In the realm of portable electronic devices(RIGID-FLEX PCBS), achieving optimal design and manufacturing standards is imperative to fulfill specific requirements. These devices demand internal circuitry that not only ensures high reliability for their designated functions but also exhibits resilience in the face of challenging environments. The gamut of challenges encompasses extreme temperature fluctuations, exposure to moisture-laden atmospheres, physical impacts, as well as susceptibility to electromagnetic interference (EMI) and radio frequency (RF) disruptions.
Compounding these challenges is the necessity to ingeniously utilize limited space within the device. The relentless march towards sleeker, slimmer, and more pliable portable devices, including smartphones, smartwatches, wearable fitness trackers, inventory management tools, and even dental surgery eyeglasses, demands circuitry that impeccably marries these compact dimensions with featherlight weight for optimum user convenience.
Among the trio of printed circuit board technologies – RIGID-FLEX PCBS, flex circuits, and rigid-flex circuits – customers are confronted with a pivotal decision. While rigid circuit boards boast versatility across a broad spectrum of applications, it is the domain of rigid-flex circuits that reigns supreme as the preferred choice for portable devices.
In essence, the intricate interplay between cutting-edge design and manufacturing methodologies is what empowers the evolution of portable electronic devices, enabling them to seamlessly merge efficiency, durability, and ergonomic elegance.
Addressing the intricate design demands of modern portable electronic devices is a complex endeavor. The conventional paradigms of rigid printed circuit boards (RIGID-FLEX PCBS) and flexible circuits each present their own set of limitations when catering to the multifaceted requisites of these devices.
Challenges with Rigid PCBs and Flex Circuits
While RIGID-FLEX PCBS offer robustness, EMI/RF shielding, and shock resistance, they often fall short when it comes to accommodating the intricate connectivity demands of portable devices. Numerous points of interconnect, involving connector solder joints, connector interfaces, wire solder joints, and crimped wire contacts, become necessary to fulfill the intricate connectivity matrix. Unfortunately, this proliferation of interconnect points escalates the susceptibility to failures, thus jeopardizing device reliability.
Moreover, the incorporation of connectors adds weight and occupies valuable space within the device, potentially leading to suboptimal ergonomics and bulkier dimensions. The rigidity of these boards also hampers their ability to conform to the contours of curved or flexible devices, limiting design possibilities.
On the flip side, flexible circuit boards exhibit promise in accommodating bendable and flexible devices, harmonizing form with function. Their slender profiles seamlessly integrate with mechanical components, yet they too necessitate connectors and solder joints, maintaining the complexity of interconnections.
Harnessing the Power of Rigid-Flex Boards
In the realm of portable device design, a breakthrough solution emerges: the deployment of rigid-flex circuit boards. This innovative amalgamation marries the strengths of rigid PCBs and flex circuits, engendering an all-encompassing platform that overcomes the drawbacks of both predecessors.
The Profound Advantages of Rigid-Flex Boards
- Revolutionizing Packaging: The integration of rigid circuits with flex areas within a single unit heralds a transformation in packaging efficiency. By markedly reducing, and in some cases, obviating the need for wired connections, rigid-flex boards enable designers to conceive products that are not only lighter but also more compact. The diminutive form factor of the flex area materials, accounting for only 10% of the size and weight of wired solutions, empowers design freedom without compromising on performance. This paradigm shift accommodates leaner, sleeker, and more elegant product designs, all while retaining uncompromised functionality.
- Unprecedented Versatility: Rigid-flex circuit boards flex their mettle when it comes to tight spaces and complex contours. These boards can infiltrate recesses and crannies that multiple rigid boards, connectors, and wiring harnesses would struggle to inhabit. Furthermore, their remarkable bend capabilities facilitate interconnect solutions previously unattainable with conventional designs.
- Enhanced Durability: Rigid-flex boards bestow unparalleled resilience by judiciously allocating rigid circuitry for robustness and flex areas for adaptability. This marriage of sturdiness and flexibility ensures that each facet of the device receives tailored reinforcement, elevating its shock absorbance and longevity.
In the dynamic landscape of portable electronic devices, the emergence of rigid-flex circuit boards heralds a paradigm shift. These boards surmount the limitations of their precursors, fusing innovative design with unwavering functionality. The journey towards more sophisticated, ergonomic, and reliable portable devices is emboldened by the pioneering prowess of rigid-flex technology.
