans prescription: pharmacie en ligne sans ordonnance – acheter mГ©dicament en ligne sans ordonnance
acheter medicaments sans ordonnance: pharmacie en ligne pas cher – vente de mГ©dicament en ligne
Meilleur Viagra sans ordonnance 24h [url=https://viasansordonnance.com/#]Viagra sans ordonnance 24h[/url] commander Viagra discretement
https://viasansordonnance.com/# viagra en ligne
Cialis pas cher livraison rapide: Cialis pas cher livraison rapide – Cialis générique sans ordonnance
pharmacie en ligne sans ordonnance: pharmacie en ligne france fiable – pharmacie en ligne livraison europe
Medicaments en ligne livres en 24h: commander sans consultation medicale – pharmacie en ligne pas cher
Cialis sans ordonnance 24h [url=https://ciasansordonnance.com/#]Cialis sans ordonnance 24h[/url] pharmacie en ligne france livraison belgique
Meilleur Viagra sans ordonnance 24h: viagra en ligne – acheter Viagra sans ordonnance
this is a great post!
Acheter du Viagra sans ordonnance: viagra sans ordonnance – Viagra gГ©nГ©rique pas cher livraison rapide
this is a great post!
this is a great post!
Viagra pas cher livraison rapide france: Acheter du Viagra sans ordonnance – Meilleur Viagra sans ordonnance 24h
kamagra en ligne: livraison discrète Kamagra – kamagra livraison 24h
https://kampascher.com/# commander Kamagra en ligne
pharmacie internet fiable France [url=https://pharmsansordonnance.shop/#]pharmacie en ligne sans prescription[/url] п»їpharmacie en ligne france
this is a great post!
this is a great post!
this is a great post!
this is a great post!
pharmacie en ligne sans prescription: pharmacie en ligne pas cher – pharmacie en ligne avec ordonnance
this is a great post!
pharmacie internet fiable France: Médicaments en ligne livrés en 24h – pharmacie en ligne avec ordonnance
this is a great post!
pharmacie internet fiable France [url=https://pharmsansordonnance.com/#]acheter medicaments sans ordonnance[/url] pharmacie en ligne
cialis generique: pharmacie en ligne france pas cher – pharmacie en ligne france livraison belgique
Sildenafil teva 100 mg sans ordonnance: viagra en ligne – acheter Viagra sans ordonnance
https://pharmsansordonnance.shop/# trouver un mГ©dicament en pharmacie
Achat mГ©dicament en ligne fiable [url=https://pharmsansordonnance.com/#]commander sans consultation medicale[/url] Pharmacie en ligne livraison Europe
Amuletobet Casino 100 Free Spins Bonus 2024 The list of top casino sites is available above, with the best casinos according to our recommendations in the top positions. If you are looking for best casinos overall, you will find them at the top of the list. The first page contains top 10 online casino sites according to our team. However, if your preferences are a bit more specific, you may find our advanced filters helpful. Demo broken Earn entries starting 6 a.m. on November 1 through 9:29 p.m. on November 15 for a chance to win up to $5,000 in free play. Don’t miss out on these free online blackjack tips – they could change your game! The game is played in a penny pokies format, then you will be awarded a scatter win. As he accepts his losses, you can ask a staff member for information on the payout ratio of a particular pokie. Australian casino no deposit bonus codes you should always keep your finger on the pulse, the government has recently introduced stricter regulations to protect consumers.
https://mebeljatijepara.id/optimize-aviator-gameplay-with-mobile-notifications-a-ugandan-players-review/
The Land of New Slots Burning Hot sets itself apart with an eye-catching aesthetic. Featuring ripe fruit symbols like plums, oranges, cherries and watermelons lends the video slot a vibrant feel while still preserving the nostalgic allure associated with classic slots. Multi-denomination, Burning hot is a pleasant game on a green background and easy to understand because here plays an energetic music that corresponds in detail with all the actions that happen on the display. Unlike slot Book of Ra, here the animations are simpler, the trebles appear in special chases and the payouts for payline combinations are clear and visible. This way you always understand what is happening at a particular point in the game and for which symbols you have been paid. The overall impression is more than good, this is a well-balanced game not only from a graphical point of view, but also from the perspective of the money that can be won.
pharmacie en ligne sans ordonnance: pharmacie en ligne sans prescription – Pharmacie sans ordonnance
pharmacie en ligne sans prescription: Medicaments en ligne livres en 24h – trouver un mГ©dicament en pharmacie
Medicaments en ligne livres en 24h [url=http://pharmsansordonnance.com/#]commander sans consultation medicale[/url] pharmacie en ligne france fiable
acheter Viagra sans ordonnance: Viagra generique en pharmacie – Viagra sans ordonnance 24h suisse
kamagra gel: kamagra oral jelly – kamagra en ligne
viagra sans ordonnance: acheter Viagra sans ordonnance – viagra sans ordonnance
this is a great post!
this is a great post!
https://pharmsansordonnance.shop/# п»їpharmacie en ligne france
this is a great post!
cialis sans ordonnance [url=https://ciasansordonnance.com/#]Acheter Cialis[/url] cialis generique
this is a great post!
Viagra 100mg prix: acheter Viagra sans ordonnance – viagra en ligne
this is a great post!
acheter medicaments sans ordonnance: Pharmacies en ligne certifiees – vente de mГ©dicament en ligne
this is a great post!
Pharmacies en ligne certifiees [url=https://pharmsansordonnance.com/#]pharmacie en ligne[/url] pharmacie en ligne france livraison belgique
pharmacie en ligne: pharmacie en ligne pas cher – vente de mГ©dicament en ligne
commander Viagra discretement: Viagra sans ordonnance 24h – commander Viagra discretement
livraison discrete Kamagra [url=https://kampascher.com/#]kamagra pas cher[/url] kamagra 100mg prix
http://viasansordonnance.com/# Viagra femme sans ordonnance 24h
kamagra pas cher: kamagra livraison 24h – kamagra 100mg prix
pharmacie en ligne france livraison internationale: Cialis pas cher livraison rapide – cialis sans ordonnance
pharmacie en ligne pas cher: pharmacie en ligne sans prescription – acheter mГ©dicament en ligne sans ordonnance
commander sans consultation medicale: pharmacie en ligne – trouver un mГ©dicament en pharmacie
cialis generique [url=http://ciasansordonnance.com/#]commander Cialis en ligne sans prescription[/url] Acheter Cialis 20 mg pas cher
this is a great post!
kamagra pas cher: kamagra 100mg prix – kamagra en ligne
this is a great post!
http://kampascher.com/# kamagra livraison 24h
this is a great post!
cialis generique [url=https://ciasansordonnance.shop/#]Achat mГ©dicament en ligne fiable[/url] commander Cialis en ligne sans prescription
kamagra en ligne: achat kamagra – Kamagra oral jelly pas cher
acheter Cialis sans ordonnance [url=https://ciasansordonnance.com/#]Cialis generique sans ordonnance[/url] cialis generique
viagra en ligne: Acheter du Viagra sans ordonnance – Acheter du Viagra sans ordonnance
prix bas Viagra generique: Acheter du Viagra sans ordonnance – Viagra sans ordonnance 24h
livraison rapide Viagra en France [url=https://viasansordonnance.shop/#]Viagra sans ordonnance 24h suisse[/url] Prix du Viagra 100mg en France
https://pharmsansordonnance.shop/# pharmacie en ligne france livraison internationale
viagra en ligne: livraison rapide Viagra en France – SildГ©nafil 100 mg prix en pharmacie en France
kamagra gel [url=https://kampascher.shop/#]kamagra en ligne[/url] kamagra livraison 24h
Cialis sans ordonnance 24h: Acheter Cialis – commander Cialis en ligne sans prescription
Pharmacies en ligne certifiees [url=https://pharmsansordonnance.shop/#]pharmacie en ligne sans prescription[/url] п»їpharmacie en ligne france
livraison rapide Viagra en France: Acheter du Viagra sans ordonnance – Meilleur Viagra sans ordonnance 24h
cialis generique [url=https://ciasansordonnance.com/#]Acheter Cialis 20 mg pas cher[/url] traitement ED discret en ligne
https://viasansordonnance.com/# Viagra sans ordonnance 24h
https://kampascher.shop/# kamagra en ligne
cerchio gocce: cefixoral 400 prezzo – tachifene 500
farmacia vazquez online [url=http://confiapharma.com/#]Confia Pharma[/url] se puede comprar ibuprofeno 400 sin receta
shop farmacia offerte online: seleparina 0 4 prezzo – abiostil unguento nasale
derinox ordonnance: amoxicilline sans ordonnance france – creme emla sur ordonnance
https://pharmacieexpress.shop/# ivermectine sans ordonnance
voltaren fiale prezzo: Farmacia Subito – naos farmaco
que laxantes puedo comprar sin receta [url=http://confiapharma.com/#]comprar sin receta medica[/url] farmacia encasa online
fond de teint vichy liftactiv 45: sinusite medicament sans ordonnance – time filler filorga
mi farma farmacia online: como comprar viagra en barcelona sin receta – montar una farmacia online
inegy 10/20 prezzo [url=https://farmaciasubito.com/#]Farmacia Subito[/url] enstilar schiuma prezzo ticket
tamponi in farmacia fvg prenotazioni online: sporanox sciroppo – paracetamolo 1000 effervescente
shop farmacia online italia: Farmacia Subito – farmacia montemerlo
https://pharmacieexpress.shop/# viagra homme prix en pharmacie sans ordonnance tunisie
viagra pas chere: furterer forticea – inhalation pharmacie sans ordonnance
farmacia en mexico online [url=https://confiapharma.shop/#]Confia Pharma[/url] farmacia online andorra xenical
cilodex a cosa serve: farmacia online napoli – cefodox bambini sciroppo
chat online farmacia: Confia Pharma – comprar estrógenos sin receta
konakion fiale prezzo: lybella pillola prezzo – setofilm 8 mg
exemple ordonnance bas de contention [url=https://pharmacieexpress.com/#]sildenafil 100mg price[/url] tadalafil 5mg sans ordonnance
http://pharmacieexpress.com/# savon rogГ© cavaillГЁs prix en pharmacie
stilnox 10 mg prezzo: farmacia vendita online – olpress 20 mg prezzo
farmacia online andorra: se puede comprar aciclovir sin receta – xenical 120 mg farmacia online
indom collirio monodose: farmacia online italiana – deniban 50 mg prezzo
bandelette urinaire pharmacie sans ordonnance [url=https://pharmacieexpress.shop/#]amoxicilline sans ordonnance[/url] laxatif puissant en pharmacie sans ordonnance
se puede comprar mifepristona sin receta: farmacia andorra online vacunas – test hiv farmacia online
comment acheter un mГ©dicament prescrit sur ordonnance sans ordonnance: tadalafil pas cher – laboratoire sans ordonnance
I just like the helpful information you provide in your articles
se puede comprar ibuprofeno sin receta medica: farmacia online lujan arguelles – promociones farmacia online
puedo comprar viagra sin receta en gibraltar [url=https://confiapharma.shop/#]Confia Pharma[/url] comprar rivotril gotas sin receta
Antes de começar a jogar, faça uma autoavaliação e considere quanto você poderá depositar nos cassinos online para fazer suas apostas e os respectivos períodos de depósito. A seguir, você terá acesso a um ranking de cassinos online confiáveis, com milhares de jogos nas plataformas para fazer apostas online que são autorizadas para operar no Brasil. O Fortune Tiger é um dos slots que fez um sucesso estrondoso nos últimos tempos, atraindo a atenção de diversos apostadores. Mesmo que esteja hospedado em sites diferentes, o Fortune Tiger funciona da mesma maneira em cada uma delas, pois todas as versões do jogo devem obedecer à regra do algoritmo criado pela PG Soft, com o RTP de 96,81%. Algumas empresas também já oferecem atendimento via Telegram ou WhatsApp, já que o suporte via telefone ainda é bem raro no Brasil.
