Industrial displays often operate in complex environments where electrostatic interference, dust adsorption and component damage are common challenges. Antistatic coatings directly address these issues through targeted technology. This paper analyzes the core functions and application scenarios of the antistatic coating from the actual industrial scenarios.
1. Eliminate the risk of electrostatic interference
In industrial environments, static electricity accumulation on the surface of the display can lead to dust adsorption, touch control failure, and even trigger internal circuit failures. Even when wearing an anti-static bracelet operation, the uncoated screen may still interfere with the device signal due to electrostatic discharge, so the need for antistatic coating. It utilizes a conductive material (such as indium tin oxide) to form a charge release path that directs static electricity into a grounding system. The use of electrostatic coatings on the screens of medical devices and laboratory instruments prevents electrostatic interference from affecting the accuracy of the sensors.
2. Ensure the stability of the equipment
Electrostatic discharge easily penetrates display capacitors, chips and other vulnerable components. In some scenarios, for example, the screen in the dry season due to static electricity caused by the motherboard short circuit, requiring frequent repairs. The antistatic coating forms an insulating barrier on the screen surface, blocking the arc from directly impacting the internal components and ensuring the stability of the equipment. Therefore, in the energy industry, outdoor terminals generally use electrostatic coating solutions to maintain more than ten years of life.
3. Optimize touch efficiency
Traditional industrial touch screen is prone to contact offset under electrostatic interference. For example, when operating the display in winter, static electricity leads to an increase in the error rate of information entry on the display. The antistatic coating, however, is characterized by uniform charge conduction, which ensures that touch signals are transmitted without delay. Therefore, it is well suited for public service areas and warehouse management.
4. Extreme environmental adaptability
Industrial scenarios are often characterized by oils, high temperatures or corrosive gases, and coatings need to maintain their performance under harsh conditions. For example, in a food processing plant, screens need to resist water vapor penetration while preventing static-absorbed dust from contaminating the production line. The antistatic coating is used in combination with tempered glass and explosion-proof film to combine abrasion and chemical resistance.
Golden Margins –Entire Range of Touchscreen Products
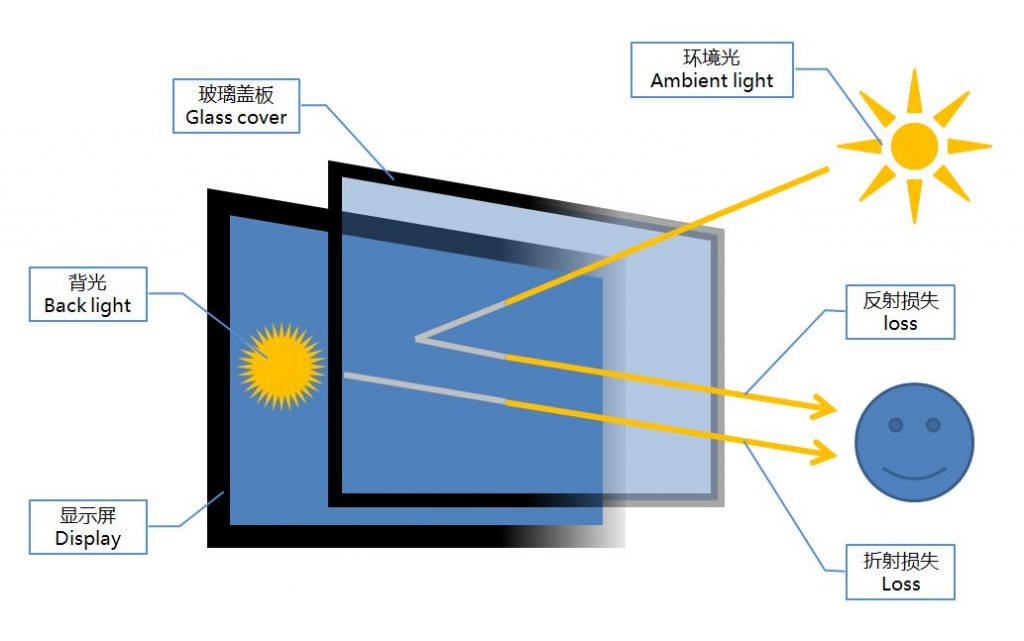
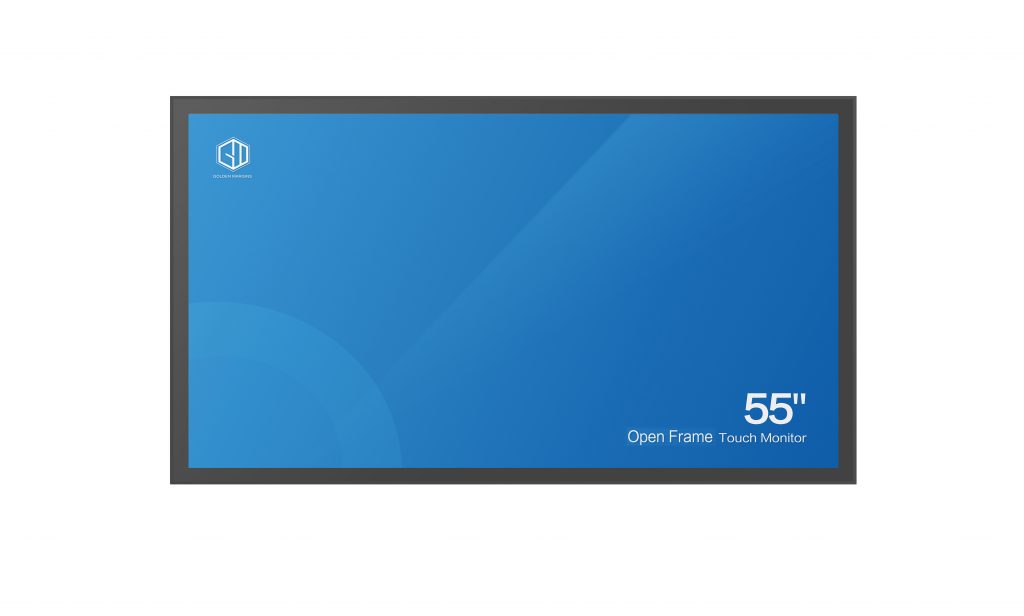
We hope you found these touchscreen or panel PC fundamentals informative. Goldenmargins offers a broad selection of Industrial Touchscreen Monitors and Touch Panel PCs in various sizes and configurations, including medical touch screens, sunlight-readable touch screens, open-frame touch screens, and waterproof touch panels, as well as other unique touch screen or panel PC designs. You can learn more about our services HERE or by calling us at +86 755 23191996 or sales@goldenmargins.com