Golden Margins –Entire Range of Touchscreen Products
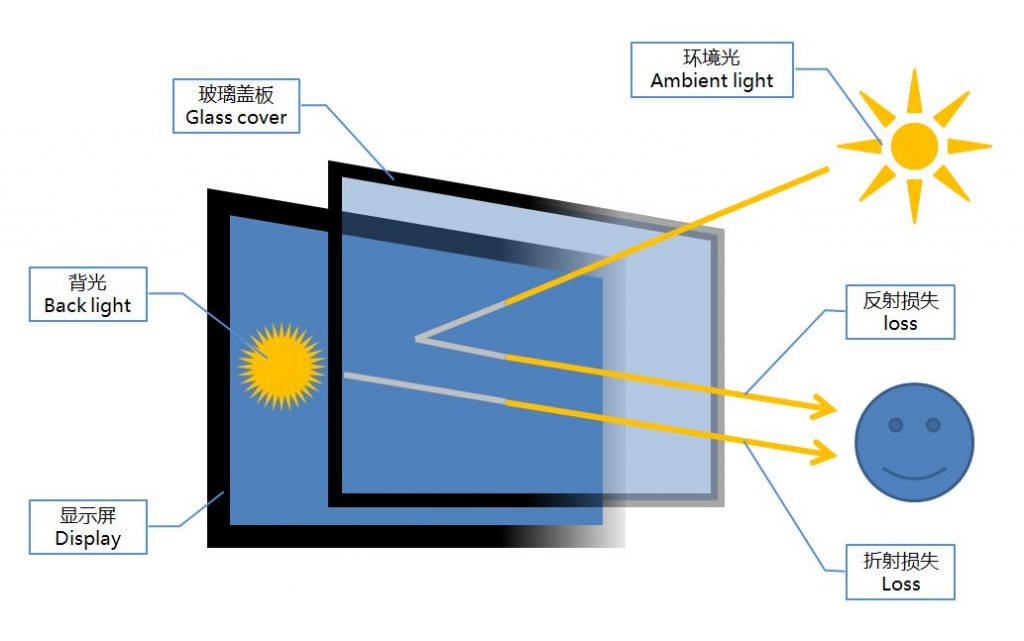
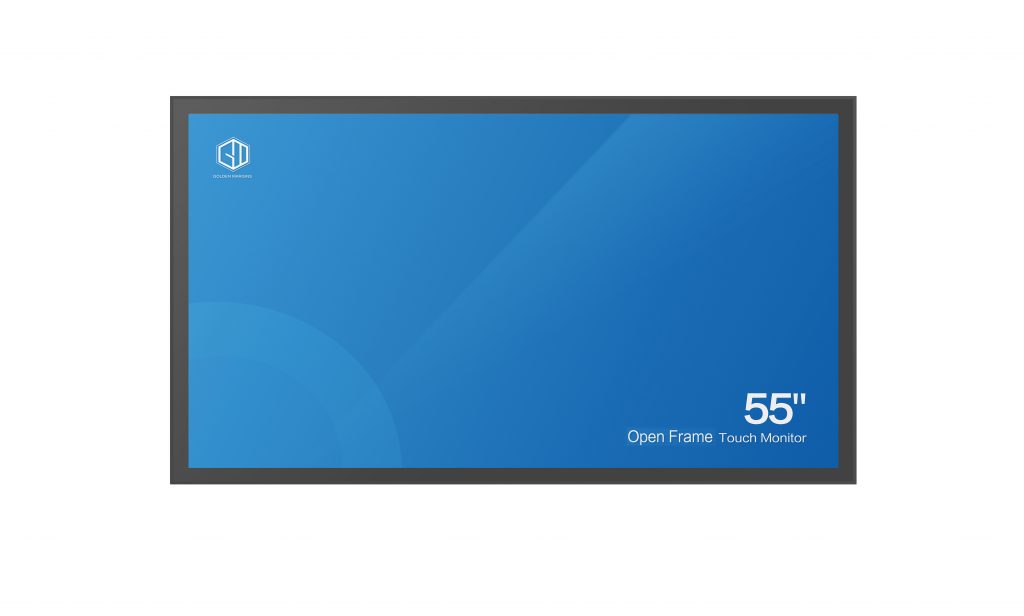
We hope you found these touchscreen or panel PC fundamentals informative. Goldenmargins offers a broad selection of Industrial Touchscreen Monitors and Touch Panel PCs in various sizes and configurations, including medical touch screens, sunlight-readable touch screens, open-frame touch screens, and waterproof touch panels, as well as other unique touch screen or panel PC designs. You can learn more about our services HERE or by calling us at +86 755 23191996 or sales@goldenmargins.com
Comments (109)
Thank you for your sharing. I am worried that I lack creative ideas. It is your article that makes me full of hope. Thank you. But, I have a question, can you help me?