https://aviraaz.com/demo-rabbit-fortune-conheca-o-que-esse-slot-tem-a-oferecer/
Acessibilidade Pompéu, 20 de março de 2025 O site possui alguns recursos para que os usuários personalizem sua visualização, sendo possível salvar jogos e campeonatos favoritos. A plataforma também permite esconder algumas janelas durante as apostas. O site possui alguns recursos para que os usuários personalizem sua visualização, sendo possível salvar jogos e campeonatos favoritos. A plataforma também permite esconder algumas janelas durante as apostas. A navegação na Luva.bet é bastante fluida e intuitiva, além de apresentar uma resposta muito rápida no carregamento dos jogos, tanto na seção de cassino ou quanto na de esportes. Acessibilidade O site possui alguns recursos para que os usuários personalizem sua visualização, sendo possível salvar jogos e campeonatos favoritos. A plataforma também permite esconder algumas janelas durante as apostas.
https://confiapharma.com/# paracetamol farmacia online
epitheliale ah duo: achat propecia – sildenafil acheter
I’m new to blogging and really appreciate your content. This article piqued my interest. Bookmarking your site!
farmacia online lucca: atem aerosol prezzo – jadiza pillola
comprar meriestra sin receta [url=https://confiapharma.shop/#]Confia Pharma[/url] farmacia asturias online
comprar elvanse sin receta: crema emla farmacia online – farmacia online bebes
comprar valium 5mg sin receta [url=https://confiapharma.com/#]se puede comprar paroxetina sin receta[/url] comprar mounjaro farmacia online
se puede comprar acido folico sin receta: puedo comprar amoxicilina sin receta – farmacia francia online
https://pharmacieexpress.shop/# ozempic sans ordonnance france
se puede comprar prednisona sin receta en espaГ±a: apiretal se puede comprar sin receta – comprar orlistat sin receta
quimica y farmacia online [url=https://confiapharma.shop/#]Confia Pharma[/url] que pastillas para dormir puedo comprar sin receta
farmacia online con spese di spedizione basse: aircort prezzo senza ricetta – cicalfate controindicazioni
ordonnance bizone sГ©curisГ©e: nurofen ordonnance – medicament pour maigrir vite sans ordonnance en pharmacie
duphalac farmacia online [url=http://confiapharma.com/#]cursos farmacia online[/url] se puede comprar nuril sin receta
farmacia online mascarillas con filtro: se puede comprar tamiflu sin receta – opiniones de farmacia yanguas 24h pamplona | envГos pedidos online en 2 horas
farmacia online test embarazo [url=https://confiapharma.com/#]farmacia online para comprar viagra[/url] donde comprar levitra sin receta en barcelona
farmacia online affidabili: portugal farmacia online – comprar imalgene 1000 sin receta
avis pharmacie en ligne sans ordonnance: Pharmacie Express – nerisone crème sans ordonnance
gentalyn beta costo: augmentin prezzo con ricetta – pafinur prezzo
https://confiapharma.shop/# se puede comprar viagra sin receta en gibraltar
pommade rap [url=http://pharmacieexpress.com/#]goviril en pharmacie sans ordonnance[/url] test urinaire sans ordonnance
farmacia online en islas baleares: wegovy comprar sin receta – donde comprar medicamentos sin receta en orlando
deursil 450 a cosa serve: Farmacia Subito – acetilcisteina eg 600 mg compresse effervescenti
related:https://www.satisfarma.com/ farmacia online [url=http://confiapharma.com/#]Confia Pharma[/url] lomper comprar sin receta
arnica montana 7ch posologie adulte: prix viagra gГ©nГ©rique en pharmacie – quel mГ©dicament pour une infection urinaire sans ordonnance
ordonnance docteur: mГ©dicaments sans ordonnance pour infection urinaire – fer pharmacie sans ordonnance
https://pharmacieexpress.com/# amoxicilline enfant sans ordonnance
test antigens farmacia online [url=http://confiapharma.com/#]crear farmacia online[/url] farmacia china online
broncho munal bambini: farmacia animali online – berny bustine
donde comprar zopiclona sin receta: comprar medicamentos online – progesterona comprar sin receta
robilas antistaminico prezzo [url=https://farmaciasubito.com/#]epiduo gel 0 3[/url] tylan prezzo
dolocatil codeina comprar sin receta: farmacia online vitamina d – comprar inzitan sin receta
fluimucil per aerosol prezzo: Farmacia Subito – ivomec 50 ml prezzo
creme corticoide sans ordonnance [url=http://pharmacieexpress.com/#]Pharmacie Express[/url] serc sans ordonnance
shampoing kelual ds: pharmacie en ligne sans ordonnance belgique – medicament testosterone sans ordonnance en pharmacie
http://confiapharma.com/# farmacia online test de antigenos
farmacia remedia online [url=http://confiapharma.com/#]Confia Pharma[/url] farmacia online en valencia
se puede comprar pildoras anticonceptivas sin receta: en espaГ±a se puede comprar viagra sin receta – donde puedo comprar diazepam sin receta mГ©dica
https://pharmexpress24.com/# what pharmacy has the best generic percocet
cialis from mexico: buy meds – what meds can you get over the counter in mexico
online pharmacy in india [url=http://inpharm24.com/#]all day pharmacy india[/url] pharmacy in india
tesco pharmacy orlistat: Pharm Express 24 – indian pharmacy
https://pharmmex.com/# best overseas pharmacy
best drugs to buy in mexico: mexican pharmacy delivery – amoxicillin mexico
india online pharmacy [url=https://inpharm24.shop/#]online india pharmacy reviews[/url] get medicines from india
mexican pharmacy near south texas maps: rx meds online – mexican online pharmacy ozempic
buy medicine online: pharmacy franchises in india – top online pharmacy india
get ozempic in mexico: can you buy vicodin in mexico – your mexican pharmacy
india pharmacy online: online pharmacy in india – all day pharmacy india
http://pharmmex.com/# tramadol mexican brands
mexican pharmacy list: mexican pharmacy fentanyl – tirzepatide mexico pharmacy
mexican pharmacy in tijuana: pharmacies in progreso mexico – reliable mexican pharmacy
my mexican pharmacy [url=http://pharmmex.com/#]what drugs can you buy over the counter in mexico[/url] alprazolam mexican pharmacy
tesco pharmacy viagra cost: fred meyer pharmacy hours – online pharmacy no prescription klonopin
buy medicines online india: InPharm24 – indian pharmacies
best online mexican pharmacy: can you get adderall at mexican pharmacy – online pharmacy shop
pharmacy online india [url=http://inpharm24.com/#]buy medicines online india[/url] medplus pharmacy india
http://pharmexpress24.com/# online pharmacy florida
mounjaro mexico: mexican pain relief cream – mexico prednisone
general health: best pharmacy price cialis – cyprus online pharmacy
buy medicine online in india [url=http://inpharm24.com/#]pharmacy franchises in india[/url] medications from india
india pharmacies: InPharm24 – buy viagra online in india
magellan rx specialty pharmacy: Pharm Express 24 – abilify india pharmacy
pharmacy store requirements: krogers pharmacy – nearby pharmacy store
Levitra Professional [url=https://pharmexpress24.com/#]low dose naltrexone skip’s pharmacy[/url] Shallaki
https://pharmexpress24.com/# buy hcg online pharmacy
what drugs can i buy at a mexican pharmacy: xanax from mexican pharmacy – can you buy percocet in mexico
mexican pharmacy online no prescription: buy meds online – hispanic pharmacy near me
online india pharmacy reviews: online pharmacy company in india – dandruff shampoo india pharmacy
prices pharmacy [url=http://pharmexpress24.com/#]Pharm Express 24[/url] gabapentin pharmacy prices
india online pharmacy: InPharm24 – india drug store
pharmseo24.com: cheap viagra online pharmacy prescription – Azulfidine
online pharmacy no scripts [url=https://pharmexpress24.shop/#]modafinil online pharmacy[/url] mexican pharmacy doxycycline
http://inpharm24.com/# cialis india pharmacy
divya pharmacy india: pharmacy in india – medications from india
What is the best 1XBET promo code? In our opinion, it is the one that allows you to get our exclusive welcome sports betting bonus. Our 1XBETpromocode: JBMAX activates a 130% bonus of up to €130 ($145) on the first deposit. It is a 30% extra compared to the standard 100% bonus of up to €100. The bonus amount differ depending on player’s location, and we will show you all that in detail in section 3. JetX promo code offers are a great way to get started with JetX Game. You can receive bonuses for your first deposit, as well as many other offers. The promo codes are easy to use and can be found online. A Code Promo JetX can be a great way to get extra money to gamble with. Just make sure that you understand the terms and conditions associated with the code before you use it. This way, you will be able to withdrawal your winnings without any problems.
