Pixel Density of Industrial Touch Monitors
On the industrial shop floor, in the control room or in the laboratory, the screen of an industrial monitor influences the operator’s operation. When people talk about the performance of display devices, the pixel density (PPI) is often simply understood as the higher the better, but in fact it is not, and the pixel density varies depending on the usage scenario. Choosing the right PPI can avoid visual fatigue and effectively reduce costs.
1. Pixel density misconceptions in industrial scenarios
High PPI screen in the field of consumer electronics, such as cell phones, is a selling point, but in the industrial scene may be counterproductive. A 400 PPI precision display, if used for 2 meters away from the equipment status monitoring, tiny text and icons will be overly dense due to the pixel can not see. Conversely, a 100 PPI display used at a close quality control station will have pixel grains that cut through image detail like a screen grid. Operators are forced to frequently adjust the angle at which they lean forward, which not only reduces efficiency, but also raises health concerns.
Screen clarity does not equal comfort. But in industrial scenarios, operators need to be consistently comfortable and readable, not tested to the limit. Practical experience shows that controlling the PPI at 70%-80% of the theoretical value of the distance (about 200-250 PPI) can avoid pixel granularity and reduce the visual oppression caused by high-density pixels.
2. Selection of Pixel Density
For multi-tasking positions that require simultaneous handling of near-operation and long-range monitoring, a layered design is more effective than a single high PPI .In the main operation area, a small to medium sized touch screen with 250-300 PPI can be used to ensure the accuracy of finger clicks. In the remote monitoring area, a large screen of 150-180 PPI can be used to make up for the lack of pixel density by enlarging the key information modules to improve efficiency.
3. Factors affecting pixel density
1. Ambient light interferes with the PPI requirement. Under strong light environment, such as outdoor, the reflected light of high PPI screen will aggravate visual fatigue. At this time, reduce the PPI appropriately (e.g., from 250 to 180), and change to frosted surface screen + high contrast UI design, but can improve readability.
2. Screen material. Certain industrial displays can improve visual clarity at the same PPI through sub-pixel rendering technology, and OLED screens can utilize self-luminous properties to reduce halo interference between pixels. Quantum dot coatings can weaken the jaggedness of low PPI through purer color transitions. These technologies allow a 200 PPI screen to present a viewing experience close to 250 PPI, providing optimized space for cost-sensitive scenarios.
Golden Margins –Entire Range of Touchscreen Products
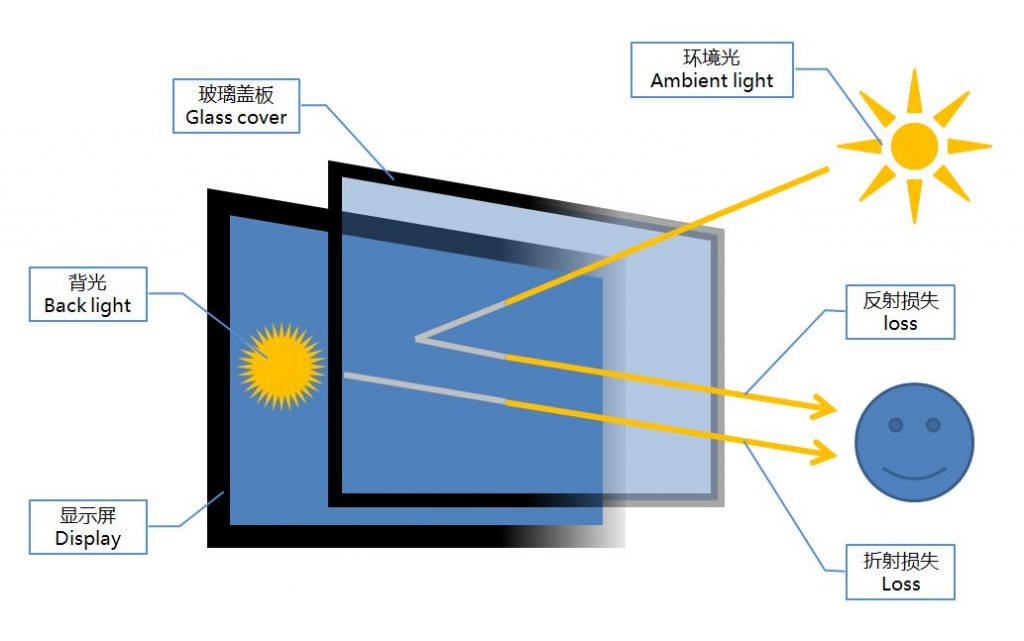
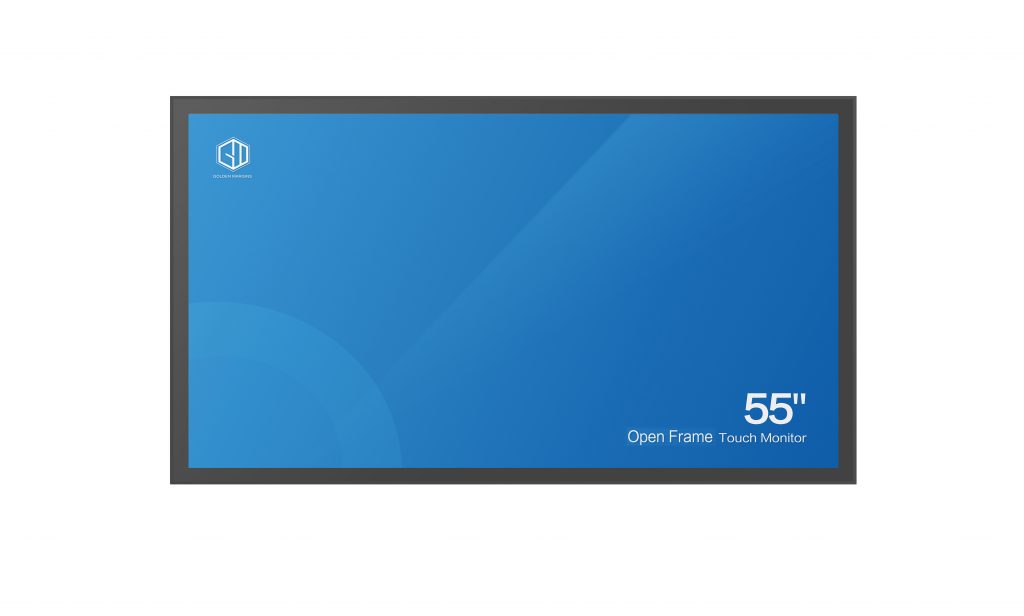
We hope you found these touchscreen or panel PC fundamentals informative. Goldenmargins offers a broad selection of Industrial Touchscreen Monitors and Touch Panel PCs in various sizes and configurations, including medical touch screens, sunlight-readable touch screens, open-frame touch screens, and waterproof touch panels, as well as other unique touch screen or panel PC designs. You can learn more about our services HERE or by calling us at +86 755 23191996 or sales@goldenmargins.com