биржа аккаунтов гарантия при продаже аккаунтов
купить аккаунт аккаунт для рекламы
покупка аккаунтов https://magazin-akkauntov-online.ru/
маркетплейс аккаунтов соцсетей магазин аккаунтов
маркетплейс аккаунтов соцсетей продажа аккаунтов
продажа аккаунтов соцсетей kupit-akkaunt-top.ru/
продажа аккаунтов перепродажа аккаунтов
Verified Accounts for Sale Account exchange
Account Sale Website for Buying Accounts
Purchase Ready-Made Accounts Profitable Account Sales
Sell Account buyaccountsmarketplace.com
Ready-Made Accounts for Sale Purchase Ready-Made Accounts
Social media account marketplace Buy accounts
Account Trading Platform Accounts market
Account Trading Service Website for Buying Accounts
Purchase Ready-Made Accounts Accounts for Sale
Account Trading https://buyaccounts001.com
Account Catalog Website for Selling Accounts
purchase ready-made accounts account buying service
online account store account sale
online account store account exchange
secure account sales account exchange
account catalog accounts market
account buying service buy account
account market https://socialaccountsdeal.com/
buy and sell accounts secure account sales
account selling platform account marketplace
ready-made accounts for sale https://socialaccountsshop.com
purchase ready-made accounts sell pre-made account
secure account purchasing platform account acquisition
sell pre-made account account trading
guaranteed accounts account store
account trading accounts-for-sale.org
purchase ready-made accounts guaranteed accounts
gaming account marketplace secure account sales
sell pre-made account account buying platform
account trading platform website for selling accounts
profitable account sales marketplace for ready-made accounts
accounts marketplace account store
account trading platform account trading
profitable account sales account marketplace
account market accounts market
verified accounts for sale buy accounts
buy account account trading platform
account market account sale
buy accounts account catalog
profitable account sales accounts market
verified accounts for sale https://accounts-marketplace.xyz
verified accounts for sale https://buy-best-accounts.org/
secure account purchasing platform https://social-accounts-marketplaces.live/
buy and sell accounts https://accounts-marketplace.live
sell account https://social-accounts-marketplace.xyz
account trading https://buy-accounts.space/
account acquisition https://buy-accounts-shop.pro/
account acquisition https://accounts-marketplace.art
account trading https://social-accounts-marketplace.live
website for buying accounts account market
account catalog https://accounts-marketplace.online
account purchase accounts-marketplace-best.pro
продажа аккаунтов https://akkaunty-na-prodazhu.pro
маркетплейс аккаунтов https://kupit-akkaunt.xyz/
продажа аккаунтов rynok-akkauntov.top
магазин аккаунтов маркетплейсов аккаунтов
маркетплейс аккаунтов соцсетей https://akkaunty-market.live
площадка для продажи аккаунтов https://kupit-akkaunty-market.xyz
продать аккаунт https://akkaunty-optom.live/
продать аккаунт https://online-akkaunty-magazin.xyz
маркетплейс аккаунтов соцсетей магазины аккаунтов
покупка аккаунтов kupit-akkaunt.online
buy accounts facebook https://ad-account-buy.top
facebook ads account buy facebook ad account for sale
facebook account buy https://ad-account-for-sale.top
buy facebook account for ads https://buy-ad-account.click
buy facebook ads accounts https://ad-accounts-for-sale.work
google ads account buy https://buy-ads-account.top
buy verified google ads accounts https://buy-ads-accounts.click
facebook ads account buy https://buy-accounts.click
google ads account buy buy old google ads account
buy google ads account https://ads-account-buy.work
buy verified google ads accounts buy google adwords account
buy account google ads https://buy-account-ads.work
buy google ads threshold accounts google ads accounts for sale
old google ads account for sale https://sell-ads-account.click
buy google ad account https://buy-verified-ads-account.work/
buy verified business manager buy facebook verified business account
buy google ads verified account google ads account for sale
buy facebook business managers https://buy-business-manager-acc.org/
buy facebook bm account buy-bm-account.org
buy fb bm https://buy-verified-business-manager-account.org/
verified bm https://buy-verified-business-manager.org
buy fb bm https://business-manager-for-sale.org/
buy facebook business manager https://buy-business-manager-verified.org/
verified bm for sale buy-bm.org
facebook business manager buy verified facebook business manager for sale
buy facebook business manager account buy fb bm
buy tiktok ads account https://buy-tiktok-ads-account.org
tiktok ad accounts https://tiktok-ads-account-buy.org
buy tiktok business account https://tiktok-ads-account-for-sale.org
tiktok ads agency account https://tiktok-agency-account-for-sale.org
buy tiktok ads account buy tiktok business account
tiktok ads account for sale https://buy-tiktok-ads-accounts.org
I value this information.
buy tiktok ads accounts https://buy-tiktok-ads.org
tiktok agency account for sale https://buy-tiktok-business-account.org
tiktok ads account for sale https://tiktok-ads-agency-account.org
buy old facebook account for ads account exchange account acquisition
Thank you for your sharing. I am worried that I lack creative ideas. It is your article that makes me full of hope. Thank you. But, I have a question, can you help me?
I don’t think the title of your article matches the content lol. Just kidding, mainly because I had some doubts after reading the article.