https://expathealthseoul.com/profile/rosendo-schwartz/
A Color Trading Prediction Chart is a visual representation of past color results in a color trading game. It helps players analyze trends and patterns to make better guesses for the next round. These color trading prediction charts typically show: Welcome to Big Daddy, a thrilling fusion of color prediction and engaging quizzes! Dive into a world of vibrancy and mental challenges in this captivating app. Hack करो Colour Prediction Gameऔर हर बार जीत कर पैसे कमाओ! 91 Club is the best color prediction gaming website in India. It offers many games including WinGo, Aviator, Slots, and much more. You can get instant withdrawals in 91club game. Download the app now, register your account, and get the sign-up bonus. To successfully bet on Wingo colors, you need to understand the betting systems and how they work. The more you familiarize yourself with these strategies, the higher your chances of making accurate predictions and securing a win.
order penicillin online: algodones pharmacy – mexican pharmacy order online
first online pharmacy in india [url=http://inpharm24.com/#]god of pharmacy in india[/url] india e-pharmacy market size 2025
mexican pharmacy coupon code: mexican pharmacy cancun – mexican online pharmacy reviews
pharmacy in india online [url=http://inpharm24.com/#]india pharmacy no prescription[/url] divya pharmacy india
publix pharmacy hours: effexor xr online pharmacy – best online cialis pharmacy
india pharmacy delivery to usa: InPharm24 – buy online medicine
https://pharmexpress24.shop/# viagra online us pharmacy
maxalt online pharmacy [url=https://pharmexpress24.com/#]Pharm Express 24[/url] allergy
mexicanrxpharm: Pharm Mex – mexican pharmacy reviews
sildenafil 5 mg tablet: VGR Sources – viagra for sale in united states
buy viagra safely online uk [url=https://vgrsources.com/#]viagra 100mg canada[/url] best price for viagra
can you buy female viagra over the counter: 25mg viagra – online viagra coupon
where can i buy generic viagra online safely: VGR Sources – viagra price in south africa
viagra price per pill: VGR Sources – viagra 100mg tablet online in india
buy generic viagra online australia: VGR Sources – online viagra coupon
https://vgrsources.com/# cheap female viagra online
real viagra for sale [url=https://vgrsources.com/#]VGR Sources[/url] sildenafil pharmacy australia
where can i get viagra online: canadian pharmacy generic sildenafil – viagra 100mg pills generic
sildenafil 10 mg: viagra soft canada – where to buy viagra in usa
sales viagra: VGR Sources – purchase viagra in usa
viagra 500mg price in india: generic sildenafil 100mg tablet – viagra black
https://vgrsources.com/# viagra how to get a prescription
best pharmacy prices for viagra: VGR Sources – where to buy generic viagra online in canada
generic sildenafil in us: VGR Sources – canadian pharmacy viagra uk
viagra over the counter europe [url=https://vgrsources.com/#]where to get female viagra pills[/url] online viagra coupon
can i buy over the counter viagra: purchase viagra online canada – sildenafil 120 mg
buy cheap generic viagra: VGR Sources – viagra in india online purchase
best over the counter female viagra: viagra buying canada – sildenafil coupon 100 mg
viagra fast delivery [url=https://vgrsources.com/#]VGR Sources[/url] viagra for females
female viagra online india: order sildenafil uk – online viagra tablets in india
https://vgrsources.com/# best viagra online australia
sildenafil women: VGR Sources – price viagra
where can i purchase viagra online: australia generic viagra – viagra-50mg
viagra prescription cost uk [url=https://vgrsources.com/#]VGR Sources[/url] order viagra from uk
this is a great post!
buying viagra online illegal: viagra price in mexico – canadian pharmacy for viagra
this is a great post!
this is a great post!
sildenafil for sale: discount viagra online canada – viagra pills for sale online
sildenafil tablets 50mg: can you buy sildenafil – genuine viagra best price
generic viagra online paypal [url=https://vgrsources.com/#]viagra 100 mg tablet price[/url] sildenafil citrate tablets
viagra pills price canada: viagra non prescription – cheap viagra 50mg
https://vgrsources.com/# buy female viagra uk online
buy generic 100mg viagra online: sildenafil 20 mg tablet – where can i buy viagra over the counter in singapore
sildenafil 5343: canadian online pharmacy viagra – sildenafil citrate 100
viagra average cost: VGR Sources – can i buy viagra over the counter in south africa
buy viagra 100mg uk [url=https://vgrsources.com/#]VGR Sources[/url] how can i get viagra in canada
viagra super active canada: viagra canada order – compare generic viagra prices
best viagra in usa [url=https://vgrsources.com/#]generic viagra from india online[/url] sildenafil price australia
https://vgrsources.com/# viagra 500mg online
order viagra uk: VGR Sources – where to get viagra over the counter
cheap viagra pills from india: viagra over the counter uk – viagra pills price in india
sildenafil 100mg uk paypal: viagra 100 mg from mexico – sildenafil 100mg sale
cheap viagra canada free shipping [url=https://vgrsources.com/#]VGR Sources[/url] female viagra medication
75 mg sildenafil: VGR Sources – how to buy viagra in india
generic sildenafil citrate: VGR Sources – buy viagra soft
generic for viagra: where to buy female viagra canada – viagra online prescription uk
75 mg viagra [url=https://vgrsources.com/#]genuine viagra online uk[/url] viagra singapore price
generic viagra prescription online: sildenafil generic drug cost – cheap viagra usa
can i order viagra online: VGR Sources – sildenafil price singapore
https://vgrsources.com/# cheapest sildenafil 50 mg
cheap viagra uk: VGR Sources – 50mg viagra
sildenafil 20mg generic cost [url=https://vgrsources.com/#]VGR Sources[/url] how much is viagra online
sildenafil online in india: VGR Sources – sildenafil online pharmacy uk
generic sildenafil 40 mg: buy sildenafil 50mg – sildenafil online purchase india
price for viagra 100mg [url=https://vgrsources.com/#]cheapest sildenafil australia[/url] buy female viagra online australia
cheap generic viagra free shipping: order brand name viagra online – average cost sildenafil 20mg
sildenafil 50 mg no prescription: VGR Sources – viagra uk otc
https://vgrsources.com/# viagra black
how to get viagra in us: viagra 20 mg cost – sildenafil 50mg tablets uk
viagra price online [url=https://vgrsources.com/#]VGR Sources[/url] how to order viagra online in canada
sildenafil 100mg tablets: sildenafil tablets 100mg uk – buy viagra online paypal
cost generic viagra: viagra for female price – buy viagra soft online
what does semaglutide do to your body: SemagluPharm – Online pharmacy Rybelsus
CrestorPharm [url=http://crestorpharm.com/#]goodrx crestor[/url] Crestor Pharm
Semaglu Pharm: Rybelsus online pharmacy reviews – can you take metformin and rybelsus together
Ne zamandır web sitelerim için aradığım içeriği sonunda buldum. Bu kadar detaylı ve net açıklama için teşekkürler.
gerçekten güzel bir yazı olmuş. Yanlış bildiğimiz bir çok konu varmış. Teşekkürler.
Yazınız için teşekkürler. Bu bilgiler ışığında nice insanlar bilgilenmiş olacaktır.
http://lipipharm.com/# Lipi Pharm
prednisone in mexico: prednisone cost in india – how to get prednisone tablets
Predni Pharm: prednisone 10mg price in india – prednisone 20
traveling with semaglutide [url=https://semaglupharm.com/#]Semaglu Pharm[/url] SemagluPharm
Rybelsus side effects and dosage: rybelsus sglt2 – Semaglu Pharm
Predni Pharm: Predni Pharm – prednisone 25mg from canada
USA-based pharmacy Lipitor delivery: Lipi Pharm – FDA-approved generic statins online
SemagluPharm [url=http://semaglupharm.com/#]tirzepatide vs semaglutide dosage for weight loss[/url] hims compounded semaglutide
FDA-approved generic statins online: can lipitor cause ed – when drawing lipitorВ®, why does chemdraw create two large compounds instead of one?
https://crestorpharm.com/# how much does crestor lower cholesterol
Best price for Crestor online USA: Crestor Pharm – Crestor Pharm
Generic Crestor for high cholesterol [url=https://crestorpharm.com/#]Crestor home delivery USA[/url] Generic Crestor for high cholesterol
prednisone 1 mg daily: non prescription prednisone 20mg – prednisone cost 10mg
CrestorPharm: Crestor Pharm – Crestor Pharm
http://prednipharm.com/# can you buy prednisone in canada
can you cut atorvastatin in half: Safe atorvastatin purchase without RX – LipiPharm
Predni Pharm [url=http://prednipharm.com/#]over the counter prednisone pills[/url] Predni Pharm
O projeto Lucky Jet 2 surpreende os jogadores com seus gráficos realistas e animação detalhada de objetos. Os desenvolvedores conseguiram combinar a mecânica simples do jogo com um enredo muito emocionante. O jogador está na orla da baía e diante de seus olhos há uma batalha militar. Um caça a jato decola do convés de um porta-aviões e parte numa missão de guerra em Lucky Jet 2. No horizonte, podem ver-se ilhas rochosas envoltas em nuvens. Há muitos navios de guerra, barcos e submarinos na superfície da água. Concluindo, para baixar o aplicativo Lucky Jet, os usuários do Android podem instalar o aplicativo 1win no site oficial, enquanto os usuários do iOS podem precisar seguir instruções específicas, dependendo do navegador que estiverem usando. O aplicativo Lucky Jet também está disponível para download em plataformas como Play Market e App Store. Além disso, os jogadores podem acessar o jogo Lucky Jet por meio do navegador da Web de seus computadores sem a necessidade de instalar o aplicativo.
https://onboardittech.com/penalty-shoot-out-da-evoplay-uma-revisao-completa-para-jogadores-brasileiros/
❌ O game pode ser viciante, por isso é importante jogar com responsabilidade e não apostar todo o seu dinheiro. Lucky Jet é fácil de entender e jogar, não importa se você é um iniciante ou um jogador experiente. O principal objetivo do jogo é fazer cair seu jato com o menor número possível de apostas. Você começa colocando sua aposta em 1x ou 2x, dependendo de quanto risco você quer correr. À medida que você avança no jogo, você vai desbloqueando novos níveis e mais opções para apostar. À medida que você atingir níveis mais altos, seus multiplicadores máximos também serão aumentados! Você também pode usar fichas especiais para aumentar suas chances de ganhar. Fique de olho em ofertas especiais e recompensas que podem ajudar a aumentar ainda mais seus ganhos. Boa sorte e divirta-se!
can atorvastatin cause constipation: Online statin drugs no doctor visit – LipiPharm
Predni Pharm: prednisone 5mg coupon – PredniPharm
Rybelsus online pharmacy reviews: how long does rybelsus stay in your system – SemagluPharm
Crestor Pharm [url=http://crestorpharm.com/#]CrestorPharm[/url] Crestor 10mg / 20mg / 40mg online
Semaglu Pharm: sulfur burps semaglutide – Semaglu Pharm
PredniPharm: generic prednisone pills – prednisone 20mg prices
PredniPharm: prednisone 20 mg tablets – Predni Pharm
Crestor Pharm [url=https://crestorpharm.com/#]Crestor Pharm[/url] does crestor help with triglycerides
Crestor Pharm: side effects of crestor vs lipitor – Crestor Pharm
can you take rosuvastatin and atorvastatin together [url=http://crestorpharm.com/#]crestor 10 mg nedir[/url] Crestor Pharm
crestor and gout: Crestor Pharm – Generic Crestor for high cholesterol
Predni Pharm: PredniPharm – prednisone price australia
Order rosuvastatin online legally [url=http://crestorpharm.com/#]Crestor Pharm[/url] rosuvastatin coupon walgreens
https://semaglupharm.com/# rybelsus mechanism of action
can crestor raise blood pressure: does crestor cause dry mouth – crestor over the counter
PredniPharm: prednisone 50 mg tablet canada – Predni Pharm
prednisone 10 [url=https://prednipharm.com/#]PredniPharm[/url] PredniPharm
Crestor Pharm: Buy statins online discreet shipping – crestor and lexapro
Crestor Pharm: CrestorPharm – side effects of rosuvastatin calcium 20 mg
https://lipipharm.shop/# LipiPharm
SemagluPharm: rybelsusдёж–‡ – how long do you stay on semaglutide for weight loss
this is a great post!
this is a great post!
this is a great post!
this is a great post!
Crestor Pharm [url=http://crestorpharm.com/#]CrestorPharm[/url] Crestor Pharm
this is a great post!
this is a great post!
CrestorPharm: Crestor Pharm – CrestorPharm
buy prednisone 50 mg [url=http://prednipharm.com/#]buy prednisone 10 mg[/url] can i buy prednisone online in uk
http://semaglupharm.com/# Affordable Rybelsus price
Online pharmacy Rybelsus [url=https://semaglupharm.shop/#]rybelsus 5 mg[/url] No prescription diabetes meds online
Crestor Pharm: CrestorPharm – Best price for Crestor online USA
http://semaglupharm.com/# SemagluPharm
Discreet shipping for Lipitor [url=https://lipipharm.shop/#]lipitor synthesis[/url] Safe atorvastatin purchase without RX
Semaglu Pharm: Semaglu Pharm – Semaglu Pharm
https://semaglupharm.com/# what to eat while on semaglutide
http://lipipharm.com/# LipiPharm
Buy statins online discreet shipping [url=http://crestorpharm.com/#]Crestor Pharm[/url] CrestorPharm
п»їBuy Lipitor without prescription USA: LipiPharm – Lipi Pharm
https://semaglupharm.com/# SemagluPharm
LipiPharm: LipiPharm – Affordable Lipitor alternatives USA
CrestorPharm [url=http://crestorpharm.com/#]No doctor visit required statins[/url] Crestor Pharm
https://semaglupharm.com/# Order Rybelsus discreetly
Buy cholesterol medicine online cheap: CrestorPharm – apo rosuvastatin 40 mg
https://semaglupharm.com/# rybelsus 14 mg precio walmart
SemagluPharm [url=https://semaglupharm.shop/#]SemagluPharm[/url] semaglutide gastroparesis
https://semaglupharm.shop/# SemagluPharm
can lipitor cause fatigue: lipitor uses – Lipi Pharm
Crestor Pharm: Crestor Pharm – how to stop crestor
PredniPharm [url=http://prednipharm.com/#]prednisone 5 mg cheapest[/url] prednisone 25mg from canada
this is a great post!
https://semaglupharm.com/# rybelsus storage
this is a great post!
CrestorPharm: Crestor Pharm – Crestor Pharm
this is a great post!
http://semaglupharm.com/# Semaglu Pharm
п»їBuy Crestor without prescription [url=https://crestorpharm.shop/#]Crestor Pharm[/url] CrestorPharm
http://semaglupharm.com/# Safe delivery in the US
LipiPharm: Lipi Pharm – LipiPharm
LipiPharm: LipiPharm – LipiPharm
https://semaglupharm.shop/# SemagluPharm
PredniPharm [url=http://prednipharm.com/#]how to get prednisone tablets[/url] PredniPharm
overdose on lipitor: pictures of atorvastatin 20 mg – Lipi Pharm
Predni Pharm: Predni Pharm – PredniPharm
https://semaglupharm.com/# rybelsus fda
PredniPharm [url=https://prednipharm.com/#]Predni Pharm[/url] prednisone 10mg online
Predni Pharm: PredniPharm – PredniPharm
https://semaglupharm.shop/# Semaglu Pharm
SemagluPharm [url=http://semaglupharm.com/#]SemagluPharm[/url] diabetes rybelsus
this is a great post!
Thank you for your sharing. I am worried that I lack creative ideas. It is your article that makes me full of hope. Thank you. But, I have a question, can you help me?
Fortune Clock s’efforce de créer une ambiance dynamique et divertissante, avec des fonctionnalités interactives telles que le chat en direct permettant aux joueurs de communiquer avec les croupiers et d’autres participants. Cela ajoute une dimension sociale au jeu en ligne, rendant l’expérience plus engageante et conviviale. La diversité des jeux de live casino, combinée à la qualité de la diffusion en direct et à l’interaction avec les croupiers, fait du live casino de Fortune Clock une option attrayante pour les amateurs de jeux de table en quête d’une expérience de jeu en direct authentique et divertissante. Lisez instantanément sur votre navigateur avec Kindle pour le Web. Recommandez-vous ce canal groupe bot à d’autres? Rédigez un avis détaillé pour aider les utilisateurs à décider s’ils souhaitent s’abonner à cette chaîne groupe bot.
https://ytinboyhhon1979.cavandoragh.org/http-asso-ppnmc-fr
Chez Please Casino, nous découvrons régulièrement de nouveaux mini-jeux en ligne casino pour le plus grand bonheur de nos lecteurs. Récemment, Evoplay a sorti sa nouvelle création : Penalty Shoot Out Street. Nous avons pris beaucoup de plaisir l’essayer et à découvrir toutes les fonctionnalités et le potentiel du titre. L’équipe de rédaction vous donne son avis maintenant ! H8PRRj mpfoigtaaygr, yrajvtkbbykm, pjsidmrdhrms, widcjwkufqrv H8PRRj mpfoigtaaygr, yrajvtkbbykm, pjsidmrdhrms, widcjwkufqrv Can you hear me OK? depo medrol dose for dogs There was no immediate word on the extent of the injury and the team said Maclin was still being evaluated. Maclin went down at the end of a non-contact drill and appeared in pain while on the ground for several minutes.
this is a great post!
crestor and pregnancy: CrestorPharm – how does crestor lower cholesterol
grapefruit crestor: Crestor Pharm – Crestor Pharm
this is a great post!
http://semaglupharm.com/# Semaglu Pharm
https://prednipharm.shop/# Predni Pharm
LipiPharm: Safe atorvastatin purchase without RX – Lipi Pharm
https://semaglupharm.com/# Affordable Rybelsus price
is crestor bad for your kidneys [url=http://crestorpharm.com/#]CrestorPharm[/url] Crestor Pharm
iv prednisone: prednisone for sale online – PredniPharm
https://semaglupharm.com/# semaglutide burping
п»їBuy Lipitor without prescription USA: Order cholesterol medication online – Affordable Lipitor alternatives USA
buy medicines online in india [url=https://indiapharmglobal.com/#]п»їlegitimate online pharmacies india[/url] India Pharm Global
https://indiapharmglobal.com/# Online medicine home delivery
https://medsfrommexico.com/# Meds From Mexico
medicine in mexico pharmacies: Meds From Mexico – Meds From Mexico
top online pharmacy india: india pharmacy mail order – India Pharm Global
canadianpharmacyworld [url=http://canadapharmglobal.com/#]Canada Pharm Global[/url] canadian pharmacy uk delivery
http://indiapharmglobal.com/# India Pharm Global
Online medicine order: India Pharm Global – India Pharm Global
http://indiapharmglobal.com/# world pharmacy india
best canadian online pharmacy reviews [url=http://canadapharmglobal.com/#]canadian neighbor pharmacy[/url] canadian 24 hour pharmacy
best online pharmacies in mexico: mexican drugstore online – best online pharmacies in mexico
http://medsfrommexico.com/# medication from mexico pharmacy
https://canadapharmglobal.shop/# canada drugs online
п»їlegitimate online pharmacies india: cheapest online pharmacy india – indianpharmacy com
indian pharmacy online [url=https://indiapharmglobal.shop/#]cheapest online pharmacy india[/url] mail order pharmacy india
https://canadapharmglobal.com/# online canadian pharmacy review
India Pharm Global: India Pharm Global – top 10 pharmacies in india
india pharmacy mail order: best india pharmacy – buy prescription drugs from india
Meds From Mexico [url=https://medsfrommexico.shop/#]Meds From Mexico[/url] reputable mexican pharmacies online
https://medsfrommexico.shop/# medication from mexico pharmacy
Meds From Mexico: buying prescription drugs in mexico – best online pharmacies in mexico
canadian pharmacy online ship to usa [url=https://canadapharmglobal.shop/#]Canada Pharm Global[/url] canada drugstore pharmacy rx
https://canadapharmglobal.com/# trustworthy canadian pharmacy
gentamicina a cosa serve: fucidin crema per cosa serve – EFarmaciaIt
scalapay accedi [url=http://efarmaciait.com/#]nicetile opinioni[/url] arval creme recensioni
http://papafarma.com/# cbd lugo
http://svenskapharma.com/# Svenska Pharma
apotek mina recept: Svenska Pharma – Svenska Pharma
medrol per 3 giorni [url=https://efarmaciait.shop/#]EFarmaciaIt[/url] EFarmaciaIt
https://svenskapharma.com/# tudca köpa
Svenska Pharma: gratis babybox apotek – Svenska Pharma
comprar loniten 10 mg [url=http://papafarma.com/#]farma 2[/url] mercado parque alcosa
https://raskapotek.shop/# Rask Apotek
https://svenskapharma.com/# Svenska Pharma
Svenska Pharma: Svenska Pharma – apotek shampoo
https://svenskapharma.com/# medeciner
EFarmaciaIt [url=http://efarmaciait.com/#]EFarmaciaIt[/url] ismigen ci vuole ricetta
Svenska Pharma: medicin apotek – Svenska Pharma
skjeggsjampo apotek: apoteker – Rask Apotek
https://raskapotek.shop/# Rask Apotek
Svenska Pharma [url=https://svenskapharma.com/#]Svenska Pharma[/url] logga in apotek
https://efarmaciait.com/# EFarmaciaIt
brystpumpe apotek: apotek ГҐpent nyttГҐrsaften – apotek leppepomade
https://raskapotek.com/# borsyre apotek
apoteket: Rask Apotek – Rask Apotek
EFarmaciaIt [url=https://efarmaciait.shop/#]siti farmacia con spedizione gratuita[/url] farmacie on line napoli
Papa Farma: para que sirve la diprogenta – Papa Farma
http://papafarma.com/# farmacias direct
kompresjon arm apotek: te tre olje apotek – vanndrivende midler apotek
Svenska Pharma [url=https://svenskapharma.com/#]apotek snabbast leverans[/url] Svenska Pharma
https://efarmaciait.com/# voltaren collirio a cosa serve
http://papafarma.com/# medicamentos online
EFarmaciaIt: EFarmaciaIt – farmaГЁ i miei ordini
http://svenskapharma.com/# Svenska Pharma
Papa Farma: Papa Farma – Papa Farma
EFarmaciaIt: farmacia online sconti – EFarmaciaIt
https://efarmaciait.com/# farmacia marchi
https://raskapotek.com/# apotek klamydia test
farmacia klarna: nicetile cos’ГЁ – EFarmaciaIt
bettskena apotek: Svenska Pharma – Svenska Pharma
https://papafarma.com/# tiendas cbd valladolid
Papa Farma [url=https://papafarma.com/#]Papa Farma[/url] farmacia vigo online
http://efarmaciait.com/# bactroban crema opinioni
apotek finland [url=http://svenskapharma.com/#]Г¶ronhГҐltagning apotek[/url] vilket apotek har min medicin
MedicijnPunt: Medicijn Punt – MedicijnPunt
https://pharmaconnectusa.shop/# PharmaConnectUSA
online apotheek goedkoper [url=https://medicijnpunt.com/#]medicatie bestellen[/url] Medicijn Punt
https://pharmaconnectusa.shop/# online pharmacy zithromax
https://pharmaconnectusa.com/# PharmaConnectUSA
Pharma Confiance: Pharma Confiance – Pharma Confiance
online apotheke wegovy [url=https://pharmajetzt.shop/#]versand apotheke auf rechnung[/url] apotheken online shop
https://pharmaconfiance.shop/# cbd lyon part dieu
Pharma Confiance: Pharma Confiance – Pharma Confiance
http://pharmaconnectusa.com/# lexapro indian pharmacy
Pharma Confiance [url=https://pharmaconfiance.shop/#]sildГ©nafil prix[/url] avis mon pharmacien conseil
MedicijnPunt: MedicijnPunt – MedicijnPunt
https://pharmaconnectusa.com/# atlantic pharmacy cialis
Pharma Confiance: Pharma Confiance – Pharma Confiance
medikamente online [url=https://pharmajetzt.com/#]gГјnstigste versandapotheke[/url] medikamente online
https://pharmaconfiance.com/# pharmacie par internet
Pharma Confiance: Pharma Confiance – exemple ordonnance bas de contention
http://medicijnpunt.com/# bestellen medicijnen
Medicijn Punt: medicijnen aanvragen apotheek – Medicijn Punt
http://pharmajetzt.com/# sjop apotheke
parapharmacie online: Pharma Confiance – grossiste croquette chat
medicijnen bestellen apotheek [url=http://medicijnpunt.com/#]MedicijnPunt[/url] online pharmacy nl
apteka amsterdam: Medicijn Punt – Medicijn Punt
https://pharmaconnectusa.shop/# online pharmacy no prescription lasix
Pharma Connect USA: united rx pharmacy – PharmaConnectUSA
shop apothek [url=https://pharmajetzt.com/#]Pharma Jetzt[/url] apotheke bestellen
http://pharmajetzt.com/# Pharma Jetzt
pharcie: soolantra prix pharmacie – Pharma Confiance
https://pharmaconfiance.com/# médicaments en ligne
luitpold apotheke berlin: shopaphotheke – Pharma Jetzt
MedicijnPunt [url=http://medicijnpunt.com/#]medicijnen snel bestellen[/url] farma online
Looking forward to your next post. Keep up the good work!
est-ce que je peux avoir du monuril sans ordonnance ?: pharmacie de garde toulouse aujourd’hui – Pharma Confiance
online apotheke gГјnstig [url=https://pharmajetzt.com/#]Pharma Jetzt[/url] medikame
https://pharmaconnectusa.shop/# PharmaConnectUSA
apteka internetowa holandia: apteka eindhoven – MedicijnPunt
Medicijn Punt: Medicijn Punt – medicaties
mijn apotheek medicijnen [url=https://medicijnpunt.shop/#]recept medicijn[/url] apotheke
https://pharmajetzt.shop/# medikamente corona apotheke
wegovy achat [url=http://pharmaconfiance.com/#]Pharma Confiance[/url] Pharma Confiance
https://pharmaconfiance.shop/# pharmacie de garde 49 aujourd’ hui
Pharma Confiance: exemple ongle gel – sanoflore pharmacie
https://pharmaconnectusa.shop/# best online pharmacy no prescription
http://pharmaconfiance.com/# amoxicilline gelule
Kazinosunda Pin-Up Aviator yuvası xüsusi bölmədə yerləşdirilib. Əsas Pin-Up səhifəsini açdığınız vaxt seçməlisiniz aviator game yuxarı üfüqi idarəetmə panelindəNişan qırmızı rənglə vurğulanır. Nişanı kliklədiyiniz zaman aviator oyunu iki rejimdə pulsuz və praktik para. В мире ставок и азарта 1win – это имя, которое ассоциируется с надежностью, быстротой и комфортной игрой. 1win – это официальный сайт букмекерской конторы, которая предлагает своим клиентам широкий спектр услуг и возможностей для ставок на спорт, киберспорт и другие события.
https://www.pr5-articles.com/Articles-of-2024/vulkanvegasnetpl
Having an international license enables Mostbet to indication up clients through many countries. Residents of these places can not enjoy Mostbet casino, neither make bets, employ Mostbet bonus. Accessing Mostbet from a good unsupported territory using a VPN performed for us. It didn’t help explain Mostbet’s lack involving promotional programs, nevertheless it did give to us the bandwidth to subscribe, make deposits make wagers. Jim Zhu wants to travel and explore brand new metropolitan areas across the world, but he’s not ever been enthusiast of concert tour vehicles. He doesn’t like getting captured in a seat and afflicted by somebody else’s timetable. Jim is healthier and energetic and prefers the independence of walking from place to spot at his personal speed. But standard maps is cumbersome, and before smartphones emerged regarding scene, phones didn’t provide a lot help when navigating a brand new area.
Medicijn Punt: MedicijnPunt – belgische online apotheek
pharmacie pas chere [url=https://pharmaconfiance.com/#]amoxicilline et lait[/url] sildenafil sans ordonnance
https://pharmaconfiance.com/# boutique en ligne lourdes
lait pour le corps la vie est belle pas cher: Pharma Confiance – Pharma Confiance
http://medicijnpunt.com/# medicijnen kopen met ideal
https://pharmaconfiance.com/# pharmacie drive
Pharma Confiance [url=http://pharmaconfiance.com/#]Pharma Confiance[/url] materiel medical vichy
MedicijnPunt: Medicijn Punt – MedicijnPunt
PharmaJetzt: online apoteken – Pharma Jetzt
https://pharmaconfiance.shop/# Pharma Confiance
medikamente online kaufen [url=https://pharmajetzt.shop/#]Pharma Jetzt[/url] online apotheke deutschland
luitpold-apotheke bad steben: shop apotheke versandkostenfrei – Pharma Jetzt
viata online apotheek: Medicijn Punt – MedicijnPunt
http://pharmaconnectusa.com/# guardian pharmacy propecia
Fulvicin [url=http://pharmaconnectusa.com/#]PharmaConnectUSA[/url] drug rx
https://pharmaconfiance.com/# Pharma Confiance
Pharma Connect USA: simvastatin at target pharmacy – arcoxia online pharmacy
https://pharmajetzt.shop/# apoteheke
target pharmacy nexium: island pharmacy calcitriol – generic pharmacy propecia
main courante hГЄtre 4 m [url=http://pharmaconfiance.com/#]Pharma Confiance[/url] meilleur site de pharmacie en ligne
https://pharmajetzt.shop/# Pharma Jetzt
Pharma Confiance: Pharma Confiance – Pharma Confiance
Pharma Confiance [url=https://pharmaconfiance.com/#]wegovy en ligne[/url] Pharma Confiance
http://pharmaconfiance.com/# pharmacie dagneux
MedicijnPunt: online medicijnen – MedicijnPunt
https://pharmajetzt.com/# apotheke obline
Pharma Connect USA: buy pain pills online pharmacy – Pharma Connect USA
apotheken online bestellen [url=https://pharmajetzt.com/#]medikamente apotheke[/url] welche ist die gГјnstigste online apotheke
http://pharmaconnectusa.com/# viagra overseas pharmacy
pillen apotheke: Pharma Jetzt – mediherz versandapotheke online shop
medpex online apotheke: welche online apotheke ist am gГјnstigsten – shop aphotheke
global rx pharmacy irvine [url=https://pharmaconnectusa.shop/#]simvastatin uk pharmacy[/url] Pharma Connect USA
https://medicijnpunt.shop/# Medicijn Punt
https://pharmaconnectusa.shop/# online lortab pharmacy
mycose nez chat: Pharma Confiance – Pharma Confiance
http://pharmaconfiance.com/# pharmacie grand paris
PharmaJetzt: PharmaJetzt – euro apotheke
Pharma Connect USA [url=https://pharmaconnectusa.com/#]online pharmacy viagra no prescription[/url] rite aid pharmacy store locations
https://pharmaconnectusa.shop/# PharmaConnectUSA
MedicijnPunt: Medicijn Punt – appotheek
http://pharmaconfiance.com/# Pharma Confiance
apotheek online nederland: Medicijn Punt – Medicijn Punt
acheter viagra original [url=http://pharmaconfiance.com/#]Pharma Confiance[/url] Pharma Confiance
apotheke auf rechnung bestellen: PharmaJetzt – Pharma Jetzt
http://pharmajetzt.com/# apotheke deutschland
online apotheek 24: MedicijnPunt – medicijnen kopen met ideal
medicijnen online: MedicijnPunt – mijn medicijnen bestellen
fortГ© pharma collagГЁne avis [url=http://pharmaconfiance.com/#]Pharma Confiance[/url] Pharma Confiance
https://pharmajetzt.shop/# PharmaJetzt
online apotheke versandkostenfrei auf rechnung: medikamente bestellen online – Pharma Jetzt
apotheker online: apotal apotheke online – medi apotheke
MedicijnPunt: apotheker medicatie – Medicijn Punt
https://pharmaconnectusa.com/# can i get misoprostol at a pharmacy
online medicijnen kopen [url=https://medicijnpunt.com/#]europese apotheek[/url] medicatie aanvragen
publix pharmacy lisinopril: buy amoxicillin no prescription fda checked pharmacy – compounding pharmacy synthroid
http://pharmajetzt.com/# shop apptheke
online-apotheke: schnellste online apotheke – PharmaJetzt
Pharma Connect USA [url=https://pharmaconnectusa.shop/#]Pharma Connect USA[/url] Pharma Connect USA
Pharma Confiance: Pharma Confiance – antihistaminique pied main bouche
caudalie nantes: Pharma Confiance – Pharma Confiance
https://pharmaconnectusa.com/# buying online pharmacy
Pharma Jetzt: fledox in apotheke kaufen – apotheke online gГјnstig bestellen
https://pharmaconnectusa.com/# Primaquine
Pharma Confiance [url=https://pharmaconfiance.com/#]Pharma Confiance[/url] contact ghd
furterer logo: cure vichy avis – livraison mГ©dicament paris
distribution de chacun cherche son chat: Pharma Confiance – Pharma Confiance
http://pharmajetzt.com/# apotal online shop
medicijn [url=https://medicijnpunt.shop/#]apotheek aan huis[/url] apotheke online
Pharma Confiance: pharmacie canadienne avis – Pharma Confiance
https://pharmaconnectusa.com/# Pharma Connect USA
https://medicijnpunt.com/# MedicijnPunt
smiths pharmacy: mexican pharmacy weight loss – PharmaConnectUSA
acheter de l’amoxicilline sans ordonnance [url=https://pharmaconfiance.shop/#]Pharma Confiance[/url] pharmacie de garde Г vichy
http://pharmaconnectusa.com/# Pharma Connect USA
Pharma Connect USA: big pharmacy online – Pharma Connect USA
PharmaConnectUSA: online pharmacy amoxicillin uk – pharmacy escrow viagra
http://pharmaconfiance.com/# Pharma Confiance
rx specialty pharmacy [url=http://pharmaconnectusa.com/#]Pharma Connect USA[/url] PharmaConnectUSA
https://medicijnpunt.shop/# Medicijn Punt
I just like the helpful information you provide in your articles
Pharma Jetzt: PharmaJetzt – apotheke online gГјnstig
http://pharmaconfiance.com/# Pharma Confiance
Pharma Confiance: Pharma Confiance – doctolib rouen mon compte
Pharma Confiance [url=https://pharmaconfiance.com/#]pharmacie 24h[/url] Pharma Confiance
Pharma Confiance: Pharma Confiance – Pharma Confiance
http://pharmajetzt.com/# shopaphotheke
I appreciate you sharing this blog post. Thanks Again. Cool.
https://pharmajetzt.com/# Pharma Jetzt
online pharmacy worldwide shipping: PharmaConnectUSA – PharmaConnectUSA
viagra online us pharmacy [url=https://pharmaconnectusa.com/#]mexican pharmacy seroquel[/url] us pharmacy no prescription
PharmaConnectUSA: amoxicillin price pharmacy – us online pharmacy
Some genuinely fantastic articles on this site, thankyou for contribution.
PharmaJetzt: Pharma Jetzt – Pharma Jetzt
https://indimedsdirect.com/# pharmacy website india
cheapest online pharmacy india: best online pharmacy india – top 10 online pharmacy in india
world pharmacy india [url=https://indimedsdirect.com/#]india pharmacy mail order[/url] indian pharmacy
https://tijuanameds.com/# TijuanaMeds
https://tijuanameds.shop/# TijuanaMeds
TijuanaMeds: TijuanaMeds – TijuanaMeds
TijuanaMeds: buying prescription drugs in mexico – mexican pharmaceuticals online
www canadianonlinepharmacy [url=https://canrxdirect.com/#]buy canadian drugs[/url] canadian pharmacy 1 internet online drugstore
https://indimedsdirect.com/# pharmacy website india
IndiMeds Direct: IndiMeds Direct – IndiMeds Direct
https://canrxdirect.com/# online canadian pharmacy reviews
IndiMeds Direct [url=https://indimedsdirect.com/#]IndiMeds Direct[/url] IndiMeds Direct
http://indimedsdirect.com/# IndiMeds Direct
https://indimedsdirect.shop/# buy prescription drugs from india
canadian pharmacy 24 [url=http://canrxdirect.com/#]CanRx Direct[/url] pet meds without vet prescription canada
https://canrxdirect.shop/# legitimate canadian pharmacy
IndiMeds Direct [url=http://indimedsdirect.com/#]IndiMeds Direct[/url] IndiMeds Direct
https://indimedsdirect.shop/# reputable indian online pharmacy
http://tijuanameds.com/# TijuanaMeds
canadian pharmacy [url=https://canrxdirect.com/#]CanRx Direct[/url] buying from canadian pharmacies
TijuanaMeds: п»їbest mexican online pharmacies – TijuanaMeds
https://tijuanameds.shop/# mexico drug stores pharmacies
canadian pharmacy review: CanRx Direct – online pharmacy canada
canadian pharmacy online store [url=https://canrxdirect.com/#]canadian valley pharmacy[/url] certified canadian international pharmacy
https://tijuanameds.com/# buying prescription drugs in mexico online
best online pharmacy india: IndiMeds Direct – Online medicine order
https://tijuanameds.com/# mexican mail order pharmacies
reputable mexican pharmacies online: pharmacies in mexico that ship to usa – TijuanaMeds
IndiMeds Direct [url=https://indimedsdirect.shop/#]IndiMeds Direct[/url] IndiMeds Direct
enclomiphene best price: enclomiphene buy – enclomiphene citrate
ConGaDen là địa chỉ xem đá gà online Campuchia Thomo sắc nét hiện nay. Miễn phí 100%, tốc độ ổn định. Xem ngay hôm nay để trải nghiệm đá gà đỉnh cao!
https://enclomiphenebestprice.com/# enclomiphene testosterone
permethrin uk pharmacy: ventolin hfa pharmacy – pharmacy no prescription required
45678 hoạt động từ năm 2015, dưới quy định của cơ quan cá cược trực tuyến Costa Rica. Vượt qua nhiều vòng kiểm tra bảo mật, mọi hoạt động đều hợp pháp. Tham gia ngay để chơi an toàn.
RxFree Meds [url=https://rxfreemeds.com/#]RxFree Meds[/url] RxFree Meds
https://farmaciaasequible.shop/# Farmacia Asequible
https://enclomiphenebestprice.com/# enclomiphene online
producto de parafarmacia: Farmacia Asequible – neoretin serum despigmentante opiniones
https://enclomiphenebestprice.com/# enclomiphene
enclomiphene online [url=https://enclomiphenebestprice.shop/#]enclomiphene price[/url] enclomiphene buy
RxFree Meds: RxFree Meds – RxFree Meds
https://farmaciaasequible.shop/# Farmacia Asequible
Viagra Soft Flavored [url=http://rxfreemeds.com/#]RxFree Meds[/url] best online pharmacy no prescription viagra
https://enclomiphenebestprice.shop/# enclomiphene online
https://bvxl.ru.com/ phát sóng đá gà Campuchia full bồ từ nhiều sới gà hàng đầu, gồm đá gà cựa sắt với video chuẩn nét. Phân tích gay cấn từng đòn – Đừng bỏ lỡ!
enclomiphene best price: buy enclomiphene online – enclomiphene best price
eucerin black friday [url=https://farmaciaasequible.shop/#]Farmacia Asequible[/url] vimovo precio
https://rxfreemeds.shop/# RxFree Meds
Đăng ký Alo789 là hệ thống dẫn đầu tại châu Á, thu hút lượng lớn thành viên. Uy tín được xây dựng trên trải nghiệm đáng tin, luôn lấy thành viên làm trọng tâm.
movicol es con receta: iraltone prospecto – Farmacia Asequible
Alo789 là sân chơi nổi tiếng tại châu Á, thu hút hàng triệu thành viên. Danh tiếng được xây dựng trên sự công bằng, luôn đặt người chơi lên hàng đầu.
enclomiphene price: enclomiphene buy – enclomiphene for men
soolantra crema amazon [url=https://farmaciaasequible.com/#]farmacia a domicilio cerca de mi[/url] aquilea melatonina prospecto
http://farmaciaasequible.com/# parque alcosa como llegar
https://rxfreemeds.shop/# permethrin cream pharmacy
cymbalta pharmacy price: phenytoin pharmacy protocol – RxFree Meds
Smokeys – nơi xem kèo chất lượng 2025, cập nhật kèo bóng đá liên tục, phân tích chuyên sâu giúp bạn tự tin cược.
agua de vichy para la diarrea [url=https://farmaciaasequible.com/#]Farmacia Asequible[/url] melatonina gominolas opiniones
http://farmaciaasequible.com/# Farmacia Asequible
enclomiphene citrate: enclomiphene online – enclomiphene
http://enclomiphenebestprice.com/# enclomiphene testosterone
Farmacia Asequible [url=https://farmaciaasequible.shop/#]Farmacia Asequible[/url] Farmacia Asequible
cost of viagra in pharmacy: tadalafil pharmacy online – pharmacy near me
https://enclomiphenebestprice.shop/# buy enclomiphene online
Farmacia Asequible: tadalafil online – farmacia a domicilio cerca de mГ
http://rxfreemeds.com/# RxFree Meds
enclomiphene price: enclomiphene for men – enclomiphene citrate
enclomiphene citrate [url=http://enclomiphenebestprice.com/#]enclomiphene buy[/url] enclomiphene citrate
HitClub – nền tảng giải trí hấp dẫn 2025 với game bài đổi thưởng, giao diện mượt, quà tặng siêu khủng.
HitClub – thế giới đổi thưởng hot nhất 2025 với tài xỉu đổi thưởng, bảo mật cao, ưu đãi mỗi ngày.
enclomiphene for men [url=https://enclomiphenebestprice.shop/#]enclomiphene online[/url] enclomiphene online
RxFree Meds: viagra in indian pharmacy – freds pharmacy store
https://rxfreemeds.shop/# tegretol online pharmacy
Farmacia Asequible: droguerГa cerca de mГ – Farmacia Asequible
http://enclomiphenebestprice.com/# enclomiphene
lamictal pharmacy assistance [url=https://rxfreemeds.shop/#]RxFree Meds[/url] griseofulvin online pharmacy
cialis mexico pharmacy: online pharmacy sildenafil 100mg – RxFree Meds
https://farmaciaasequible.shop/# famacia barata
RxFree Meds: baclofen river pharmacy – generic viagra online pharmacy no prescription
Go88 – sân chơi đổi thưởng đỉnh cao với nổ hũ đa dạng, giao diện hiện đại, quà tặng cực chất.
enclomiphene citrate [url=https://enclomiphenebestprice.com/#]enclomiphene for sale[/url] enclomiphene online
comprar semaglutida online: Farmacia Asequible – Farmacia Asequible
https://farmaciaasequible.com/# top farmacias
http://farmaciaasequible.com/# melatonina 20 mg amazon
farmacias mas baratas: Farmacia Asequible – Farmacia Asequible
RxFree Meds [url=https://rxfreemeds.com/#]buy ambien online pharmacy[/url] ambien india pharmacy
MCW – sân chơi chuẩn quốc tế từ 2011, được giám sát hợp pháp. Cá cược thể thao đáng tin cậy, hoạt động chuyên nghiệp.
https://farmaciaasequible.shop/# Farmacia Asequible
http://enclomiphenebestprice.com/# enclomiphene for men
RxFree Meds: pharmacy choice loratadine – klonopin online pharmacy no prescription
Nitroglycerin: acyclovir target pharmacy – RxFree Meds
https://farmaciaasequible.com/# crema brentan para que sirve
enclomiphene price [url=https://enclomiphenebestprice.shop/#]enclomiphene for sale[/url] enclomiphene testosterone
rx pharmacy plus: RxFree Meds – percocet online pharmacy without prescriptions
RxFree Meds: RxFree Meds – RxFree Meds
https://enclomiphenebestprice.com/# buy enclomiphene online
RxFree Meds: pharmacy magazine warfarin – warfarin pharmacy protocol
enclomiphene citrate [url=http://enclomiphenebestprice.com/#]enclomiphene citrate[/url] enclomiphene online
MCW – thương hiệu cá cược minh bạch, được kiểm soát chặt chẽ, mang đến dịch vụ chuyên nghiệp với game đa dạng, xử lý mượt mà.
https://enclomiphenebestprice.shop/# buy enclomiphene online
MCW – nền tảng giải trí minh bạch, được kiểm soát chặt chẽ, mang đến dịch vụ chuyên nghiệp với hỗ trợ 24/7, xử lý mượt mà.
buy enclomiphene online: enclomiphene best price – enclomiphene best price
RxFree Meds [url=http://rxfreemeds.com/#]pharmacy program online[/url] RxFree Meds
enclomiphene for sale: enclomiphene best price – enclomiphene for sale
http://farmaciaasequible.com/# Farmacia Asequible
https://enclomiphenebestprice.shop/# enclomiphene testosterone
Farmacia Asequible [url=http://farmaciaasequible.com/#]Farmacia Asequible[/url] farmacia mГЎlaga cerca de mi
http://farmaciaasequible.com/# celestone cronodose sin receta
blink pharmacy: flovent hfa online pharmacy – pharmacy open near me
top rated online pharmacy: RxFree Meds – adipex diet pills online pharmacy
enclomiphene price [url=http://enclomiphenebestprice.com/#]enclomiphene price[/url] buy enclomiphene online
http://rxfreemeds.com/# RxFree Meds
https://rxfreemeds.shop/# viagra best online pharmacy
enclomiphene best price [url=http://enclomiphenebestprice.com/#]enclomiphene citrate[/url] buy enclomiphene online
http://enclomiphenebestprice.com/# enclomiphene buy
RxFree Meds: advair pharmacy assistance – lamictal pharmacy prices
RxFree Meds: costa rica pharmacy viagra – RxFree Meds
acyclovir target pharmacy [url=https://rxfreemeds.com/#]RxFree Meds[/url] RxFree Meds
http://enclomiphenebestprice.com/# enclomiphene online
enclomiphene for men: enclomiphene best price – buy enclomiphene online
enclomiphene best price: enclomiphene testosterone – enclomiphene price
https://enclomiphenebestprice.com/# enclomiphene online
elocom precio [url=http://farmaciaasequible.com/#]Farmacia Asequible[/url] Farmacia Asequible
Nitroglycerin: RxFree Meds – RxFree Meds
enclomiphene: buy enclomiphene online – enclomiphene price
RxFree Meds [url=https://rxfreemeds.com/#]fluconazole pharmacy first[/url] online shopping pharmacy india
harlem rx pharmacy: RxFree Meds – RxFree Meds
https://enclomiphenebestprice.com/# buy enclomiphene online
online pharmacy tamoxifen: percocet online pharmacy without prescriptions – lipitor $4 copay pharmacy
Farmacia Asequible [url=https://farmaciaasequible.shop/#]Farmacia Asequible[/url] paragarmacia
fda approved online pharmacy: citizens rx pharmacy – rx discount pharmacy
http://enclomiphenebestprice.com/# enclomiphene buy
https://enclomiphenebestprice.com/# enclomiphene for men
RxFree Meds: RxFree Meds – indian pharmacy cialis
RxFree Meds: RxFree Meds – RxFree Meds
viagra online uk pharmacy [url=http://rxfreemeds.com/#]RxFree Meds[/url] Confido
https://enclomiphenebestprice.com/# enclomiphene online
enclomiphene online: buy enclomiphene online – buy enclomiphene online
Farmacia Asequible [url=https://farmaciaasequible.shop/#]farmacia abierta cerca de aquГ[/url] Farmacia Asequible
https://farmaciaasequible.shop/# supradyn mujer opiniones
https://enclomiphenebestprice.com/# enclomiphene for sale
buy enclomiphene online [url=https://enclomiphenebestprice.shop/#]enclomiphene price[/url] enclomiphene testosterone
https://farmaciaasequible.shop/# farmacias 24h barcelona
MexiMeds Express: mexican mail order pharmacies – buying prescription drugs in mexico online
Sinemet [url=http://medismartpharmacy.com/#]MediSmart Pharmacy[/url] Thorazine
https://medismartpharmacy.com/# the drug store
http://meximedsexpress.com/# MexiMeds Express
best india pharmacy: IndoMeds USA – online shopping pharmacy india
https://meximedsexpress.com/# MexiMeds Express
fluconazole online pharmacy [url=https://medismartpharmacy.com/#]MediSmart Pharmacy[/url] finpecia from inhouse pharmacy
viagra muscat pharmacy: MediSmart Pharmacy – superdrug pharmacy cialis
VND789 là website cá cược trực tuyến uy tín, tích hợp game bài. Với bảo mật cao, VND789 đảm bảo trải nghiệm chuyên nghiệp và phần thưởng hấp dẫn mỗi ngày.
legal canadian pharmacy online: care pharmacy rochester nh store hours – canada cloud pharmacy
http://medismartpharmacy.com/# viagra online uk pharmacy
https://meximedsexpress.com/# MexiMeds Express
mexico drug stores pharmacies [url=https://meximedsexpress.shop/#]mexican border pharmacies shipping to usa[/url] MexiMeds Express
IndoMeds USA: IndoMeds USA – top online pharmacy india
canadian pharmacy mall: online pharmacy reviews reddit – canadianpharmacyworld
http://medismartpharmacy.com/# accutane pharmacy coupons
MexiMeds Express [url=https://meximedsexpress.shop/#]mexican online pharmacies prescription drugs[/url] MexiMeds Express
mexican online pharmacies prescription drugs: MexiMeds Express – mexican pharmaceuticals online
http://meximedsexpress.com/# п»їbest mexican online pharmacies
best india pharmacy: online shopping pharmacy india – IndoMeds USA
http://medismartpharmacy.com/# people’s pharmacy zoloft
indian pharmacy paypal [url=https://indomedsusa.shop/#]top 10 online pharmacy in india[/url] IndoMeds USA
KUBET là sân chơi trực tuyến hàng đầu châu Á, được cấp phép bởi PAGCOR và tập đoàn KU. Cung cấp nền tảng giải trí gồm thể thao, casino trực tuyến, đổi thưởng, nổ hũ, game bắn cá, Keno.
http://indomedsusa.com/# pharmacy website india
prescription drugs canada buy online: MediSmart Pharmacy – vipps canadian pharmacy
Online medicine home delivery [url=https://indomedsusa.com/#]online shopping pharmacy india[/url] best online pharmacy india
https://indomedsusa.shop/# IndoMeds USA
VND789 là nền tảng game online hàng đầu, quy tụ nổ hũ.
http://medismartpharmacy.com/# people’s pharmacy bupropion
pharmacy website india: IndoMeds USA – IndoMeds USA
viagra in uk pharmacy: target pharmacy crestor – viagra pharmacy 100mg
MexiMeds Express [url=https://meximedsexpress.com/#]best online pharmacies in mexico[/url] mexican mail order pharmacies
https://meximedsexpress.com/# MexiMeds Express
IndoMeds USA: IndoMeds USA – IndoMeds USA
KV999 là nền tảng game online uy tín, tích hợp nổ hũ cùng công nghệ tiên tiến.
online pharmacy vardenafil: MediSmart Pharmacy – cymbalta mail order pharmacy
MexiMeds Express [url=http://meximedsexpress.com/#]best online pharmacies in mexico[/url] MexiMeds Express
https://medismartpharmacy.shop/# priceline pharmacy viagra
https://meximedsexpress.shop/# medicine in mexico pharmacies
canadian pharmacy meds: bestsellers – pet meds without vet prescription canada
pharmacy website india [url=https://indomedsusa.com/#]world pharmacy india[/url] IndoMeds USA
http://indomedsusa.com/# IndoMeds USA
IndoMeds USA: п»їlegitimate online pharmacies india – IndoMeds USA
lipitor diplomat pharmacy: trazodone price pharmacy – cialis tesco pharmacy
http://indomedsusa.com/# indian pharmacy online
IndoMeds USA [url=https://indomedsusa.com/#]india pharmacy[/url] IndoMeds USA
buy account facebook ads account buying platform secure account purchasing platform
http://medismartpharmacy.com/# propecia discount pharmacy
legit canadian pharmacy online: compound pharmacy domperidone – canadian pharmacy ed medications
IndoMeds USA: top online pharmacy india – IndoMeds USA
https://meximedsexpress.shop/# MexiMeds Express
top online pharmacy india [url=https://medismartpharmacy.shop/#]pharmacy certificate programs online[/url] enterprise rx pharmacy system
https://indomedsusa.com/# IndoMeds USA
MexiMeds Express [url=http://meximedsexpress.com/#]MexiMeds Express[/url] mexican pharmaceuticals online
http://meximedsexpress.com/# mexico drug stores pharmacies
MexiMeds Express [url=https://meximedsexpress.shop/#]mexican online pharmacies prescription drugs[/url] mexico pharmacies prescription drugs
http://indomedsusa.com/# indian pharmacy online
https://indomedsusa.com/# IndoMeds USA
IndoMeds USA: top 10 pharmacies in india – IndoMeds USA
This is really interesting, You’re a very skilled blogger. I’ve joined your feed and look forward to seeking more of your magnificent post. Also, I’ve shared your site in my social networks!
reputable mexican pharmacies online [url=http://meximedsexpress.com/#]MexiMeds Express[/url] mexican rx online
buy facebook profiles guaranteed accounts sell pre-made account
http://meximedsexpress.com/# MexiMeds Express
target pharmacy price cialis [url=http://medismartpharmacy.com/#]MediSmart Pharmacy[/url] viagra target pharmacy
https://indomedsusa.shop/# cheapest online pharmacy india
https://meximedsexpress.shop/# mexico pharmacies prescription drugs
bupropion sr online pharmacy: MediSmart Pharmacy – nexium 40 mg pharmacy
best india pharmacy [url=https://indomedsusa.com/#]online pharmacy india[/url] reputable indian pharmacies
https://indomedsusa.com/# world pharmacy india
MexiMeds Express: pharmacies in mexico that ship to usa – MexiMeds Express
donde comprar viagra en granada sin receta [url=https://clinicagaleno.com/#]Clinica Galeno[/url] comprar botox sin receta
https://pharmadirecte.shop/# generique jasmine
movicol bustine adulti: OrdinaSalute – dicloreum 150 mg
diurГ©tique naturel puissant pharmacie sans ordonnance: durex classic jean – prix viagra pharmacie
http://clinicagaleno.com/# farmacia online en leganes
http://pharmadirecte.com/# generique daflon
flixotide spray [url=http://ordinasalute.com/#]gastrotuss bustine bugiardino[/url] kestine prezzo